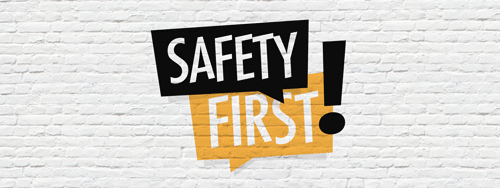
Safely pumping hazardous materials is a critical aspect of various industries, where the slightest oversight can lead to catastrophic outcomes like fires, explosions and environmental harm. Effective risk management and adherence to stringent safety standards are essential to mitigate these risks and ensure the protection of workers and assets. The FAQ below provides concise yet comprehensive answers to common queries regarding submersible pumps used in hazardous environments.
What are some examples of hazardous environments in industry?
Hazardous environments in industry are those where the presence of flammable gases, vapors, liquids or combustible dusts creates a risk of explosion or fire. These environments are commonly found in:
- Liquor distilleries: In distilleries, the production process involves handling ethanol, which is highly flammable. The vapors produced during fermentation and distillation can create explosive atmospheres if not properly managed.
- Natural gas facilities: These facilities handle large quantities of natural gas, which is highly combustible. Any leaks or releases of gas can mix with air and form explosive mixtures.
- Refining applications: This includes petroleum refineries, chemical plants and other facilities where volatile hydrocarbons and chemicals are processed. The presence of flammable substances in various stages of refining creates numerous hazardous zones.
How can I tell if my environment is considered a hazardous environment?
Determining if an environment is considered hazardous involves several key steps:
- Identify the presence of hazardous substances: Look for the presence of flammable gases, vapors, liquids or combustible dusts. Common examples include natural gas, ethanol, gasoline, solvents and certain dusts from grains, metals and chemicals.
- Consult safety data sheets (SDS): Review the safety data sheets for the materials handled in the facility. The SDS provides detailed information on the flammability, explosiveness and handling precautions for each substance.
- Conduct a hazardous area classification: Perform a hazardous area classification to determine the extent and type of hazardous zones. This classification divides the area into zones based on the likelihood and frequency of the presence of explosive atmospheres.
- Evaluate existing safety measures: Assess the current safety measures in place, such as ventilation, gas detection systems and explosion-proof equipment. The adequacy of these measures can help determine the level of hazard in the environment.
- Engage safety professionals: Involve safety professionals or consultants who specialize in hazardous environments. They can conduct thorough risk assessments and provide recommendations based on industry best practices.
What are the key considerations when working with hazardous materials in these environments?
Several key considerations must be addressed to ensure safety and compliance:
- Classification of hazardous zones: Properly classify areas based on the type and frequency of the presence of hazardous substances. This helps in determining the appropriate equipment and safety measures needed.
- Explosion-proof equipment: Use explosion-proof equipment that is certified for use in hazardous environments. This equipment is designed to prevent ignition sources from causing an explosion.
- Ventilation and gas detection: Implement adequate ventilation systems to disperse flammable vapors and gases. Use gas detection systems to monitor and alert personnel to dangerous concentrations of hazardous substances.
- Maintenance and inspection: Regularly inspect and maintain equipment to ensure it remains in good working condition. This includes checking seals, connections and the integrity of explosion-proof enclosures.
- Training and safety procedures: Ensure all personnel are trained in the proper handling of hazardous materials and the operation of explosion-proof equipment. Establish and enforce strict safety protocols to minimize risk.
- Regulatory compliance: Adhere to local and international regulations governing hazardous environments. This includes complying with standards such as Factory Mutual (FM), Atmospheres Explosibles (ATEX), International Electrotechnical Commission System for Certification to Standards Relating to Equipment for Use in Explosive Atmospheres (IECEx) and Canadian Standards Association (CSA) for equipment certification and operational practices.
What is the FM classification system and how does it apply to hazardous environments?
The FM classification system is a set of standards developed by FM Global, a property insurance and loss prevention company. These standards are used to ensure the safety and reliability of equipment used in hazardous environments. The FM classification system applies to hazardous environments by:
- Classifying hazardous locations:
• Class I: Areas where flammable gases or vapors may be present
• Class II: Areas where combustible dust may be present
• Class III: Areas where ignitable fibers are present - Division of zones:
• Division 1: Locations where hazardous substances are present during normal operations
• Division 2: Locations where hazardous substances are present only under abnormal conditions - Equipment certification: Equipment, including explosion-proof submersible pumps, must meet FM standards for use in specific hazardous locations, ensuring they do not act as ignition sources.
What do the different classes of hazardous environments mean?
The classification of hazardous environments is based on the nature and frequency of the presence of flammable substances:
- Class I (gases and vapors):
• Zone 0 (Division 1): Explosive gases or vapors are present continuously or for long periods.
• Zone 1 (Division 1): Explosive gases or vapors are likely to occur.
• Zone 2 (Division 2): Explosive gases or vapors are not likely to occur in normal operations, and if they do, it will be for a short period. - Class II (dusts):
• Zone 20: Explosive dust clouds are present continuously or for long periods.
• Zone 21: Explosive dust clouds are likely to occur in normal operation.
• Zone 22: Explosive dust clouds are not likely to occur in normal operation, and if they do, it will be for a short period. - Class III (fibers):
• These are typically found in areas like textile mills, where ignitable fibers may be present but not suspended in the air in large quantities.
What is the ATEX classification system and how does it differ from FM?
The ATEX classification system is used in Europe and is governed by two European Union directives for controlling explosive atmospheres:
- ATEX directives:
• ATEX 95 (Directive 94/9/EC): Pertains to the equipment and protective systems intended for use in potentially explosive atmospheres
• ATEX 137 (Directive 99/92/EC): Pertains to the minimum requirements for improving the safety and health protection of workers potentially at risk from explosive atmospheres - Zone classifications:
• Like FM, but with slight differences in nomenclature and criteria.
For example:
o Zone 0: Continuous presence of explosive gas
o Zone 1: Likely presence of explosive gas
o Zone 2: Unlikely presence of explosive gas - Equipment groups and categories:
• Group I: Equipment for mining
• Group II: Equipment for other industries
• Categories 1, 2 and 3: Define the level of protection needed, with Category 1 providing the highest level of protection for use in Zone 0.
What are IECEx and CSA explosion-proof standards, and how do they differ from FM and ATEX?
IECEx and CSA are additional systems that provide standards for ensuring the safety of equipment used in explosive atmospheres. Here’s how they differ from FM and ATEX:
- IECEx:
• Global standard: IECEx provides a global certification framework based on International Electrotechnical Commission (IEC) standards, facilitating international trade by ensuring that equipment used in hazardous environments worldwide meets the same safety requirements.
• Zone classification: Like ATEX, IECEx uses zone classifications (Zone 0, Zone 1, Zone 2 for gases and vapors and Zone 20, Zone 21, Zone 22 for dusts). - CSA:
• Canadian standard: CSA provides standards specifically for equipment used in explosive atmospheres in Canada, ensuring compliance with Canadian safety regulations.
• Classification system: CSA’s classification system is like FM, using classes and divisions to define hazardous locations—for example, Class I, Division 1 and 2 for gases and vapors, and Class II, Division 1 and 2 for dusts.
All systems are valid, and none is inherently better than the others. The choice of standard depends on the region of operation: FM and CSA are more region-specific (U.S. and Canada, respectively), while ATEX is European and IECEx is global.
What are flame paths and why are they significant in hazardous environments?
Flame paths are designed pathways within explosion-proof equipment that safely channel and contain any potential ignition sources, such as sparks or arcs, preventing them from igniting flammable gases or vapors present in the environment. These flame paths serve several critical purposes:
- Containment: By providing a controlled path for any potential ignition sources, flame paths prevent sparks or arcs from reaching the surrounding explosive atmosphere, minimizing the risk of ignition and subsequent explosion.
- Compliance: Flame paths are a fundamental requirement for certification under all explosion-proof standards. Ensuring the integrity and effectiveness of flame paths is essential for maintaining compliance with these stringent safety regulations.
- Testing and certification: Explosion-proof motors undergo rigorous testing and certification processes to verify the flame paths’ effectiveness in preventing ignition and containing potential explosions. These tests assess factors such as enclosure integrity, spark containment and resistance to external forces.
Why is selecting an explosion-proof pump not as simple as it seems?
Selecting an explosion-proof pump involves more than just choosing a pump that can handle hazardous materials. Several factors make the selection process more complex:
- Choosing the correct classification: Understanding the specific classification of the hazardous environment where the pump will operate is crucial.
- Limited availability: There are limited suppliers who offer explosion-proof pumps due to the specialized design and certification requirements. This can restrict options and necessitate careful consideration of available products and manufacturers.
- Application requirements: Consideration must be given to the specific requirements of the application, including flow rate, head pressure, fluid compatibility and temperature range. These factors determine the appropriate pump type, size and materials of construction needed to meet the demands of the application.
- Cost considerations: Explosion-proof pumps are typically more expensive than conventional pumps.
Why are explosion-proof pumps typically more expensive than conventional pumps?
Explosion-proof pumps are engineered to operate safely in hazardous environments where the risk of explosion is present. Several factors contribute to their higher cost:
- Specialized design: Explosion-proof pumps are built with robust materials and construction methods to withstand the rigors of hazardous environments, including corrosion-resistant materials and heavy-duty enclosures.
- Certifications and testing: These pumps undergo rigorous testing and certification processes to ensure compliance with industry standards such as FM, ATEX, IECEx and CSA. This involves additional manufacturing steps and quality control measures, adding to the overall cost.
- Safety features: Explosion-proof pumps are equipped with safety features such as flame paths, thermal protection and sealed electrical components to prevent ignition sources and mitigate the risk of explosion.
- Elastomer compatibility: Specialized elastomers add to the cost but are essential for ensuring durability and reliability in hazardous environments.
What factors should be considered when selecting pumps for different hazardous applications?
Several factors should be considered to ensure safe and efficient operation:
- Type of application: Determine the specific type of application, such as dewatering, solids handling or slurry pumping, as this influences the selection of pump design and features tailored to the application’s requirements.
- Material construction: Choose pump materials that are resistant to corrosion, abrasion and chemical attack. Materials such as stainless steel, bronze and specialized alloys are commonly used for their durability and compatibility with hazardous materials.
- Elastomer compatibility: This is critical in pump selection for hazardous materials due to the potential for chemical exposure and degradation. Choosing the right elastomers ensures the longevity and reliability of the pump by preventing material deterioration, leaks and contamination.
- Flow rate and pressure requirements: Determine the required flow rate and pressure head to meet the demands of the application. Select a pump that can deliver the necessary performance while operating within its designated operating range.
- Safety features: Ensure the pump is equipped with appropriate safety features, such as explosion-proof enclosures, thermal protection and leak detection systems, to mitigate the risk of accidents and ensure compliance with safety regulations.
- Maintenance and serviceability: Consider the ease of maintenance and availability of spare parts when selecting a pump. Opt for pumps that are designed for easy inspection, maintenance and repair to minimize downtime and ensure reliable operation in hazardous environments. Also consider most repairs must be conducted by an authorized service shop, which will add time and cost to a repair.
What considerations should be made for control systems in hazardous environments?
Control systems play a crucial role in ensuring the safe and efficient operation of pumps in hazardous environments. Key considerations include:
- Explosion-proof design: Select control systems that are specifically designed and certified for use in hazardous environments. Ensure that all components, including switches, relays and enclosures, meet the necessary explosion-proof standards to prevent the risk of ignition and explosion.
- Environmental monitoring: Implement monitoring systems to continuously monitor environmental conditions, including gas concentration levels, temperature and pressure. Early detection of potential hazards allows for prompt response and intervention to prevent accidents and ensure personnel safety.
- Remote operation and monitoring: Utilize remote control and monitoring capabilities to allow for safe operation and supervision of pumps in hazardous environments from a distance.
- Emergency shutdown systems: Install emergency shutdown systems to automatically stop pump operation in the event of a safety hazard or abnormal condition. These systems provide an additional layer of protection against accidents and help minimize the risk of equipment damage and environmental contamination.