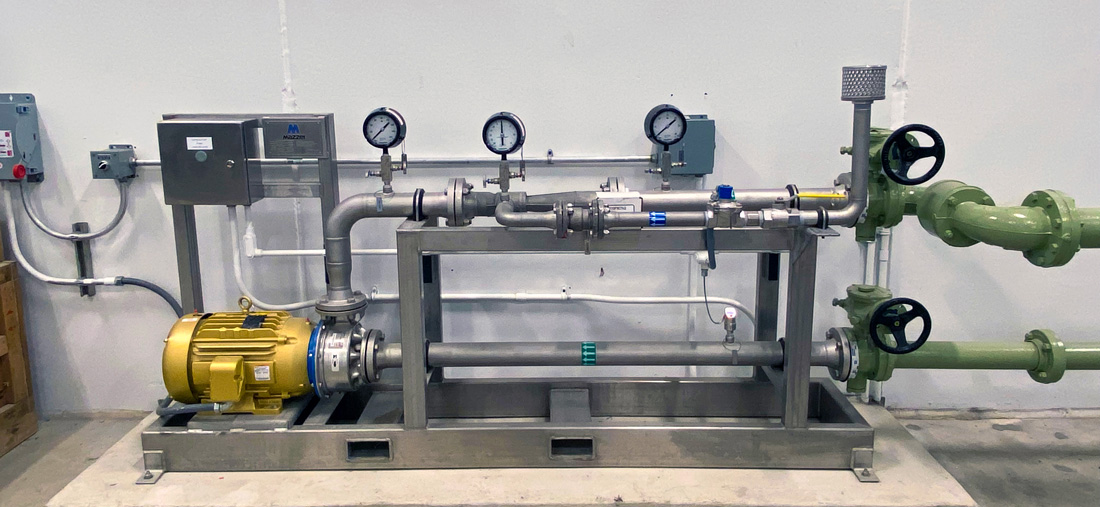
Aeration can be a valuable tool used to reduce various contaminants found in groundwater. Just as aeration improves the efficiency and effectiveness of filtration and purification systems downstream, careful selection and design of the aeration system itself can enhance its efficiency.
Managing Chlorine Demand
Three common contaminants—iron, hydrogen sulfide (H2S) and ammonia—can increase chlorine demand in water treatment systems. All three create taste, odor or staining nuisances, and iron and ammonia can also present public health hazards by contributing to biofilm growth. Pretreatment with aeration can control all three contaminants and reduce chlorine consumption at later stages of treatment.
Reducing the chlorine dose is more than just a cost saving action. As more chlorine is dosed, a plant is more likely to exceed maximum contaminant levels (MCLs) set for disinfection byproducts (DBPs), such as trihalomethanes (THM).
Iron and H2S can be oxidized by oxygen from atmospheric air and have relatively low oxygen requirements—0.15 milligrams (mg) of oxygen (O2) for 1 mg iron and 1 mg of O2 per 1 mg H2S.
Good practices dictate that an additional oxygen buffer of 4 to 5 mg/liter (l) be present in addition to the amount required for oxidation to encourage faster and more complete kinetics. Ammonia is more challenging, calling for approximately 4.6 mg of O2 for 1 mg of ammonia. A common design rule is that for each 1 mg of ammonia, 10 mg of chlorine is required, so break-point chlorination can be a more expensive method of ammonia reduction when compared to aeration.
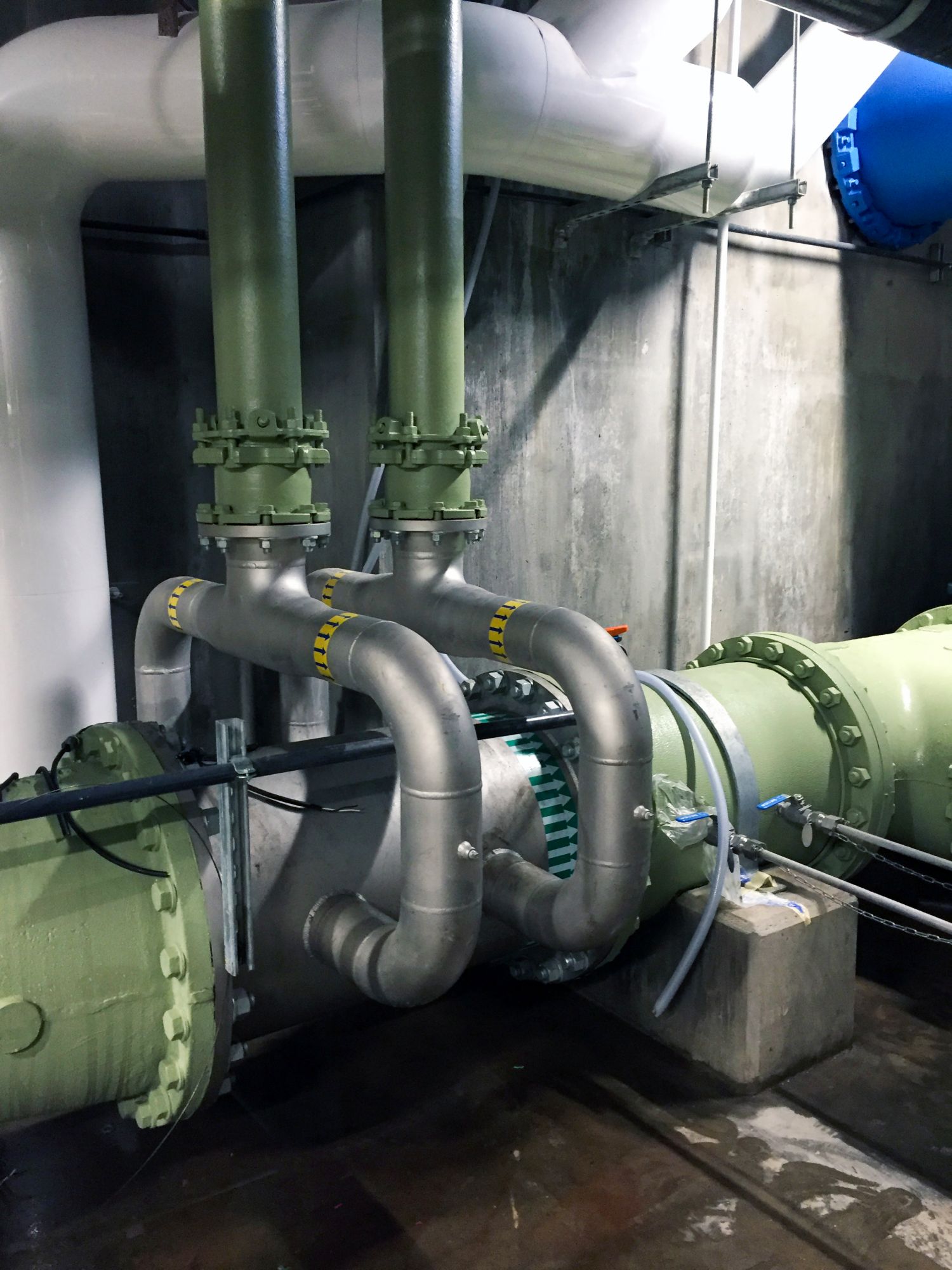
Achieving Higher DO Levels
Sidestream injection, using venturi technology, along with a pipeline flash reactor (PFR) or pipeline nozzle manifold (PNM), can be a cost-effective way to reduce footprint and maintenance and achieve higher dissolved oxygen (DO) levels.
A typical sidestream injection system consists of one or two air injection skids and a PFR or PNM. A skid-mounted booster pump draws a sidestream from the mainline and pumps it through the skid-mounted venturi injector, which uses the flow of the water to create a vacuum that draws atmospheric air into the sidestream. The water/gas mixture is then blended back into the mainline through a stainless steel PFR or PNM that employs high velocity mixing nozzles to aggressively mix and uniformly transfer the oxygen into solution on the mainline. The PFR/PNM does not contain any static mixing elements or any moving parts, so maintenance is not an issue, and there is almost no mainline pressure loss across the unit.
Scalability is another benefit of PFR/PNM systems, which are often designed with a spare sidestream connection to allow for the addition of a future air injection skid.
If contaminant concentrations increase or water flow rates grow to exceed design peaks, the air injection skids can simply be converted to oxygen injection skids by adding an oxygen source, such as liquid oxygen (LOX) or an on-site oxygen concentrator, to achieve higher DO levels.
Beauty & Efficiency in South Dakota
In 2017, ground was broken on the expansion of a water purification facility in Yankton, South Dakota. The new facility was designed to use reverse osmosis (RO) technology to achieve high-quality drinking water for groundwater flow rates up to 10 million gallons per day (mgd) with a large iron concentration. To reduce chemical costs and lighten the load on the RO membranes, the raw water is first sent through an aeration step, retention tank and multimedia filtration.
The plant faces a challenge beyond the technical demands of water treatment. It is located in an existing city park on a beautiful stretch of the Missouri River, so
it was important to the city to have a facility that could seamlessly blend in with both the park and the surrounding downtown area.
When evaluating aeration equipment, it became apparent that there was no convenient location to install a large draft aerator. The only possible location would have required the replacement of an aesthetically pleasing clock tower.
The design engineer was familiar with in-line gas contacting systems used for ozone applications and was happy to hear that the same equipment could be effectively used for aeration systems. In the end, the aeration equipment consisting of two air injection skids and a 24-inch PFR was conveniently installed out of sight in the building’s basement.
The system was started up in 2020 and is able to sufficiently aerate the raw water to oxidize up to 2 mg/l of iron that is subsequently removed by the multimedia filters.
Fighting Fouling
At a 1.6 mgd groundwater treatment facility in Iowa, an in-line diffusion system was being used for pre-filter aeration to treat iron and ammonia. The highest DO level that could be achieved with the diffusion equipment was 3 to 4 mg/l. This low DO concentration was not sufficient to support complete nitrification inside the filters, and as a result, the remaining ammonia was driving up chlorine demand and inhibiting the plant’s ability to maintain a stable chlorine residual in its treated effluent.
Diffuser fouling had become a major issue. Plant managers tried to deal with fouling by using two diffusers so one would operate at all times while the other could be taken out of service for cleaning. Even with frequent cleanings, the diffusers appeared to have reached a point beyond repair.
At this particular plant, there were a few challenges. The water was being pumped directly from the well into pressure filters without the use of a retention tank. Since the nitrification of ammonia has a relatively high oxygen demand, elevated levels of DO were desired.
This was a retrofit situation, so there was little space for additional equipment. Due to the limited footprint and desire to maintain mainline pressure, a draft aerator was not a viable option.
In the fall of 2019, a one-skid in-line aeration system with a 10-inch PFR was installed and commissioned. The system was designed to increase the DO to 7-8 mg/l prior to entry into the multimedia filters—enough oxygen to support the biological activity necessary to achieve full nitrification from ammonia to nitrate. The air injection skid was controlled by a variable frequency drive (VFD) so the system could be optimized to achieve the desired DO level without using any unnecessary pumping energy.
With their small footprint, scalability and minimal maintenance demands, sidestream systems with venturi injectors are becoming increasingly popular for aeration—improving the efficiency not only of downstream treatment systems but of the aeration process itself.