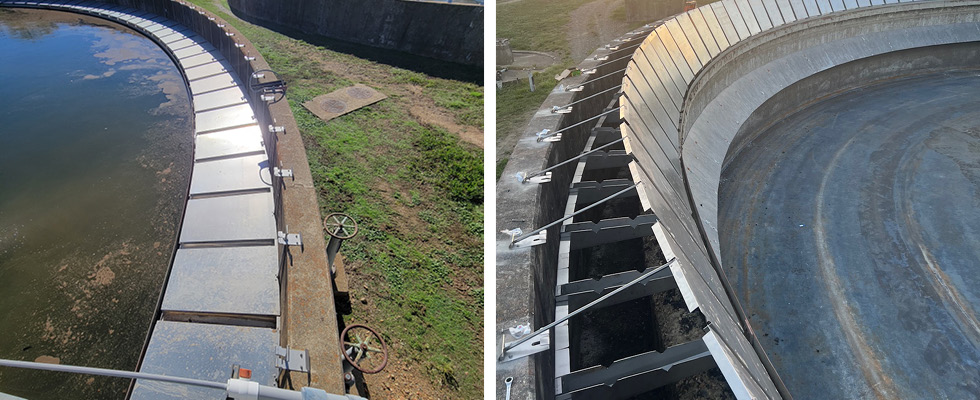
Challenge
A wastewater treatment plant in Hot Springs, Arkansas, faced recurring operational issues with excessive algae buildup on trough and weir surfaces, coupled with aging clarifier drives nearing the end of their operational lives. The equipment had deteriorated over decades of continuous use, leading to potential breakdowns, with noticeably reduced efficiency and escalating maintenance costs putting a strain on the facility. Replacing entire tanks and a clarifier system was a financially prohibitive option at the time, prompting the Hot Springs facility to seek a cost-effective solution that minimized downtime while restoring the equipment’s functionality.
Solution
In 2024, due to ineffective launder covers, the Hot Springs team noticed an excess of algae growth along weir and trough surfaces in some of their tanks. Algae blooms in wastewater tanks can be common, as wastewater often contains high levels of nutrients like nitrogen and phosphorus. These nutrients are essential for algae growth, and when combined with sunlight and warm temperatures, they will trigger significant algal blooms. This also contributes to sludge accumulation, increasing wear on the skimmer and other equipment. Instead of committing extra maintenance hours to routinely removing algae growth, Hot Springs searched for a more permanent and reliable solution.
A comprehensive evaluation of the Hot Springs facility was conducted by a repair and retrofit service provider, including a detailed inspection to identify the observable wear patterns, material degradation and potential functional weaknesses. During this assessment, a drive that needed to be replaced was identified, as well as one that needed to be rebuilt to keep the facility operating efficiently, reduce maintenance costs and prevent disruptions to the wastewater treatment processes.
After the assessment, it was recommended that the facility order three launder covers, a new clarifier drive and rebuild another clarifier drive. The launder covers and clarifier drive were installed, the clarifier unit on-site was dismantled, worn components were reconditioned and critical parts were replaced using either OEM parts or custom precision machining and upgraded materials designed to withstand the unique operating conditions in Hot Springs.
Implementation
The launder cover installation and drive rebuild process was initiated and ultimately completed with minimal disruption to the Hot Springs plant’s operations. The stainless steel covers were fabricated to be a modular design, enabling them to withstand extreme weather conditions while also allowing Hot Springs staff to remove individual panels and clean them as needed. In addition to the installation of launder covers, the drive was upgraded using corrosion-resistant coatings and upgraded seals to extend the life span of the facility.
Results
The Hot Springs facility’s equipment was restored to optimal performance, improving the plant’s efficiency. The stainless steel launder covers reduced algae growth along the trough surface by nearly 100%, eliminating the need for a brush system and drastically reducing time spent on what could have been prolonged maintenance. In 2025, the Hot Springs team plans to have new launder covers installed on their only remaining clarifier without launder covers, as well as to rebuild three other clarifier drives and retrofit their skimming mechanism to the upgraded design.
The installation and rebuild process allowed the Hot Springs facility to resolve its operational challenges efficiently and cost-effectively and find long-term solutions that will extend the life of critical infrastructure and minimize downtime, highlighting the value of professional equipment rebuilding.