Sealless centrifugal pumps with a magnetic coupling have become more popular among end users in the chemical industry. Rare earth magnets have reduced costs associated with magnetic couplings by decreasing magnet mass and required horsepower. This innovation has lowered the cost of the coupling and the overall operating cost. Seal failure is one of the most common causes of pump maintenance and downtime. If the seal fails, fluid escapes along the shaft that connects the motor to the impeller. Even when maintenance is scheduled, the pump must be taken out of service to replace the seal. While mechanical seal technology has improved over time, the innovations often require additional equipment. Double mechanical seals, either back-to-back or in tandem, are common for harsh conditions such as chemical pumping. Maintaining the barrier fluid in these designs often means purchasing barrier fluid tanks, controls and even additional pumps. Gas seals are another option but also require supporting equipment that poses the risk of failure. At first, end users only considered sealless pumps when handling hazardous fluids. The initial cost of a magnetically coupled pump far exceeded a conventionally sealed design. However, as time passed, operators became more concerned with total cost of ownership than preliminary capital outlay. Magnetically coupled pumps began to show a true cost advantage. Sealless designs replaced mechanically sealed pumps that required yearly removal for maintenance. Service intervals and mean time between failures extended. Emissions decreased, and safety improved. Operators now consider sealless pumps for services that they would not have just a few years ago—non-hazardous applications that are still difficult and costly to seal. In centrifugal pumps, the shaft transmits torque from the motor to the impeller. A seal prevents the pumped fluid from escaping down the shaft. The seal includes two parts, one stationary and the other rotating. Seal faces are typically made of carbon, tungsten carbide or silicon carbide (SiC). In a magnetic sealless pump, the motor torque rotates a magnet carrier, or drive magnets. The torque is transmitted through a containment shell to an inner magnet, or driven magnet. The magnet delivers torque to the impeller. The magnetic field creates eddy currents when it passes through a metallic container. Ceramic shells prevent eddy currents but can only contain a limited pressure. These eddy currents create heat directly between the magnets, and this heat must be dissipated.
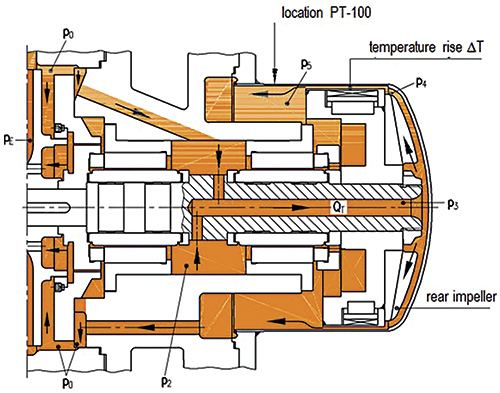
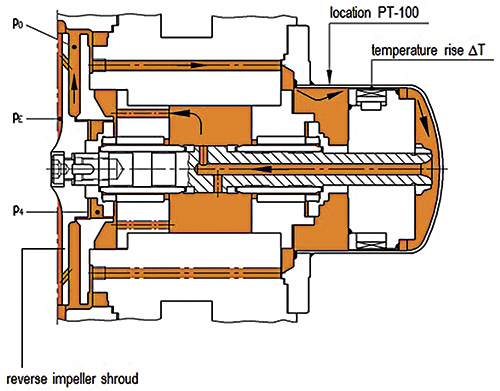
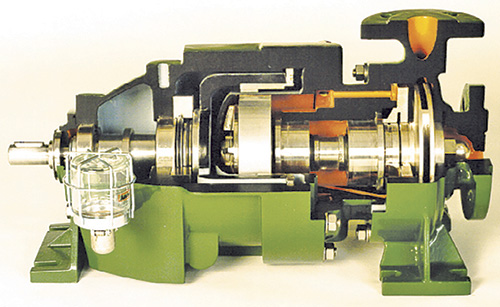
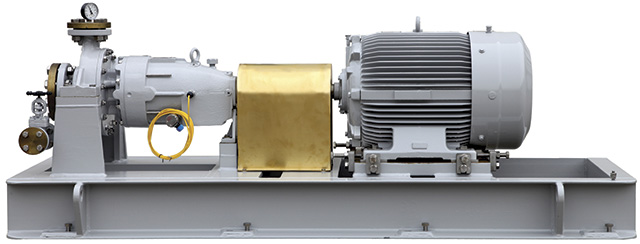