Water is the lifeblood of agriculture, and the lack of it can limit the productivity of an otherwise economically attractive piece of property. Therefore, getting water to the crops is a critical part of a grower’s job and often represents a major cost. When pumping is necessary, the cost of getting power to the pump and the cost of electricity for operation can be significant. Foster Family Vineyards in Lewisburg, North Carolina, is the largest grape supplier to the largest wine-making operation in the southern U.S. The vineyard was faced with the challenge of irrigating with efficiency in mind. The company was pumping deep-well water from two 400-foot wells at 30 gallons per minute. But this rate was insufficient to adequately serve the 70 acres of vines, and the power consumption was expensive. To ease the cost of pumping well water, vineyard management wanted to take advantage of a creek on the property. But estimates showed the costs at $8,000 to $10,000 per pole to run electrical wire from the nearest access point to the creek, which was located in a low-lying spot on the property approximately a half-mile away. From this creek, a pump would send the water to a holding pond on higher ground, approximately 75 feet above the vineyard and 2,500 feet away. Vineyard management looked for a solution that would reduce installation costs and the vineyard’s dependence on the local power grid. Open to using new technologies, the team thought that this application may be a good candidate for a solar-powered pump system. The company found a provider who had experience with solar power. At the same time, they learned about an available university grant that would help fund the project and submitted an application.
Solar System
A pump manufacturer introduced vineyard employees to a possible technology solution (see Figure 1). Key to the system’s capability is its variable frequency drive (VFD) control that runs the pump at varying speeds to achieve the most possible flow at all times of the day, regardless of the solar array’s momentary electrical power output fluctuations.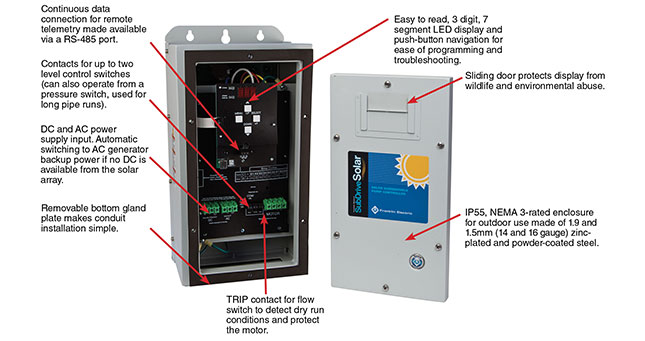
System Details
The solar solution employed at the vineyard powers a 200-volt (V), 3-phase, 60 hertz, 4-inch submersible motor. The system runs between 190 V and 330 V DC, which is typically supplied by four to 10 standard solar modules. The pumps have flow rates between 5 and 90 gallons per minute (gpm) and can pump from 1,000 feet in some lower-flow applications. At about 100 gpm the systems are still able to produce 30 pounds per square inch (psi) of operating pressure. Thanks to the VFD-based control unit, the pump systems often run from sunrise to sunset with few interruptions.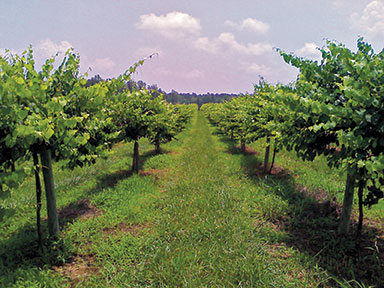