Successful field engineering requires many of the same tools and techniques as traditional development engineering. For the purposes of this article, “field engineering” can be thought of as the application of engineering to solve a problem with a machine or system after it has been designed and installed. A logical, detailed analysis approach must be used in conjunction with the appropriate engineering analysis hardware and software. Often, field engineering efforts degenerate into a trial-and-error approach, which does not achieve an optimal, cost-effective solution. Pressure from management to get a system online and running or to ensure adherence to a project schedule often force temporary fixes or poorly developed solutions, which ultimately detracts from the long-term reliability and increases life-cycle costs of the equipment. If a field engineering effort is approached with the same methodology as a new project or design problem, the outcome will be a superior solution. This is true regardless of whether the problem lies within hydraulic system or is a mechanical equipment issue. To illustrate this concept, this article will start with a basic “engineering analysis” procedure:
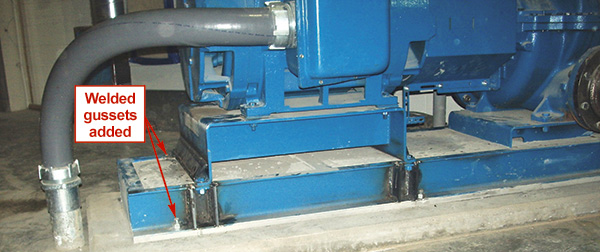
- Clear problem statement
- Information gathering
- Defining assumptions and limitations
- Selecting appropriate governing equations
- Calculations (or simulation) and solution generation
- Alternative selection and implementation
- Vague problem statement
- Trial solution
- Feedback (Did it work?)
- Another trial solution
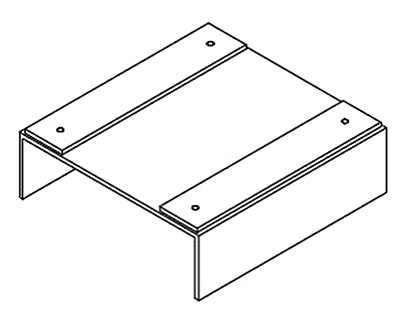
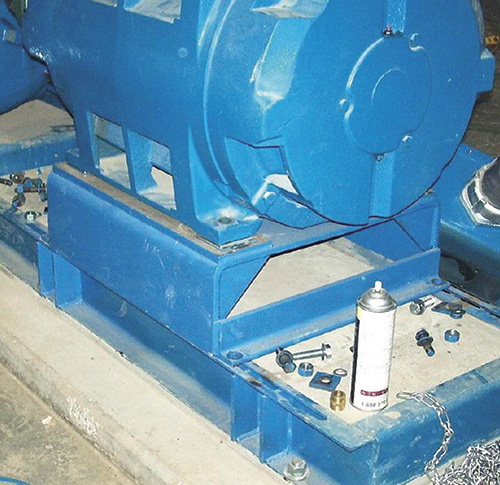
A Case Study
The following case history is offered to illustrate the concept. A new manufacturing plant was being constructed near Kansas City in early 2012 and the plant utilities building was close to completion. However, a problem was noted with the newly-installed chilled water circulator pumps. The pumps were between bearings, double suction centrifugal, 1,800 RPM, size 8x10-17 operating on VFDs. The reported problem was elevated turning speed vibration at higher operating speeds. Amplitudes of greater than 0.40 IPS-RMS were reported. This was unacceptable and the contractor was facing penalties on the project unless the issue was corrected in a short time frame. The first field engineering effort proved unsuccessful in reducing the vibration and took approximately two weeks to work through at a cost of several thousand dollars. The problem was investigated, but not enough to facilitate the engineering solution. In this case, the problem was identified as a resonant frequency using standard spectral vibration analysis, but no further investigation was performed to clearly define exactly which component(s) were involved, the mode shapes involved or the operating deflection shape of the equipment. The result was a vague definition of the problem. The next steps were contacting the original equipment manufacturer (OEM) for support. This was a positive step, but without complete information and a clear definition of the problem, the suggested field fix from the OEM was ineffective. It involved welding gussets to several areas of the base (see Figure 1).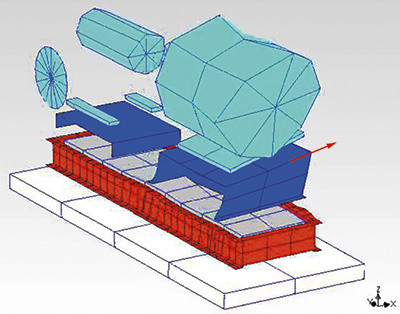
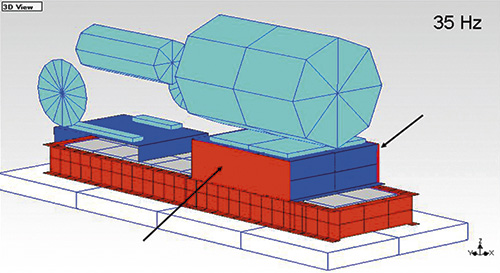
- The operating deflection shape at 1,498 RPM approximated the first mode shape indicating possible resonance.
- The first mode was a lateral rocking of motor base at 25 hertz
- The second mode was a longitudinal twisting of the motor saddle at 70 hertz
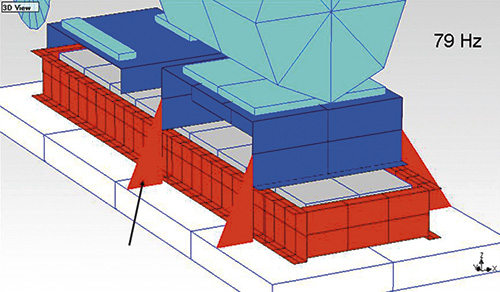
- The next step in the process was to define the assumptions and limitations. For this case, the list of assumptions and limitations looked similar to those listed below.
- Shifting the first mode to a value greater than 15 percent higher than the maximum operating speed will eliminate the resonant condition.
- The solution must be able to be fabricated and installed in less than one day per pump.
- The solution must cost less than $1,500 per pump.
- No piping or piping support modifications are allowed.
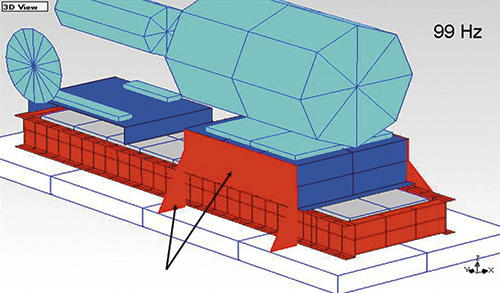
Specific Software Simulation Tool
Steps four and five involved the use of a specific software simulation tool. The governing equations for the engineering analysis are part of the software package and involve the equations of motion and the experimentally derived modal parameters (stiffness, mass, damping, etc). The use of a software simulation tool allows the engineering analyst to simulate the impact of myriad structural modifications on the dynamics of the system. The goal is to determine what type of modifications would increase the first natural frequency of the motor/base assembly to 35 hertz or greater with a minimum of additional cost and effort. The accuracy of the predicted effect from the structural dynamics modifications (SDM) simulations was checked by comparing the predicted effect of the previous modifications with the test data obtained on the modified pump. Agreement was determined between them, resulting in a high degree of confidence that the SDM predictions were accurate. The results of several example SDM simulations are shown in Figure 5. (The predicted natural frequency of the mode of interest is shown in the upper right hand corner.)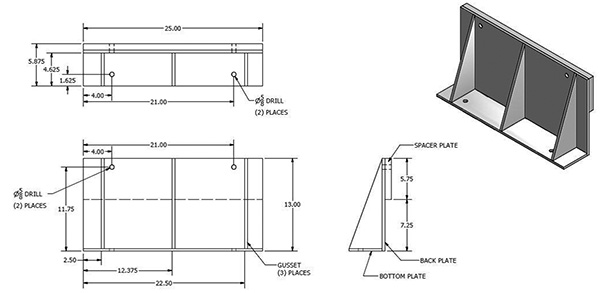