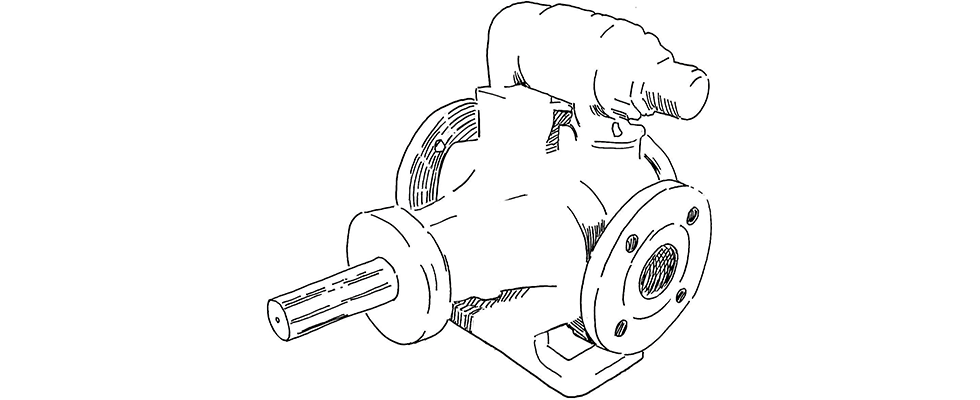
There are many considerations when selecting the right pump for chemical applications. When working with materials such as corrosive or flammable chemicals, extra care should be taken to ensure that the product selected is suitable.
Define the Fluid Characteristics
The safety data sheet (SDS) and chemical manufacturer or chemical distributor can provide required information such as fluid name, concentration, fluid temperature, specific gravity and viscosity at pumping temperature. If solids are present, determine at what concentration, particle size and hardness, and if the material is corrosive, flammable or combustible.
Describe the Application
The more detailed the description, the better. Make sure to verify:
- What type of container is the chemical stored in? Is it a drum or tote, bulk storage tank, rail car or tanker truck?
- Where will the fluid be moved? From a drum to a bucket, from a rail car to bulk storage, or simply recirculating in the same container, for example.
- Is the liquid below the pump? In this case, a pump that is either self-priming or one that can be submerged in the liquid is needed.
- What is the flow rate required? Flow rate is required to calculate friction loss in the piping system.
- What is the total head or pressure required? Total head is based on the piping system and is used (along with flow rate) to help choose a pump.
- What is the net positive suction head available (NPSHa)? It is the suction head made available to the pump and provided by the piping system. To avoid cavitation (causes erosion damage to pump components) the NPSHa must exceed the NPSH required (NPSHr).
- How long will the pump be operating per day or week? This is important in evaluating energy costs. For example, if a pump is going to be operating many hours per day, a pump driven with an electric motor could have considerably lower operating costs compared to an air-driven pump.
- Is it indoors or outdoors? What are the maximum and minimum ambient temperatures? This is important for the correct selection of the construction materials for the pump and motor.
- What is the altitude? Higher altitudes reduce available lift if it is a self-priming application, reduces NPSHa and reduces cooling by an electric motors fan.
Pump Selection
There are many variables to the selection of the best pump type with the correct materials of construction.- Gather information on the fluid to be pumped.
- Gather information on the hydraulic and application requirements.
- Consult the experts. Consult with the chemical manufacturer, chemical distributor, pump manufacturers, local pump distributors, and even industrial supply catalogs that are experienced in the selection of chemical pumps.
Review Possible Pump Types
Here are some of the most common pump types for transferring chemicals.
Drum/barrel pumps: Ideal for transferring a wide variety of chemicals from pails, drums, totes [(such as intermediate bulk containers (IBCs)] and other containers used by chemical manufacturers to transport products to the user. These can be powered by electric, lithium ion battery or air motors.
Centrifugal pumps: Provide smooth flow and have a wide range of flows and head capabilities. These pumps are available in a wide range of materials and either mechanically sealed or sealless magnetically coupled. They are typically operated with electric motors.
Air-operated double diaphragm pumps: Versatile, simple to operate, and can pump solids and viscous fluids. They typically operate with compressed air.
Positive displacement pumps: Includes gear, rotary vane or piston pumps. These pumps are good with high viscosity fluids and can generate high pressures.
Selecting Proper Materials of Construction
The proper materials of construction are critical to safely transfer chemicals and provide a long life. Here are some common examples of materials used for chemicals.
Metals
- Stainless steel: 304 and 316 are used; 316 has increased corrosion resistance.
- Hastelloy C/Inconel/Alloy 625: This contains high nickel and chromium levels and up to 13 percent molybdenum. It has better corrosion resistance than stainless steel but is more expensive.
- Titanium: This works best in oxidizing media such as hot nitric acid and sodium hypochlorite and is expensive.
Plastics
- CPVC: Chlorinated polyvinyl chloride (CPVC) is a thermoplastic that can be processed using injection molding technology. It has reasonable corrosion resistance and is used in piping, valves, filters and pumps.
- Polyethylene: Versions of cross-linked polyethylene (XLPE) are used for chemical storage tanks, chemical transfer hoses and can be found in low-cost, hand-operated drum pumps.
- Polypropylene: Polypropylene is resistant to many corrosive materials. It is used for piping, fittings and pumps used in the transfer of corrosive fluids.
- PVDF: Polyvinylidene fluoride (PVDF) is a strong, abrasion-resistant fluoropolymer with outstanding chemical resistance. It is used in piping, fittings, pumps and instrumentation.
- ETFE: Ethylene tetrafluoroethylene (ETFE) is a fluoropolymer with better chemical resistance and a wider temperature range than PVDF. It is used to line pipe, valves and pump housings and can be injection molded into a variety of products including pumps.
Elastomers
- Nitrile (Buna N): A general-purpose oil- and water-resistant rubber with a moderate working temperature range, nitrile is not compatible with many corrosive materials.
- FKM: FKM is a fluorocarbon elastomer with extensive chemical compatibility that spans considerable concentration and temperature ranges, making it good for many applications.
- EPDM: Ethylene propylene diene methylene (EPDM) rubber is compatible with most caustics and has a good temperature range.
- FFKM: Perfluoroelastomers (FFKM) are the elastomeric form of PTFE that are fully fluorinated providing a high level of corrosion resistance.
Other materials
- Ceramic: Alumina ceramic (aluminum oxide) is commonly used in mechanical seals and as thrust rings, shafts and bushings. Higher purity (99.5 percent) alumina demonstrates enhanced wear and corrosion resistance.
- Alpha sintered silicon carbide: Alpha sintered silicon carbide (SiC) offers superior hardness, high strength, high abrasion/wear resistance and excellent corrosion resistance.
- Carbon graphite: Carbon graphite offers good chemical resistance, even to many that are extremely corrosive. Used in mechanical seals and as a bushing material in other pump types.