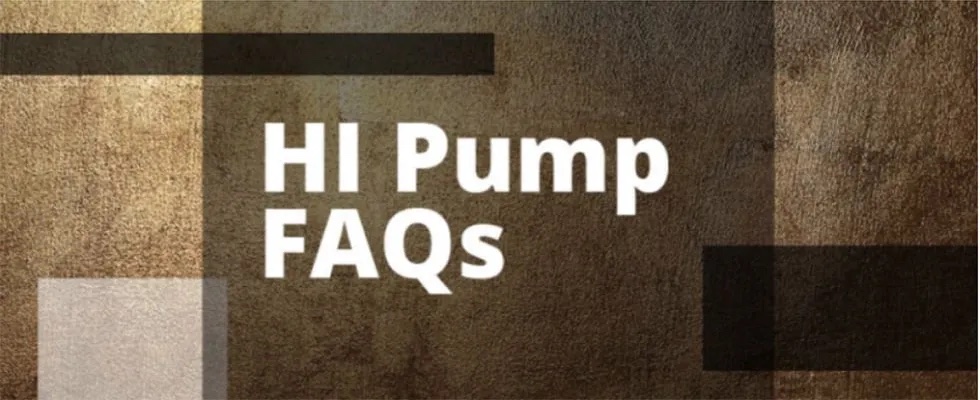
Submersible pumps are subject to many of the same tests as nonsubmersible pumps such as hydraulic performance, hydrostatic pressure and net positive suction head required (NPSHr). These, and some other standard acceptance tests, are outlined in ANSI/HI 14.6 Rotodynamic Pumps for Hydraulic Performance Acceptance Tests. There are mechanical and electrical integrity tests that are unique to submersible motors which are integral to the submersible pump. These tests are outlined in ANSI/HI 11.6 Rotodynamic Submersible Pumps for Mechanical and Electrical Acceptance Tests.
Two common types of mechanical integrity tests exist. They are the housing pressure test and the housing vacuum test. These tests ensure there are no holes, cracks or openings in the pump housing. To introduce the air pressure to the housing, a “T” assembly can be attached to the housing, as seen in Image 1. After the specified pressure is reached, the housing is isolated, and acceptance is judged based on the pressure decay.
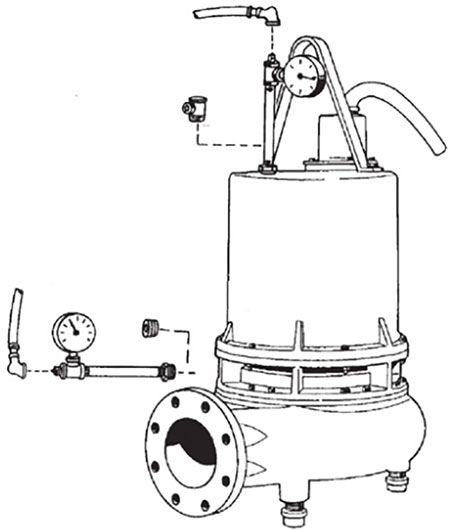
The housing vacuum test is connected to the pump housing similarly, except instead of adding pressurized air, it is connected to a vacuum line. Instead of disconnecting the vacuum pump and monitoring the pressure over a period of time, a differential pressure transmitter is required as well as a reference vessel, as shown in Image 2. Acceptance is based on the leakage rate.
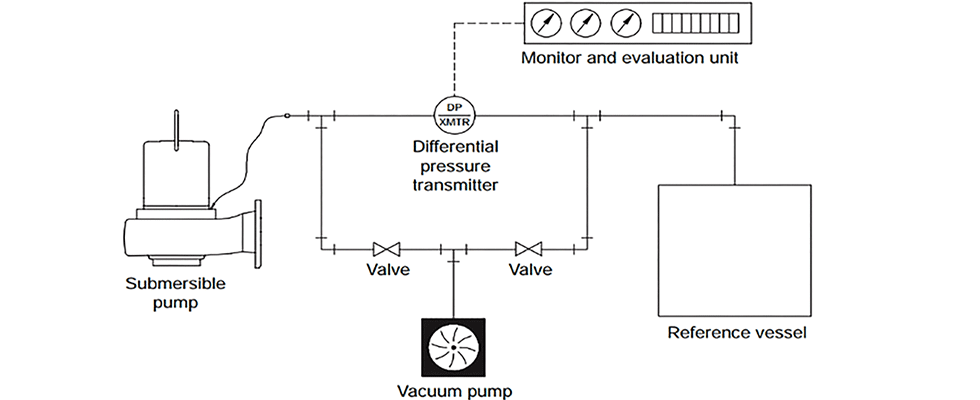
For more information about rotodynamic submersible pump tests, refer to HI standard, Rotodynamic Submersible Pumps for Mechanical and Electrical Acceptance Tests (ANSI/HI 11.6-2022) at www.pumps.org.