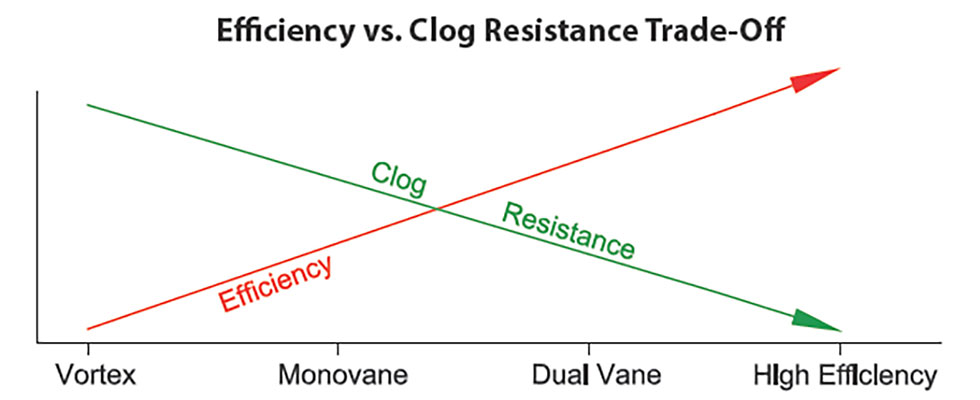
Mechanical efficiency has been a topic of conversation since energy conservation became a priority. This began in the 1970s and ’80s with the establishment of the Department of Energy (DOE), which was in reaction to the Arab Oil Embargo that caused energy costs to skyrocket. Energy conservation not only reduces overall energy costs but also benefits the environment through emissions and the changing climate. Pumps, motors and their corresponding systems are no exception to the energy conservation trend. Historically, pump efficiency was only a concern and focus in clean water markets but is increasingly important in the wastewater market and not just with pumps. Pumps and motors do not operate alone—they use drives, valves, controls and other pieces of ancillary equipment. These items all have efficiencies to account for.
Efficiency in Clean Water
Efficiency in clean water pumps has long been a concern but has most recently culminated in new requirements published by the DOE. The development of these requirements began in 2011 and were officially published in 2016 as an amendment to the Energy Policy and Conservation Act of 1975. This amendment, named “Energy Conservation Program for Certain Industrial Equipment,” was the first standard for clean water pumps, including end suction models, submersible turbines and inline pumps, and it established minimum efficiency requirements. The minimum efficiency is determined by the Pump Energy Index (PEI), which is based off various pump characteristics to assign a single number that can be used to compare pumps from different manufacturers and technologies. These requirements for clean water pumps went into effect January 2020.
Shifted Public Focus on Efficiency in Wastewater
While the DOE regulated clean water efficiency first, wastewater treatment systems often have more processes and equipment, making it a bigger opportunity for energy cost reduction. The treatment plant processes are energy-intensive, with the U.S. Environmental Protection Agency (EPA) reporting that wastewater treatment plants can be responsible for up to one-third of a municipality’s energy costs. It recommends a systemwide approach to improve energy efficiency.
3 Types of Efficiency in Wastewater Pumps
A typical submersible wastewater pump has three types of efficiencies to consider: pump end, motor and wire-to-water. Wire-to-water, also called combined or total efficiency, considers both the pump end efficiency and the motor efficiency to create one number for the entire pump and motor system. This also takes into account losses attributed to the bearings, mechanical seals and power cables. Wire-to-water can also be expanded to include controls and variable frequency drives (VFDs), which reinforces the need for overall system efficiency. Note that because both the pump and motor have efficiency curves, the wire-to-water efficiency should also be described as a curve plotted against flow. Because most pump manufacturers only publish pump end efficiency on their curves, the best way to obtain wire-to-water efficiency for the pump and motor combination is typically through a pump performance test. However, if an estimation is needed, a quick calculation can be done to approximate the wire-to-water efficiency of a pump and motor combination at a specific flow. Simply take the product of the two efficiencies and remove a few points for the mechanical losses.
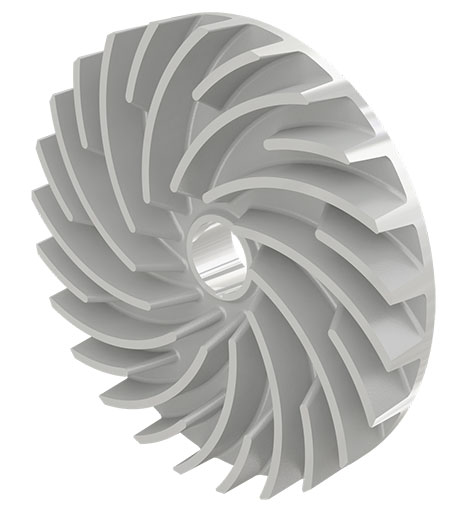
Impeller Types, Solids Handling & Pump End Efficiency
Many factors contribute to pump end efficiency, including casting and machining quality, volute-to-impeller clearances and mechanical losses. One specific factor to look into further is the impeller type.
There are many impeller designs out there—enclosed, semi-open, open, vortex, screw type, mixed flow—the list goes on. Each of these designs has a specific purpose. Sometimes that purpose comes with an efficiency impact. One that is specifically seen in wastewater is the inverse relationship between solids handling and efficiency.
Typically, impellers that are the best at handling solids are the least efficient. Vortex impellers do well in solids heavy applications, but they have a maximum efficiency in the 40% to 50% range. On the opposite side of the spectrum, enclosed impellers have high efficiencies in the 80% range, but have little to no solids handling capabilities. Grinder pumps typically follow this trend, with maximum efficiencies around 20% to 30%.
One outlier in this relationship is chopper/cutter pumps. Depending on the design of the cutting mechanism, these pumps can use enclosed or semi-open impellers, allowing for higher efficiencies while maintaining good nonclogging capabilities. Cutter and chopper impellers with sharpened leading edges also mean that the impellers have fewer vanes and higher efficiencies than a typical vortex-style impeller.
With the increased use of computational fluid dynamics in impeller designs, efficiencies are increasing on all types of impellers, including those that handle solids well, so the solids handling-efficiency relationship may change as this technology advances.
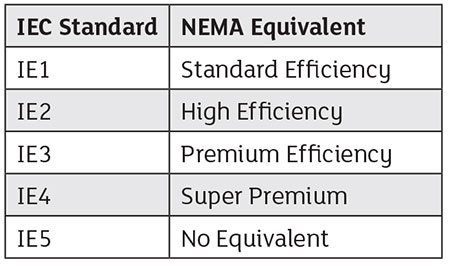
Pump Motor Efficiency: NEMA vs. IE
The other half of wire-to-water efficiency is the motor efficiency. In submersible pumps, this is typically referring to the International Efficiency (IE) motor rating, which is designated by the International Electrotechnical Commission (IEC). In nonsubmersible pumps, the reference is to the National Electrical Manufacturer’s Association (NEMA) rating. While NEMA sets the standards for motors used in North America, the IEC sets the standards for the rest of the world (Image 3).
The IEC efficiency ratings are represented by curves, plotting efficiency against horsepower. The market standard for premium efficient submersible motors is IE3, which ranges from just more than 60% at lower horsepower ratings to
96% at the highest. The combination of an IE3 efficient motor with a high efficiency pump end creates a high wire-to-water efficiency and can lead to energy savings over time. The equivalent NEMA rating, Premium Efficient, is the market standard in nonsubmersible applications, meaning that the overall wire-to-water efficiencies are high in almost all pumping applications in wastewater systems.
Changing to Systemwide Efficiency
As noted previously, pumps and motors do not operate alone. While each device in a wastewater treatment system has an inherent efficiency, the benefits come from the ever-changing technologies and their ability to operate without waste. Systems like supervisory control and data acquisition (SCADA) collect data on pump cycles and flows, allowing operators to correctly size pumps for their applications. VFDs control the pump speed so that it runs exactly where it needs to, minimizing wasted energy. VFDs can also vary the pump’s performance to handle peak and off-peak loads, furthering the reduction in energy requirements.
Updates to the pumps themselves are also important; replacing outdated pump technologies with newer efficiencies is increasing through equipment upgrades. Treatment facilities are updating their motors, mixers, aerators and even lighting systems and windows to save energy costs.
Due to the focus on system efficiency, the wastewater industry is well poised to handle the constant fluctuations in energy costs. This trend is not likely to disappear anytime soon. Efficiencies will continue increasing in pumps, motors, drives and all ancillary pieces of equipment, driving toward the highest possible values they can achieve.