This article will use a case study as an example of one of the many cases seen in the field with a range of different manufacturers’ seals to provide a checklist of considerations for applications where product containment is essential. Legislation surrounding leakages from rotating equipment sealing devices has led to the introduction of more stringent regulations, particularly relating to emissions and health and safety issues. Upgrading single seals to more compliant technology for mature assets has evolved from being a reliability issue into a requirement to provide effective containment, or prevention of the process fluid leaking to atmosphere. In addition to selecting more modern sealing devices, there is often a need to introduce or upgrade a seal auxiliary system to further manage the risk of process fluids reaching the atmosphere. One such instance occurs when wet or dry secondary containment seals have been incorporated in addition to the primary seal faces that seal the process fluid. Dry containment seals1 have gained popularity over the past two decades. Specifically the refinery sector has used this technology for limiting emissions without incurring the cost of more traditional liquid dual mechanical seal auxiliary systems.
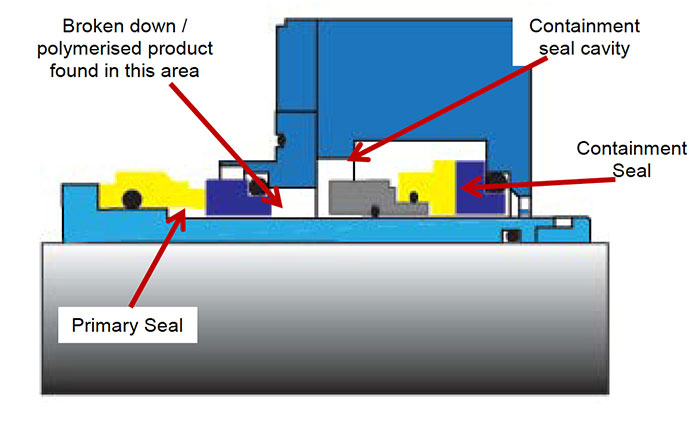
Case History
A petrochemical plant had installed a containment seal on a process pump that contained Butadiene as the process fluid. No seal support system was applied. However, a pressure gauge was fitted to the containment seal cavity. The seal operated at a temperature of 44 C, a seal chamber pressure of almost 8.2 bar(g) and a speed of 2,920 rotations per minute (rpm). After four years of operation, the seal catastrophically failed, and it was reported that there was a fire on the pump in question. The seal was returned for inspection where the following was discovered. The primary (inboard) seal faces, although appearing scored and phono grooved, were intact. This suggested that the primary seal did not catastrophically fail, although heavy leakage could not be ruled out. Abraded damage to the primary seal faces means that flatness was barely measurable. The abraded damage to the seal faces could have been a consequence of heavily contaminated process leakage or degraded product build-up within the containment seal cavity. The containment (outboard) seal faces were totally destroyed, suggesting a catastrophic failure of the containment seal. Heavy build up of what appeared to be degraded process fluid was found within the containment seal cavity and around the outside diameter of the sleeve. It is suspected that this build up is a consequence of years of normal process fluid leakage over the primary seal faces into the containment seal cavity. The process fluid had then broken down (polymerised) once subject to atmospheric pressure and ambient temperature within the cavity. The seal had been operating without any auxiliary system support for the secondary containment seal. A pressure gauge was used to monitor any increase in pressure within the containment cavity should the primary seal suffer high leakage. If the primary seal had suffered excessive leakage, this would have led to either excessive vapor leakage to the atmosphere or a back pressure within the containment seal cavity, depending on the quality of the leaked process fluid. If the containment seal was still in good condition to contain the process leakage from the primary seal, the pressure gauge should indicate a pressure increase providing the reference line to the gauge was not blocked. There were no reports of a pressure increase on the pressure gauge. This indicates that either the primary seal was still operating in a satisfactory condition or that the pressure reference line was blocked.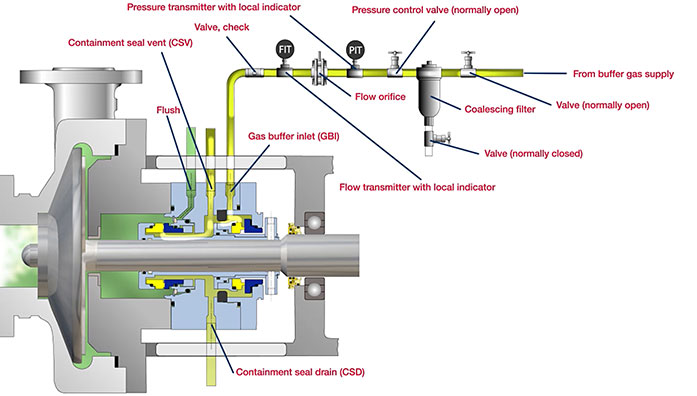
Containment Seals
In 2002, dry containment seals were recognized in the second edition of API 682. A series of piping plans offered to take leakage to a safe collection point. The basis for a containment seal is an Arrangement 2 seal (two seals per cartridge assembly with a liquid buffer fluid) with an API plan 71 seal support system as a minimum requirement (i.e. without buffer gas feed). The introduction of a buffer gas is covered with API Plan 72 and the collection/disposal of process leakage is covered by API Plan 75 and API Plan 76 (see Figures 2 through 4).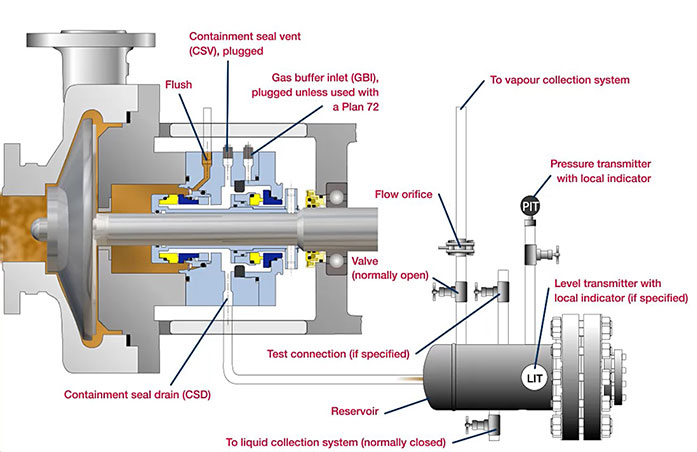
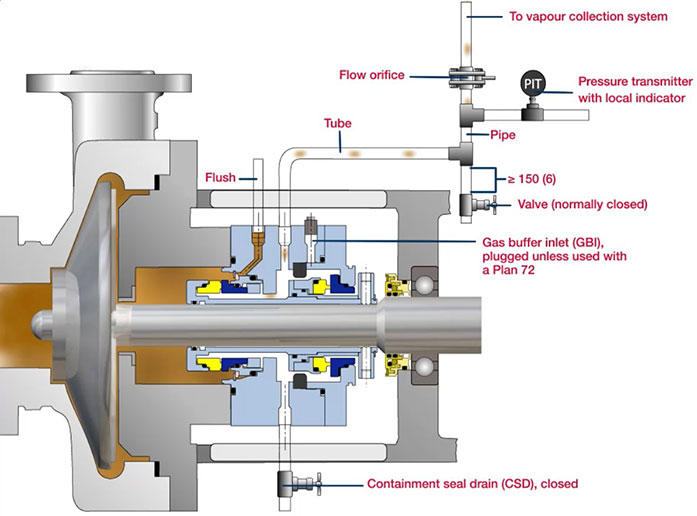
Wet Dual Seal with Unpressurized Seal Auxiliary System
Plan 52 is a wet dual unpressurized seal (Arrangement 2) where the buffer fluid (liquid) fills the space between the primary seal and the outer seal (see Figure 5). Plan 52 is intended to be connected to a flare system so that the gaseous emissions that separate from the buffer fluid in the collection vessel can be vented. The 4th Edition of API 6824 specifies transmitters for both pressure and level, thereby offering a means of condition monitoring the primary and secondary containment seal simultaneously.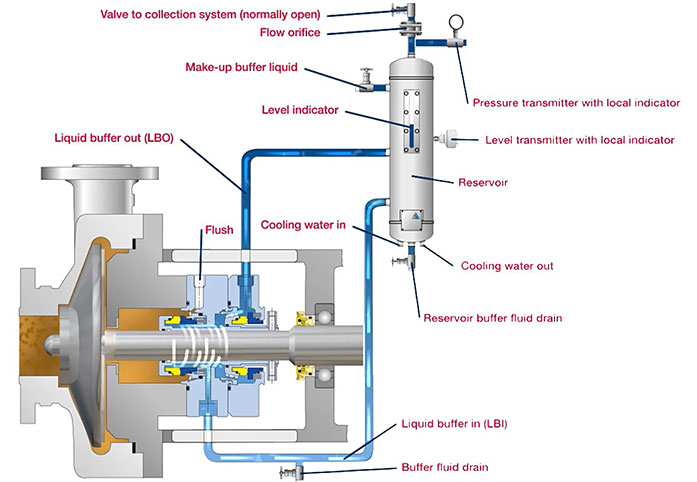
Dual Seals with Pressurized Seal Auxiliary System
The principal difference between a dual seal with a pressurized and unpressurized containment seal auxiliary system is that with a pressurized system, both the primary and secondary seals will be sealing a clean, non-hazardous barrier fluid. With an unpressurized containment seal, the system is managing the hazardous (and/or contaminated) leakage from the primary seal. One benefit of this type of system is that in the event of a pump being accidently dry run (not an uncommon occurrence in tank farm product transfer, or off-loading), both the primary and secondary seals remain lubricated and therefore will survive. Pressurized dual seals are becoming increasingly common. The cost of the supporting systems of pressurized dual seals has become more comparable with unpressurized containment seals, especially when considering the cost of utility connections. The barrier fluid of the system can be either a non-compressible liquid (Plan 53 A, B or C) or compressible gas (Plan 74).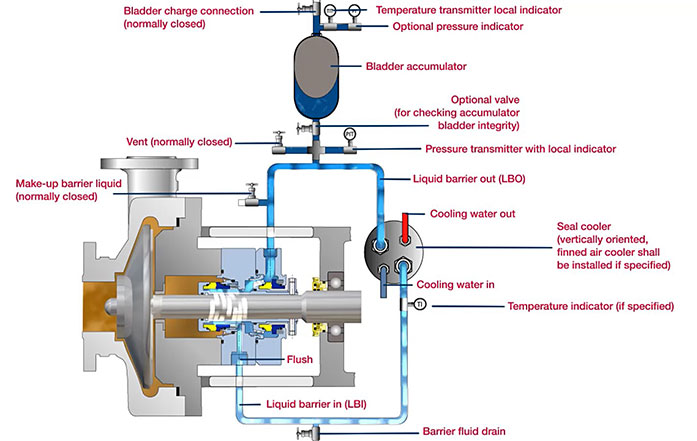
Sealing System Fault Tolerance Comparison
Table 1 compares typical containment seals against other typical dual seal arrangements (see page 36). Various typical scenarios are presented along with the alarm strategy that would be used and the effect of the condition. The traffic light color coding illustrates areas of concern. In particular, Table 1 focuses on a major event where the seal leakage is high (so-called catastrophic). Generally of equal importance is the prolonged integrity of the secondary sealing device since this ultimately prevents or restricts the leakage of large amounts of process fluid into the atmosphere. In the case of containment seals, the condition of the secondary seal at the time of the primary seal’s failure—along with monitoring devices—will dictate how long containment is likely to last (if at all) and hence whether process leakage will be prevented prior to shutdown and isolation of the equipment. Kalfrin and Gonzalez2 recommend protocols: testing containment seal integrity to detect a potential hidden failure of the outer seal. It is recommended to establish and adjust testing frequencies. Fone and Bowden3 recommended containment seal integrity testing to be conducted on a weekly basis—such frequency would probably be impractical, however, as with any spot check testing the condition of the containment seal is only known at the point of testing.Conclusion
Secondary containment seals should be operated with particular attention to control the normal primary seal process leakage collection. Operating them with an appropriate API plan as stated in API 682 is always key to ensure safe collection or disposal of the primary seal process leakage. In the example case study shown, the ideal solution would be to upgrade the seal and seal support system to a dual seal with a pressurized seal support system, which would ensure the integrity of both the primary and secondary seal.- For the purpose of clarity we have used the American Petroleum Industry standard API 682 4th Edition definition of a containment seal i.e. ‘Containment Seal – Special version of an outer seal used in Arrangement 2 and that normally operates in a vapor (gas buffer or no buffer) but will seal the process fluid for a limited time in the event of an inner seal failure’
- API 682 4th Edition
- API 682 Arrangement 2 Configurations – Considerations for Outer Seal and Support System Design. B. Kalfrin and L. Gonzalez Presented at 45th Turbomachinery & 32nd Pump Symposia. Houston, Texas, USA Sept 2016
- Bowden, P. E. Fone, C. J. Containment Seals for API 682 ISO 21049 Proceedings Of The 19th International Pump Users Symposium. 2002, Turbomachinery Laboratory pp 67-84.