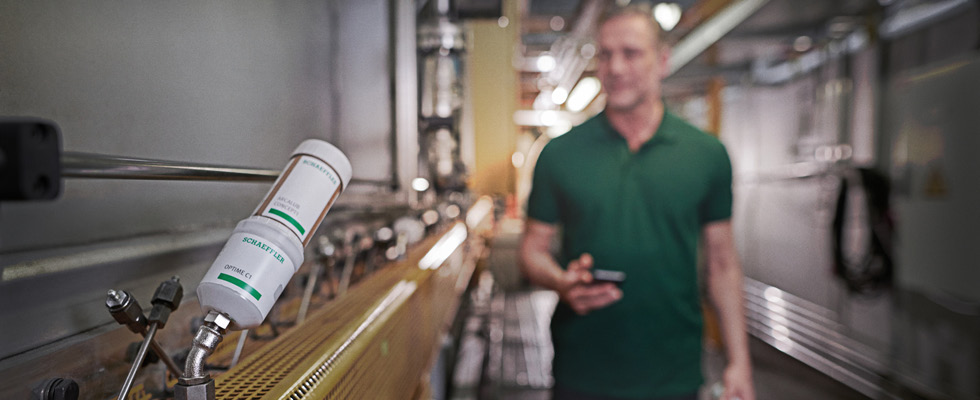
Problems with lubrication are one of the leading causes of early bearing failure in balance-of-plant rotating equipment such as pumps, compressors, fans and electric motors. Over 50% of bearing failures can be traced back to issues originating with lubrication problems,1 despite years of effort to integrate lubrication into the regular cadence of a reliability-centered maintenance program. Clearly, there is something missing in efforts to properly lubricate rotating assets.
Many manufacturing plants utilize a route-based, manual lubrication program. This typically involves having a technician work from a list, visit each lubrication point and manually apply lubrication where needed. While there are advantages to this method, as the technician can visually inspect each machine, it also presents some obvious potential shortcomings.
Recent advances in smart, automatic lubrication systems are changing this paradigm. With a focus on reliability-centered maintenance principles, a smart lubrication system can become an integral part of a proactive maintenance program.
Shortcomings in Current Practices
A proper lubrication program consists of four key elements:
- Identifying the appropriate lubricant for the application
- Identifying the appropriate lubrication points
- Defining appropriate relubrication intervals
- Defining appropriate lubrication quantities
Determining the appropriate lubricant requires knowledge of the bearing application, anticipated loads the bearing will experience and expected shaft speeds. This is often determined by the OEM based on their machine ratings. While it is wise to follow the OEM’s guidance, varying operational environments may warrant deviations from OEM recommendations—which is a science unto itself and outside the scope of this article.
Identifying lubrication points should be straightforward. When developing a maintenance plan, every bearing that requires lubrication must be documented, and a mitigation task for addressing each bearing’s lubrication needs should be created.
But this is where the first shortcoming crops up: What if a bearing is hard to reach? Will that bearing always receive the attention it needs in a route-based manual lubrication system?
This leads to lubrication intervals. Based on loads and speeds, how often does the bearing need to be relubricated? Even with a correct interval, should the bearing be checked in between those times? Doing so uses scarce maintenance personnel who could be performing other tasks. Even worse, does the interval get skipped entirely because maintenance teams are too busy? If so, the bearing gets lubricated only irregularly. What effect does this have on the life of the bearing?
Finally, what is the appropriate quantity of lubrication? With greased bearings, it is not uncommon to see a maintenance technician manually pump in grease until it starts squeezing out of the bearing. But is this best for the bearing? Will excess grease have a negative effect on bearing life? Ultrasonic tools are available to “listen” to the bearing as grease is being pumped in. Once the noise level drops below a certain value, the technician knows to stop applying grease. While these tools have proven successful, they require patience and effort to be effective.
How Does a Smart Lubrication System Work?
Smart lubrication starts with an automated lubricant delivery device. In its simplest form, this device has a single output delivery port and a reservoir cartridge filled with lubricant. Gas generated via a controlled chemical reaction inside a special cell in the reservoir forces the lubricant out of the cartridge through the lubrication line to the bearing. The chemical reaction rate in the cell can be adjusted to dispense the lubricant at a controlled pace over time periods ranging from one month to one year, depending on the requirements of the bearing.
This method ensures lubricant is dispensed in a continuous, controlled manner, thereby avoiding the peaks and valleys of manual lubrication (over-lubricating, then running nearly dry, then over-lubricating again, etc.).
While these types of lubricant delivery devices have been around for some time, what makes this system smart?
- Wireless infrastructure: Smart lubricators need to be installed within a wireless network, analogous
to a common Wi-Fi system. For industrial devices such as smart lubricators, this wireless infrastructure is sometimes referred to as an Internet of Things (IoT) wireless system. It is commonly used to support wireless vibration sensors for monitoring the condition of rotating machines. - Motorized pump base: The addition of a battery-powered base to the lubricant delivery device is required to make this system “smart.” The base is equipped with both a motorized pump for dispensing the lubricant as well as a radio for communicating with the wireless IoT infrastructure.
Data from the smart lubricators and other IoT devices is transmitted via a gateway to the cloud. This allows the user to view a dashboard via a web browser to monitor the status of all connected devices. Perhaps more importantly, the user can receive mobile alerts for anomalous events such as a blocked lubrication line or a cartridge running low on lubricant.
Reliability-Centered Maintenance
This capability transforms lubrication into an “on-condition” maintenance task, which aligns well with a reliability-centered maintenance program. Lubrication becomes a condition-based maintenance item rather than a routine task. Technicians no longer need to walk routes checking on individual lubrication points that may not even need attention.
Instead, they receive alerts about lubrication problems, assess the criticality of the problem based on the alert category and take appropriate mitigating actions. Enabling a focus on high-priority tasks, this is a much more efficient utilization of maintenance personnel than simply checking lubrication points manually.
A smart lubrication system is an integral component of a proactive, reliability-centered maintenance program. Conventional lubrication programs are ultimately reactive. By the time an anomaly is discovered, there is little to no planning time to address the issue. Conventional lubrication programs are also inefficient, requiring maintenance personnel to routinely check lubrication points that may not need service. A smart lubrication system addresses these shortcomings by making lubrication a condition-based task, thereby enabling maintenance technicians to prioritize tasks that truly need attention.
References
Katz, S. (2010, May). Bearing Failure & Analysis, Pumps & Systems. pumpsandsystems.com/bearing-failure-analysis.