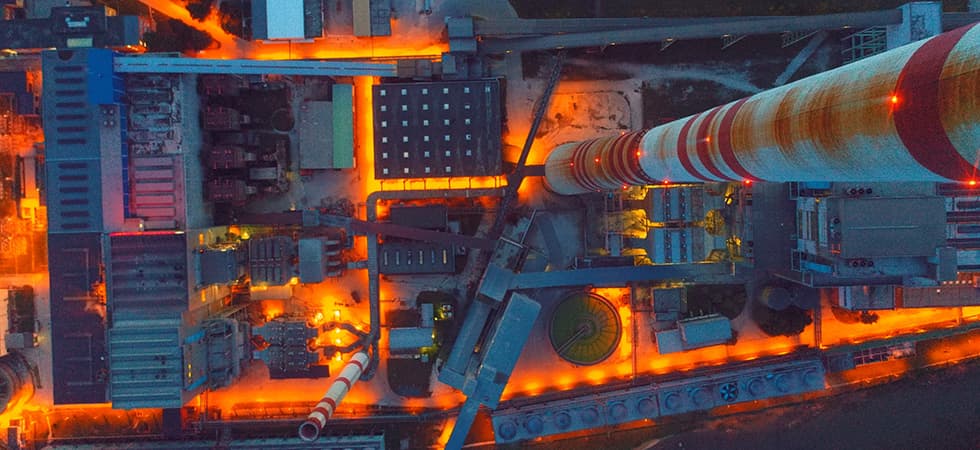
Many power generation plants rely on integrally geared centrifugal compressors designed to boost the flow of natural gas to turbines. The day-to-day reliability of these compressors is critical for these plants to deliver uninterrupted power to ratepayers and stakeholders.
Repeated compressor failures, on the other hand, can quickly drain millions of dollars from the bottom line in repair and maintenance costs—not to mention the potential power supply problem passed on to the public. Oftentimes, the trouble can be linked to faulty compressor dry gas seals (DGS) that are critical for containing compressor pressure as well as preventing leaks.
Correctly troubleshooting the seal problem calls for a holistic and comprehensive root cause analysis (RCA) of the problem to arrive at the most effective way to solve the issue. An RCA is a time-tested method of solving problems employed by many industries.
A proper DGS RCA goes well beyond seal performance, or lack of it. It also includes the mechanical and operational functions of the gas compressor and the related system to isolate the underlying cause of the seal failure.
A Holistic RCA Approach
While power production plants vary in design, technology and output, a standard RCA approach may be used in most cases. Again, an effective RCA takes into account the big picture, understanding that every change made affects the entire compressor. The analysis goes well beyond the seal to establish the underlying differences and unique reasons for a DGS failure.
An RCA encompasses the mechanical and operational functions of the gas compressor, including related systems design and settings. These include:
- damage analysis of failed dry gas seals, internal compressor parts and labyrinth seals
- sequencing of events encompassing speed, pressures, process temperature, flows, shaft radial/axial vibrations, shaft axial position, gas seal leakage, gas composition and system settings
- operating procedures
- compressor operating trends and history
- startup and shutdown procedures
- gas compositions
- system designs and transmitters settings
- DGS design and related inspection reports
RCA Case in Point
An example of an effective RCA can be found at a power generation plant located on the East Coast that provides power to a major city where operational reliability of the plant is vital to its customers. This plant’s system is typical of those found in other natural gas-fired, combined-cycle power plants.
For years, the DGS installed in the plant’s gas booster compressors operated without interruption or needing repair. However, in 2017, plant engineers at this electric generation site found that the gas seals were failing multiple times on three multistage, high-speed bull gear compressors.
The >800 megawatt (MW), combined-cycle power plant continuously ran two 30,000 to 45,000 rpm compressor trains, each equipped with a low-pressure and high-pressure DGS. The generating station depended on the third compressor train, also equipped with two DGS, to provide backup gas in case one or both primary trains went down.
The frequent DGS failures threatened the potential for all three compressor trains to simultaneously be out of service. That was unacceptable to plant management.
The power plant’s compressor included a thrust bearing and bidirectional DGS as part of the original design. The original DGS supplier suggested the problem was the quality of the incoming gas and did not consider other mechanical or operational causes. After repeated attempts to remedy the problem, the plant went another route.
At the request of the power company’s management, an RCA was conducted, finding that some of the failures were catastrophic. The RCA concluded:
- There was no sign of heavy compressor surge.
- There was signs of liquid condensate and clear oil in spite of a well-designed DGS buffer gas conditioning unit.
- There was erratic seal leakage flow during operation.
- There were signs of face contact at both the primary and secondary face.
- The primary face contact was mostly at the entire face.
- The secondary contact was mostly at the face inside diameter.
Ultimately, the RCA determined that DGS problems were linked to improper settings on the DGS control system related to change in gas composition because of new process gas sourcing, reinforcing that every change made affects the entire compressor/plant operational reliability.
A Multifaceted Solution
The solution included replacing the backup compressors’ low- and high-pressure original DGS with more robust noncontacting gas seals that could stand up to the demanding environment of the high-speed compressor.
The analysis showed that inadequate primary vent back pressure made the secondary sealing unstable and
required resetting the control system’s transmitters to maintain an optimal 15 pounds per square inch (psi) primary vent back pressure.
The team also increased the DGS buffer gas temperature to avoid process condensate forming at the seal faces in extreme weather conditions. Attention was given to seal balancing due to the high speed of the operation. Back pressure was introduced at the primary vent to improve secondary seal performance, provide dampening across the seal face, and provide a way to monitor seal performance according to the American Petroleum Institute (API) 692 standard. Finally, the flow of dry and clean buffer gas was also increased to the DGS to optimize the reliability of the DGS.
Since 2017, the compressors have performed without interruption or repair since the RCA and subsequent improvements. Additionally, most of the of DGS at the plant have been replaced with new DGS to ensure reliability and lower cost of ownership.