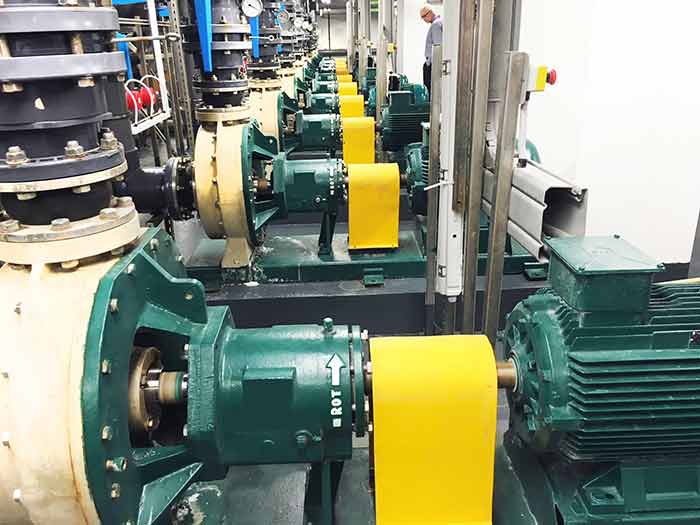
When picking the right pump for chemical applications, there are many factors to consider. True, for many mid-to-large-scale industrial fluid transfer needs, a good-quality conventional single-stage centrifugal pump with a mechanical seal at the drive-shaft opening is perfectly adequate. Probably two-thirds or more of all industrial pumps in use today are of this type. How often the seals and inside components need to be replaced depends on the nature of the fluid—its chemical composition, corrosiveness, viscosity and temperature among other factors. The good news is that, due to ANSI standards, pumps of this kind are interchangeable, which means they can be replaced as needed—at a cost. Typically, the first point of failure in a conventional chemical pump is the mechanical seal. During normal operation, the life of a mechanical seal is two to three years. However, depending on operating temperature, fluid properties and amount of solids, a mechanical seal can fail within three to six months. If the pumped fluid is hazardous to personnel, equipment or the environment, the fluid leakage from failure could be catastrophic. This fluid leakage can be curtailed by using an inside mechanical seal with external flushing. The flushing and draining system can be costly and the operator must control and/or contain any drained fluid.
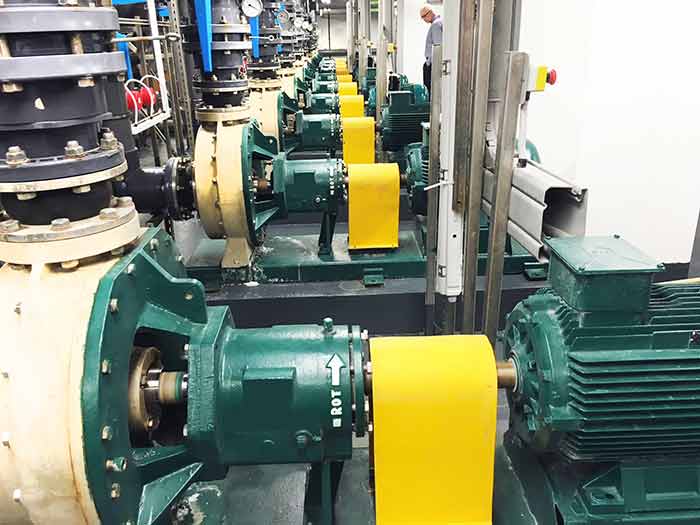