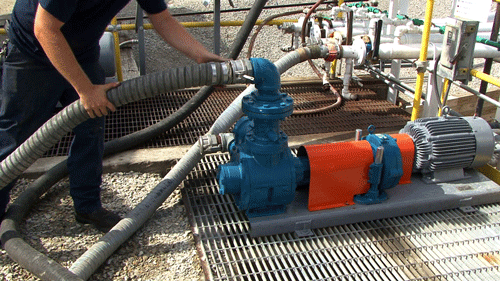
There is no way around it. If someone is a part of an industrial sector with processing pumps, they will more than likely encounter solvents. Solvents serve as a reactionary compound, one designed to dissolve other substances to create a new mixture or to create other chemicals. The nature of solvents requires deliberate care to ensure they are processed properly without creating detrimental effects to your equipment or staff.
Solvents come in many varieties, most in thin liquid form, that allow common products to function properly and optimally. Examples include paints that dry quickly and maintain their integrity for a long time, industrial cleaners and degreasers. Industries that commonly deal with solvents include oil and gas, wastewater, automotive and coatings and paint among many others.
While certain pump technologies can process solvents, many operators opt for centrifugal pumps. Most operators are familiar with the technology and its ability to effectively handle water-like fluids, such as solvents. Because they are widely available, centrifugal pumps also have a reputation for being a cheaper solution than other pump technologies.
This article will discuss why positive displacement sliding vane pumps are another pump technology worth considering when it comes to solvents.
Centrifugal & Sliding Vane Pumps
Centrifugal pumps, one of the oldest pump technologies, use kinetic energy, velocity and momentum to transfer liquids. These pumps require an engine or electric motor to power them, creating enough energy to rotate an impeller to move fluids. Fluid enters on the suction side of the pump and moves into the impeller chamber. As the impeller and its blades rotate, it creates momentum for incoming fluid.
The casing, which encloses the impeller, has a volute-shaped passage of increasing area, collecting the liquid leaving the impeller and converting a portion of its velocity energy into additional pressure. This casing passage leads to the discharge nozzle of the pump, where it is then forced into the discharge piping. Centrifugal pumps are common in liquid transfer and process applications, with many operators citing its wide operating range.
Sliding vane pumps feature a rotor with a series of vanes that retract and slide out as the rotor turns. This sliding motion creates chambers into which the liquid flows, and as the rotor turns, the liquid is moved to the outlet where it is discharged as the pumping chamber is squeezed down. Each revolution of the rotor displaces a constant volume of fluid with little chance for slippage. Variances in pumping
pressure have little effect on the sliding vane pump’s flow rate, and the open-flow profile provides a gentle and low-shear environment within the pump.
Sliding vane pumps’ operating principles allow them to offer volumetric consistency throughout their operational life, as well as the ability to handle a wide range of liquids, including ultra-thin liquids (0.2 centipoise [cP]) up to 22,500 cP without compromising its performance.
Why Centrifugal Pumps for Solvents?
Centrifugal pumps are a tried-and-true technology for multiple liquids, including solvents. These pumps feature a compact, robust design that allows them to process solvents of all kinds. One example will use phenol, a solvent, to show the effectiveness of a centrifugal pump when it comes to the processing and transferring. Phenol is made from petroleum-derived feedstocks and is used to manufacture several end products, including epoxies, detergents, herbicides, cosmetics, sunscreen, aspirin and numerous pharmaceutical drugs.
While phenol is indispensable in the production of many common products, it requires diligent handling due to its harmful nature if it contacts skin. Additionally, phenol is difficult to control because of its innate characteristics.
Specifically, phenol freezes around 90 F (32 C). As it reaches that temperature, it begins turning into a slushy liquid, which can disturb a pump’s functionality. Centrifugal pumps can handle phenol effectively because they can stay above phenol’s freezing point temperature and have an optimal flow rate to ensure the substance continues without interruption. Some centrifugal pumps can achieve flow rates as high as 1,400 gallons per minute (gpm), or 320 cubic meters of gas per hour (m3/hr), and can handle materials with a maximum temperature of 450 F (232 C), sometimes even higher, depending on the pump manufacturer.
Centrifugal pumps are also one of the most affordable pumping technologies for handling liquids and solvents, providing efficient processing power in a compact package. The compact nature of centrifugal pumps also allows operators to fit them easier into facilities without dedicating an abundance of space for each one.
Another benefit of centrifugal pumps is familiarity. They serve as one of, if not the most popular processing pumps in the world, meaning many operators are already well-versed in using them. That familiarity also extends to maintenance, as many operators can handle whatever problems might arise down the line because of their prior experience with them.
Additionally, centrifugal pumps are capable of continuous duty and have contact elements typically only within the shaft seal. This allows centrifugal pumps to outlast similar types of pumps.
Centrifugal Drawbacks
Despite the effectiveness of centrifugal pumps in handling solvents, the technology does have some drawbacks. The phenol example is one of them. When it comes to handling phenol, many operators will select sealed American National Standards Institute (ANSI) centrifugal pumps.
The drawback with using these types of centrifugal pumps comes down to the mechanical seals, which can be prone to failure from vibration or radial load during operation. Roughly 80% of all pump failures start at the seal, which can cost up to $3,000 to replace. If a mechanical seal must be replaced repeatedly throughout the year, that ancillary cost can quickly climb, especially if the entire facility uses the same technology.
Phenol is also hazardous. If the pump needs to be serviced, an operator must flush and decontaminate the pump before the work begins, leaving the pump offline for several hours to as much as 10 hours. Sealed pumps, however, are cheaper than the sealless variety, allowing operators to outfit their processing facilities with more affordable technology. These pumps will still perform well, but have their limitations.
A sealless centrifugal pump addresses most of those shortcomings when handling phenol but does not prevent others from surfacing. For instance, if the pump cavitates during operation, or if the viscosity of the liquid increases, a likely possibility with phenol, the pump’s shaft and impeller will come out of alignment and cause a catastrophic failure.
Additionally, centrifugal pumps, while effective overall with a wide operating range, function at their best when operating within their best efficiency point (BEP). The BEP serves as the pump’s optimal operating point. While staying at this specific operating condition is advantageous, it is not a common expectation.
A centrifugal pump endures amplified loads when it does not operate near its BEP. These loads exceed the service factor of individual components, many of which are economically optimized for a narrow variance from the BEP. This can cause excessive stress on bearings and the shaft, leading to deflection, premature wear, rubbing contact, leak-path development and product contamination.
Magnetic drive centrifugal pumps are in a more precarious situation as they have bushings instead of external bearings, resulting in narrower BEP flexibility. Overall, having a centrifugal pump operate at or near its BEP is essential for its long-term reliability.
Why Sliding Vane for Solvents?
Sliding vane pumps are suited for thin liquids, which makes them ideal for solvent processing and mixing. These pumps are not prone to leaking because the design features few leak points, as well as tight internal clearances. Some pumps, as they age, will suffer from internal slip as the wear parts begin to erode.
With sliding vane pumps, internal clearances remain optimal because the vanes are designed to maintain a dynamic seal as they wear. As the vanes wear over time, the remains slide out of the rotor and maintain their contact with the cylinder. This allows for volumetric consistency during the pump’s lifetime.
Like centrifugal pumps, operators can choose between sealed and sealless sliding vane pumps. The mechanical seal is prone to breakdown over time on a sliding vane pump, as with other pump technology. The reason is that the mechanical seal is a wear part, so it naturally will erode with constant, repeated use.
Sealless pumps do not have this drawback. The lack of a seal means fewer leakage concerns, which is imperative for solvents, as many can be dangerous to operators and the environment. Without a seal, it is also one less wear part to replace. The composition of sliding vane pumps ensures there is no metal-on-metal contact, a feature that allows them to run dry and handle low-viscosity liquids. Because sliding vane pumps can run dry without galling or affecting pump life and performance, operators can line strip solvents from the pump and run a different solvent through the same pump without concern of contamination or product loss. That is a key benefit if an operator wants to use one pump for several solvents instead of having multiple pumps for different liquids.
The dry-run capability also pays dividends for operators when dealing with solvents. Most solvents have a low lubricity, meaning pumps that cannot run dry require a lubricating fluid before attempting to process solvents. However, because sliding vane pumps can run dry, the lack of lubrication from solvents is not a detriment. The technology can process it on its own, without the need for lubrication. Additionally, sliding vane pumps can also operate in either direction, providing operators with operational flexibility.
When it comes to liquids with low viscosities, sliding vane pumps do not require a minimum liquid viscosity. These pumps have a range from ultra-thin liquids (0.2 cP) to as thick as 500 cP. Small particulates also are not a concern, as sliding vane pumps can process them with up to 40% concentrations.
Sliding vane pumps also function exceptionally well under continuous cavitation in low net positive suction head (NPSH) applications. This plays a crucial role in solvent processing, as volatile liquids can be problematic for other pumping technology. Higher vapor pressure will cause other pump technology, such as centrifugal, to cavitate and erode the impeller. Sliding vane pumps handle multiphase vapor/liquid mixtures well because the flow through these pumps is gentler than comparable technology.
Sliding Vane Shortcomings
Sliding vane pumps are not perfect either, having their own shortcomings when it comes to solvents. This technology is dynamically actuated, meaning it relies on differential pressure to activate the vanes fully. If a sliding vane pump has a stable, steady flow, it will function optimally. With high viscosity applications, low differential pressure adversely affects a sliding vane pump’s performance, leaving it unpredictable and non-efficient.
These low pressures, those at or below 35 pounds per square inch (psi) (2.4 bar), can reduce flow capacity and suction vacuum, which means the vanes will not fully engage. Given the nature (and name) of the technology, if the sliding vanes do not slide as intended, the pump does not operate as intended.
While the combination of high viscosity and low differential pressures are tough on sliding vane pumps, the inverse of that creates its own problems. High pressure is not catastrophic to sliding vane pumps, as they need higher pressures for effective operation. However, excessively high pressures can aggressively wear away at the pumps and their internal components, such as the cylinder and vanes. The integrity of those components will suffer more than other non-positive displacement pumps.
The temperature range of sliding vane pumps also is not as vast as comparable technologies. Sliding vane pumps can function as low as -40 F (-40 C) and as high as 350 F (176 C) in most cases. Comparable pump technologies can exceed those thresholds without compromising their integrity.
When it comes to solvent processing and mixing, operators must weigh the benefits of each pump technology. Centrifugal pumps have been a go-to technology for operators when it comes to processing solvents and other substances; yet, many do not realize the value and advantages of sliding vane pumps. Both technologies will provide operators with the features they need to handle solvents.
Sliding vane pumps, while not as popular, should not be overlooked, given their versatile nature when it comes to processing thin liquids.