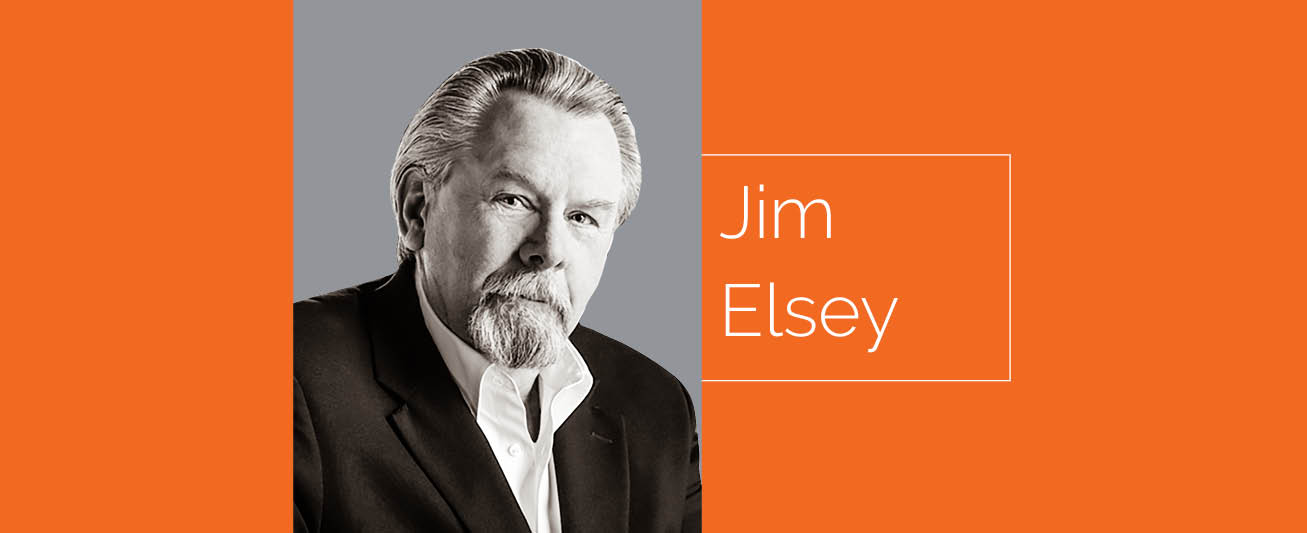
I’m not here to tell you what to do; I just want you to make an informed decision. Like many of my columns, this one is a corollary from reader’s comments to a previous column. In the August 2017 issue of Pumps & Systems, I laid out my thesis as to why I prefer slow-speed pumps when and if possible. Reference point: I am referring to motor speeds based on 60 hertz 2 pole versus 4-pole induction speeds (1,750 versus 3,550 rotations per minute [rpm]).
Review
If you haven’t read the 2017 column, it is important that I acknowledge that it is often necessary and prudent to use high-speed pumps. High-speed pumps can be more efficient and possess a markedly smaller physical envelope for the same hydraulic conditions. Depending on the duty cycle, the pump with higher efficiency will yield a keen return on investment (ROI) that is especially welcome in today’s energy-hungry world.
As a rule of thumb, a pump rated to perform at some given value of head and flow can be physically reduced to half the size if you double the speed. The smaller size of the high-speed pump translates to a reduced footprint and lower initial cost.
Antithesis
I propose that slower pumps can often be more reliable, meaning they will experience a longer life and require less maintenance during that period. These reliability benefits will also translate to ROI savings, though it may take more time than some corporations have the patience for. Convoluted logic will focus solely on the initial costs, thereby irresponsibly shifting the inevitable increased maintenance and operating costs to others. To summarize, compare initial cost versus total cost of ownership (TCO) for the expected life of the pump.
One Opinion
When asked about my preference on pump speed, I normally state that I am from the camp of “it depends.” There is a long list of variables in the overall decision process to be considered.
Do I have any empirical data to back up these claims? The short answer is I have knowledge of one formal study that supports my thesis involving over 100 American Petroleum Institute (API) class pumps mentioned by Allan R. Budris in an article he wrote some years back. I regret that I do not have a copy of the study.
In another study presented by the late Dr. Elemer Makay for Electric Power Research Institute (EPRI) on boiler feed pump stability, his abstract stated the following: “Feedwater pumps must be designed for stable operation over the full range of possible flow rates, even at the cost of some reduction of efficiency at best operating point.” Note that there are many other important points in the over 60 pages of his report.
Decision Process
Appreciate that the question of high speed versus low speed is not an easy one to answer, and many experts will postulate their own theories. There are many who disagree with my “sometimes slower is better” thesis; however, all I ask is that you consider all the factors in the equation before deciding.
Given all the pump application considerations, I recommend a thorough review of each factor/variable and then assigning a weighted exponent or multiplier. There are so many factors to consider, you cannot in good conscience decide solely on the speed factor. I suggest putting all variables into a spreadsheet and computing a solution. The outcome will help you decide, based on objective data converted to analytic information versus subjective emotional choices.
Measuring
Like any good Six Sigma exercise, the data you select in the evaluation is not valid unless there is measurement. One of the common axioms from pump engineering is that the pump wear factor is proportional to the speed factor cubed. Stated as: Wear α (RPM)3. [If you are not familiar with the symbol “α”, it is the lowercase Greek letter alpha, and, in mathematics, it signifies “is proportional to.”] This wear thesis and expression are commonly used in rheological applications where the liquid is classified as a slurry. Other common maxims are that wear is proportional to the velocity of the liquid, and wear is indirectly proportional to the hardness of the material.
It is not my intention for the column to dive down the rabbit hole of rheology, so I will end that sidetrack here except to state that I will often use rheology factors as a tool to predict potential pump wear and reliability regardless of the liquid properties.
To play along, you will first need to assign a factor (F), and that is the tricky part that should be based on experience, educated/calibrated guesses and/or empirical data. As an imperfect illustration, consider wear α [(F)3 x (RPM)3], where F is substituted into the previous expression. Assume you are pumping clean water; one perspective would be to assign the factor F as a magnitude of 1, so 1 cubed is still 1. As another example, a given liquid class 2 slurry might be assigned a magnitude 3, so the result would be 27. Note that the actual speed remains a factor in my example. There are many alternative mathematical routes to design your own equation; this one is just a simple example.
The conclusion here is that, depending on the liquid properties, your resultant wear factor will be different. However, don’t forget the overall salient point that even if the liquid is clear water, there are many other forces and stresses on the pump that compound with increased speed.
What are some of the main factors to consider? I covered net positive suction head (NPSH) and impeller tip speed in detail in my August 2017 column. Thinking along the lines of the affinity laws, note that hydraulic performance within the preferred operating envelope (range) of a pump, NPSH varies approximately as the square of the speed ratio. So, if the NPSH margin was already small at low speed, it will certainly be unacceptable at higher speeds.
Part 2 will cover specific speed, mitigating and dynamic forces, inertia and more.
References
Centrifugal Pump Hydraulic Instability EPRI Report CS-1445 Research Project 1266-18 by Dr. E Mackay 1980