The Middle East and North Africa are home to one of the world's most sophisticated storage-terminal networks for refined petroleum products. The market is ripe for significant investment and expansion. Millions of cubic meters (m3 ) of independent tank storage will be made available in the region to support advanced recovery efforts among the region's maturing oil fields. For example, the UAE plans to double its tank capacity during the coming years. The Port of Fujairah recently expanded its storage capacity to 8.67 million m3 with plans to expand to about 12 million m3 by 2017. This expansion will give Fujairah the world's second-largest bunkering capacity behind Singapore's Jurong Island facility. This growth in terminal sites and overall storage capacity in the MENA region will increase demand for pumps. These pumps must be able to handle refined fuel products. At storage terminals, sliding vane pump technology provides the most efficient solution for optimizing throughput rates for refined petroleum products.
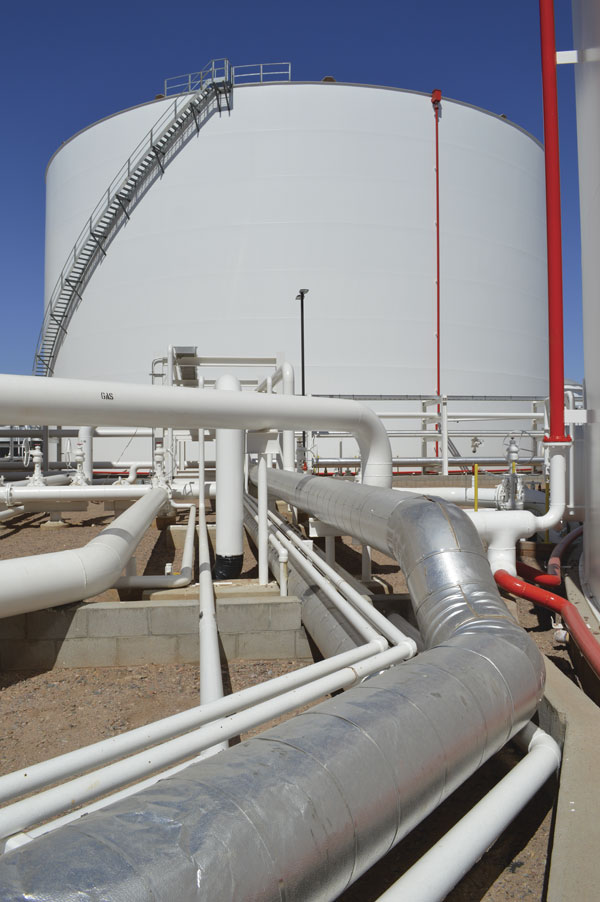
Centrifugal Pumps
Millions of gallons of refined petroleum products pass through MENA storage facilities on a daily basis. Terminal operators must employ a battalion of transfer pumps that operate reliably and cost-effectively at predetermined flow rates. While operators have several choices in the pump market, including centrifugal, gear and lobe pumps, storage terminal networks present unique challenges that must be considered when selecting equipment. Transfer pumps play a key role in the terminal's supply chain, but they are also the terminal's biggest energy consumers. According to a report from the UN Industrial Development Organization, pumps can account for up to 20 percent of total electricity use in the industrial sector, and a pumping system's average efficiency is about 40 percent or less. When efficiency is low, pumps consume more energy, produce more emissions and fail more often. At storage terminals, operators must maximize throughputs while using energy efficiently. Too many terminal operators still reflexively depend on centrifugal pumps, which are not the most energy-efficient choice for their application. Centrifugal pumps rarely operate at their best efficiency point (BEP)—the point when product flow rate and discharge pressure are equal around the pump's impeller and volute. As a centrifugal pump moves away from its BEP, the impeller experiences uneven pressure. The resulting radial thrust will cause the pump shaft to deflect. When the shaft deflects, excess load on the bearings can damage the mechanical seal and lead to uneven wearing of the gland packing or shaft sleeve. Once a centrifugal pump operates too far away from its BEP, cavitation occurs, which can quickly destroy the pump casing, back plate and impeller. Centrifugal pumps pose other challenges in storage terminal operations. Performance often suffers when pumping fluids with a viscosity higher than 400 centistokes. Flow rate control can become a serious maintenance issue. Low-flow centrifugal pumps consume more energy and require more pressure, while higher flow rates can lead to friction loss. Terminal operators often select oversized pumps for their application, increasing energy consumption and operating and maintenance costs.Sliding Vane Pumps
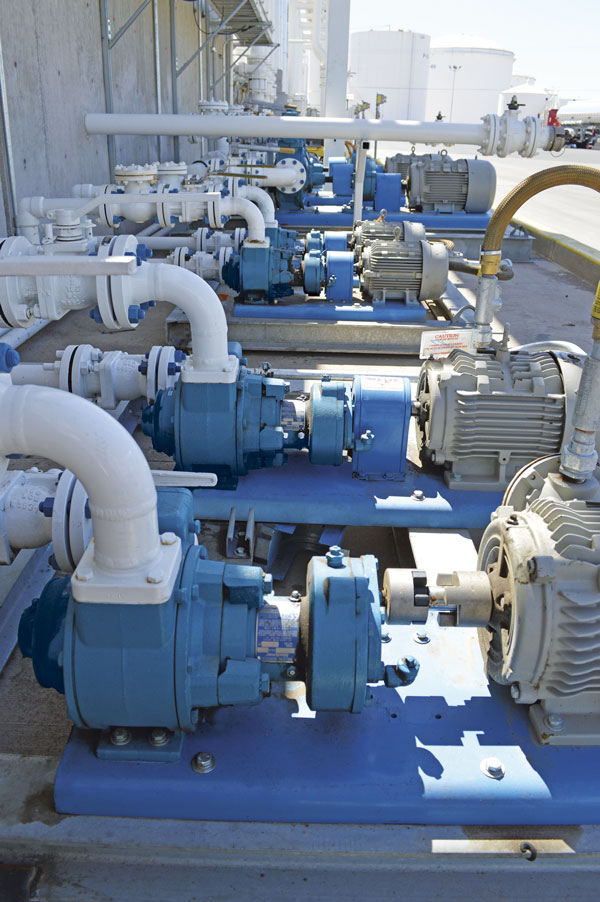