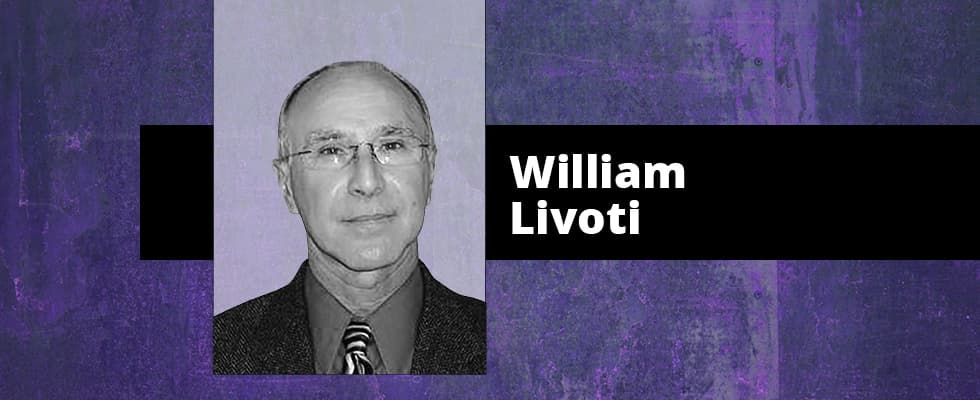
It’s been a while since my last article—May of last year to be exact. Unforeseen circumstances prevented me from continuing with my monthly column, but I would like to pick up where I left off in “Selecting a Pump Repair/Service Shop.”
Not all pump repair shops are the same. Each individual shop has specific skill sets and limitations. Selecting the appropriate shop(s) (it is wise to have several to choose from) for your repairs depends on several factors. This is where the vendor qualification/selection process becomes interesting, as the on-site audit inspection requires validating what was discussed during the phone/email correspondence as well as additional information and observations. We will go into this in detail in future articles.
There are many types of pump repair shops. Each has their pros and cons. Which type is best for your specific needs? It all depends on your specific needs and expectations.
Take time to prepare for the site visit. If you or your team do not feel qualified, seek out a qualified third party. Develop a checklist of questions as well as specific observations you wish to verify. Do not trust your questions to memory. A site visit is necessary to physically validate what was shared during the interview and in emails, as well as additional information based on the type of pumps you need repaired.
The on-site inspections allow you to visually verify the building, lifting capabilities, equipment, etc., but what other critical information is needed to ensure you have selected the appropriate repair facility? Asking the right questions up front can save you down the road.
This portion of the audit process requires asking specific questions of the entire staff, as well as observation of how the staff interacts. Prior to the visit, prepare a checklist of areas you wish to visually verify along with the questions you want to ask. How the staff responds to the questions will speak volumes of the capabilities and workmanship the facility produces. In addition, visually verify documentation, specifically the QA/QC manual, as-found/as-built reports, shipping and receiving documentation, work orders (to shop) and inspection reports. The heart of any business is the people; a pump repair facility is no exception. You can have a state-of-the-art facility with top-of-the-line equipment; however, without well-trained, dedicated people to staff the facility, you have nothing but a lot of overhead.
In the pre-assessment, specific questions were asked regarding the service center capabilities, quality control methodology and people. What questions would you want to ask the staff while on-site? Remember, trust but verify. Using the interview questionnaire, have the list of questions, go through the list and request verification of their interview response.
Take the opportunity to meet with facility staff. During this segment of the visit, one must be sensitive to the subject matter and somewhat discreet. A few sample questions to give an idea of what to ask would be: Do you enjoy working here? Have you had training on QA/QC protocol? Have you been through safety training?
The manager may tell you one thing, but reality is something else. It is amazing what you hear from the workers. You may think this is being sneaky or underhanded. If so, I remind you of the ramifications if a critical pump fails under your watch.
Phone Interview Questionnaire
1. What types of pumps do you repair at your facility?
a. vertically suspended pumps
• single casing
• double casing
• in-line casing
b.overhung pump types
• flexibly coupled
• rigidly coupled
• close coupled
c. between bearings pump types
• 1 and 2 stage
• multistage
2. Are you a distributor for any pump manufacturers?
a. If so, which ones?
b.Are you certified to perform pump repairs for the manufacturers that you represent?
c. Do you have access to certified drawings from said manufacturers?
3. Do you have a test stand to performance test the pumps post repair?
a. If so, is your test stand certified by Hydraulic Institute?
b. Do you maintain a list of measuring/testing equipment?
• Is your equipment calibrated on a regular basis?
4. What is the largest pump for which your service center is fully equipped to repair and test in house?
a. What is your maximum lifting capacity?
b. What is your maximum lifting elevation?
c. Do you have a stacking pit?
d. Do you have two-plane balancing equipment?
• If so, what is the largest rotating element that you can balance?
5. Do you have a coordinate measuring/inspection machine/device?
6. How many employees do you have and what are their experience levels?
a. __________ number of employees
b. __________ maximum number of years of experience
c. Do you have a degreed pump engineer on staff? What is his/her name, years of experience and where did he/she gain his/her experience (pump OEM)?
7. What supplemental training or professional development activity is offered to service center employees?
a. in-house training or structured mentoring (describe)
b. off-site short courses, workshops or seminars one or more days in length
c. subsidized evening or part-time classes at college or trade school
d. attendance at trade conferences or conventions
e. other
8. How much training or professional development do service center employees receive?
a. ___________ percentage of employees receiving off-site training annually
b. ___________ average days off site
per year per employee receiving off-site training.
9. What trade or professional associations is your service center a member of?
10. Do you have a formal quality management system involving third party inspection and certification? Do you have a Quality Manual and/or published directive?
11. Do you have the capability of taking any brand of centrifugal pump and returning it to OEM conditions via reverse engineering and knowledge of pump hydraulics?
12. Do you use Six Sigma protocol or similar process?
13. Do you have a safety program in place for shop and field work?
14. What are the qualifications of your field service personnel?