Foreign materials in sewage system led the maintenance team to look for a new equipment option.
BJM Pumps
03/27/2018
We have all seen it in movies—prison inmates sneaking cigarettes and other contraband from one person to another while guards are not looking. While these scenes from cinema may be highly dramatized, the reality is that goods do get smuggled throughout prisons and correctional facilities.
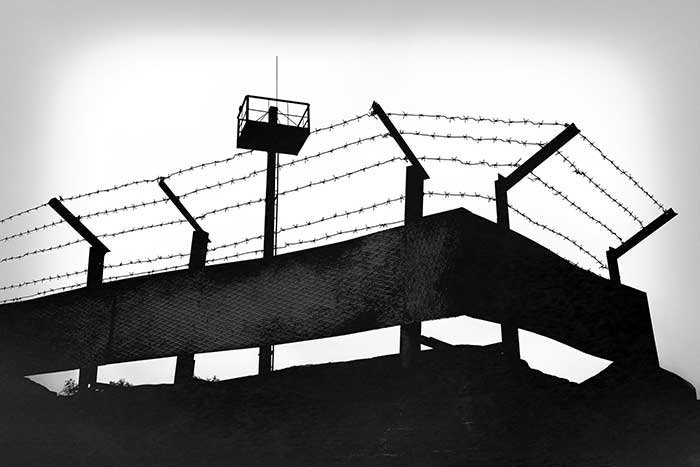