For more than 50 years, air-operated, double-diaphragm (AODD) pumps have played a role in many companies’ modern global manufacturing and fluid-handling operations. The original pump concept has changed little over time and works because of its simple operation and construction. With a major focus on operating improvements and cost reductions from businesses, AODD pump manufacturers have introduced new air distribution systems (ADS) to increase pump efficiency and meet these demands. The new ADS technologies range from electronic controls to mechanical innovations. However, the resulting savings in compressed air usage and increase in pump efficiency vary for each system. This article presents the results of head-to-head comparisons of AODD pumps with different ADSs and the final data acquired during those tests. The results help illustrate the impact that different ADS technologies have on air consumption, energy use and overall flow rate.
The Challenge
In AODD pump operations, energy use is directly related to the rate at which the pumps use air to drive each stroke during the pumping cycle. With increasingly high energy costs, facility operators understand that the initial purchase and installation of a new pumping system is only a small part of the total cost of ownership (TCO) and operation. The routine costs of energy and maintenance remain the primary cost drivers in the TCO.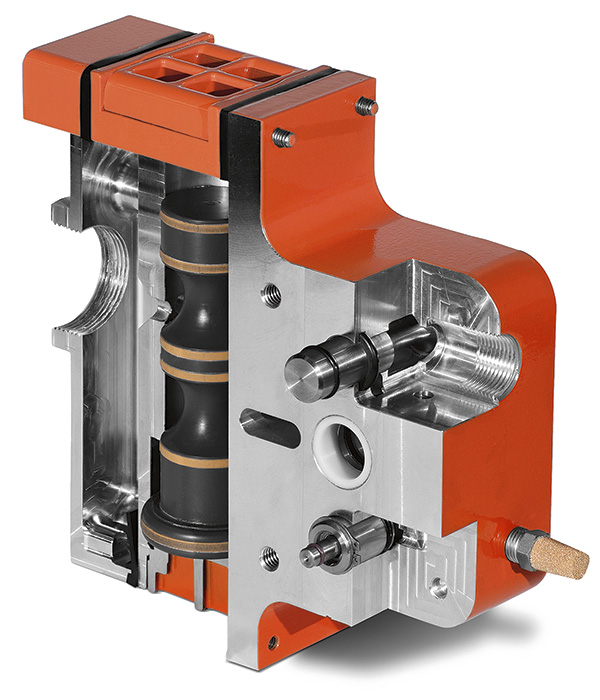
The Controlled Comparisons
To create real-world conditions to measure the effectiveness of different ADS technologies industry-wide, a controlled, objective head-to-head test was arranged comparing several AODD pumps that were fitted with traditional, electronically controlled and mechanically actuated ADSs. Common conditions of service that are seen in the field were replicated in the laboratory. This simulated application required each pump to produce a flow of 320 liters per minute (lpm)—85 gallons per minute (gpm)—against a head pressure of 2.1 bar (30 psi). To achieve a fair comparison between these competing pumps, each pump was run at the inlet air pressure needed to meet the common condition of service. Air-consumption data was then recorded (see Table 1 for the results for four pumps).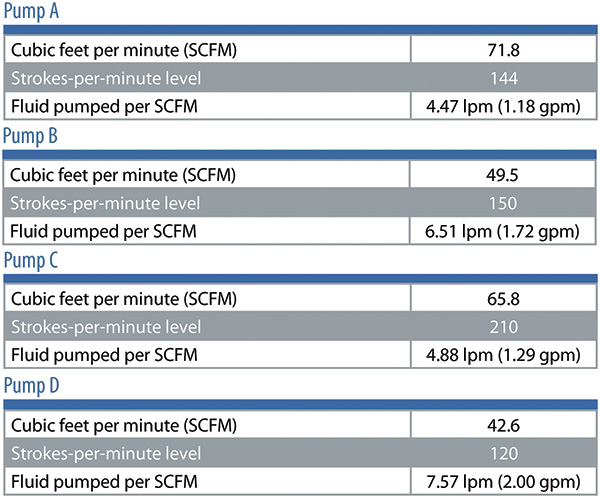
The Solution
The data gathered in the objective AODD testing show that Pump D—which used the ADS that restricts air flow into the filling air chamber to minimize wasted compressed air—had better performance in all three points of measurement. It had the lowest air consumption in standard cubic feet per minute (SCFM), the lowest strokes per minute and the highest volume of fluid pumped per SCFM. Pump D averages an overall 30 percent reduction in air consumption compared with Pumps A, B and C. It also provides the largest reduction in air consumption among the four pumps while still managing the best overall volume of fluid moved per stroke, requiring the fewest strokes per minute. The air-restricting ADS in Pump D is a new way to look at how pneumatic pumps operate. To combat overfilling, the ADS used in Pump D restricts the air flow into the filling air chamber at the end of the pump’s stroke, which minimizes the compressed air that is wasted. The air control spool of this ADS meters the air to prevent overfilling without reducing product yield.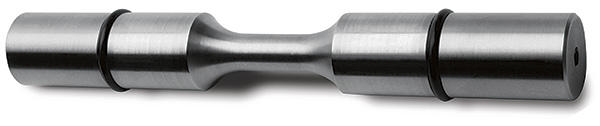
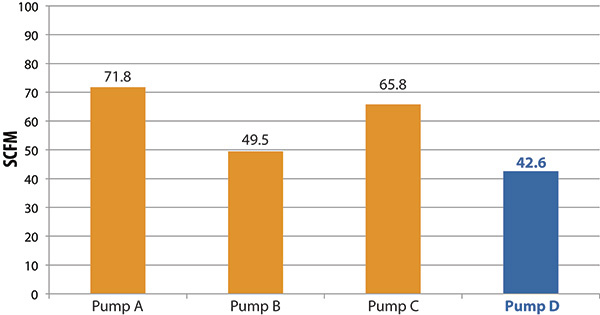