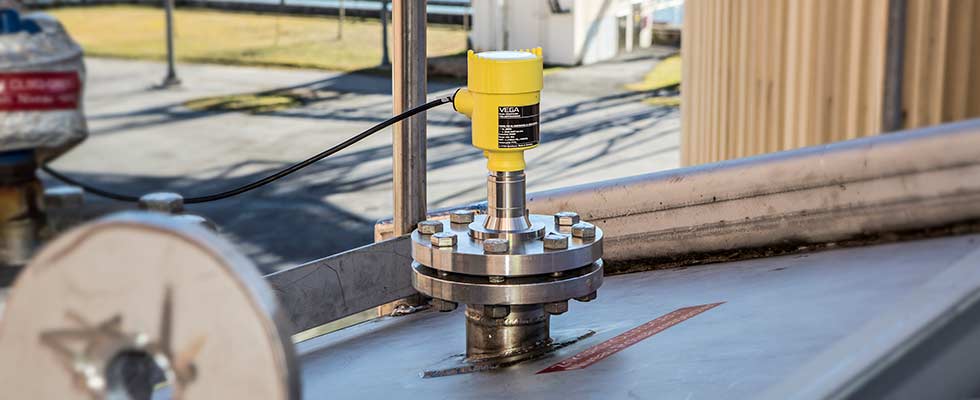
Radar sensors are used for measuring liquids and solids in industries ranging from chemical plants and refineries to ready-mix concrete facilities and wastewater treatment plants.
There is a reason radar technology is widely used: It can provide accurate, reliable level measurements without maintenance or recalibration, and the sensors are easy to set up. Once a radar sensor is installed properly, it can provide vital level control for years and even decades.
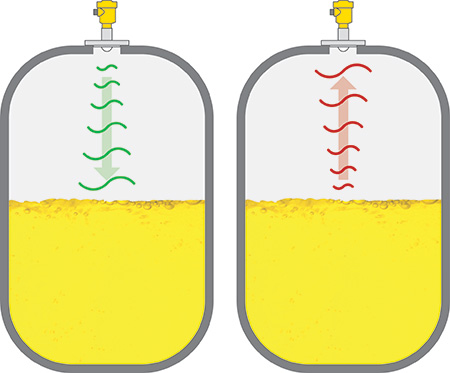
How Radar Level Measurements Work
Radar level technology uses time of flight to make a measurement. Radar sensors are installed at the top of the vessel and emit radio microwaves from the antenna system to the measured product surface where that signal is reflected back to the antenna.
The amount of time between emission and reception is proportional to the distance to the product surface—the longer the time of flight, the greater the distance. This distance is inversely proportional to the level in the tank, bin, silo or container, so a greater distance equates to a lower level—and vice versa.
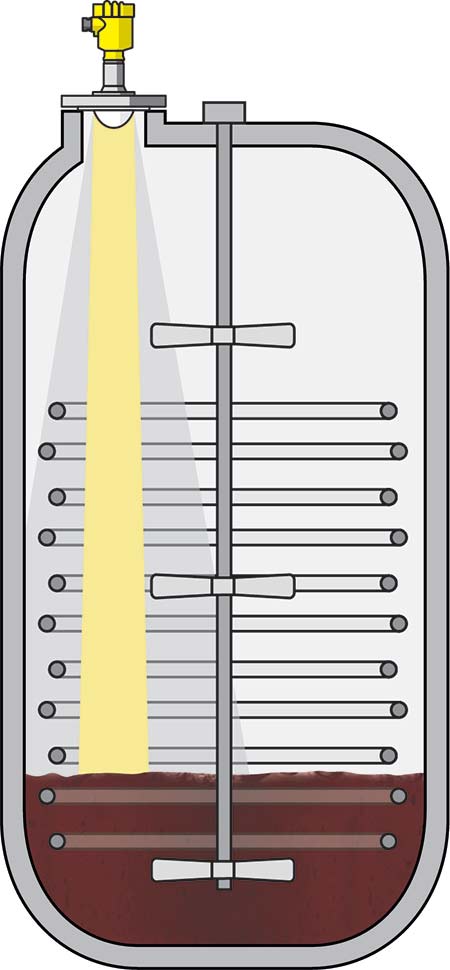
A radar sensor’s integrated electronics convert the measured value into an analog or digital signal for transmission. The signal can be used for an external display or a process control system. Additional components for hazardous areas, overvoltage protection or wireless communication enable a wide range of applications in all industrial sectors.
Radar manufacturers continue to make improvements in sensor technology and software, which has boosted signal strength and improved measurement accuracy and reliability. Many of today’s radar sensors use higher transmission frequency, take advantage of an improved dynamic range, and use smarter software, giving users better options and more versatility for reliable level measurement instrumentation.
The latest high-frequency radar level sensors use a transmission frequency of 80 gigahertz (GHz), a leap forward from the previous generation of radars using 26 GHz. This is important because a radar sensor’s beam angle is dependent on two factors: antenna size and transmission frequency.
When it comes to antenna size, a radar sensor’s microwave beam angle is inversely related. A smaller antenna will have a wider, less focused beam. Conversely, a larger antenna will have a narrower, more focused beam.
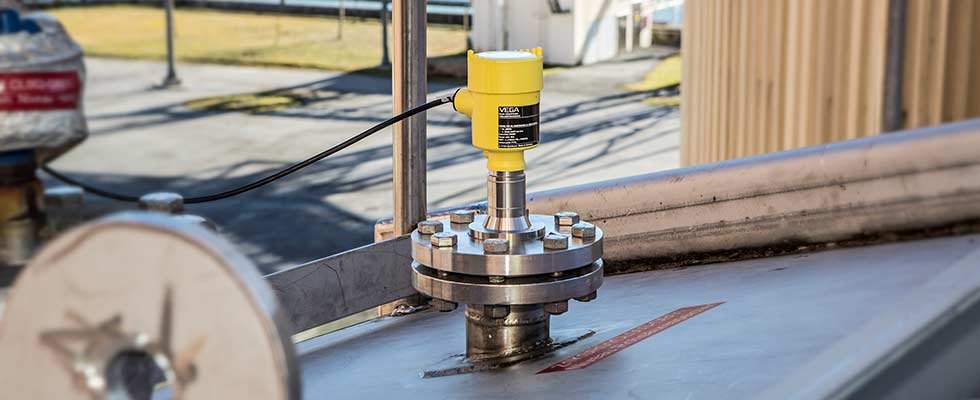
Process fittings cannot always be changed; so, a radar level sensor’s beam angle is often at the mercy of where it is installed. While this may work in some applications, it can be a hindrance in small vessels or tanks with internal components like agitators or heating coils. These are the situations where 80 GHz radar level sensors outperform their 26 GHz counterparts.
Radar sensors with a higher transmission frequency have a narrower beam angle, which makes installations easier and measurements more reliable. A more focused signal can make measurements around internal obstructions, and with more of the microwave energy reaching the measured product, the radar sensor receives a stronger return signal. When paired with improved sensitivity, users can expect a more reliable, more accurate measurement.
Receiving a Reliable Signal
The strength of the radar’s return signal relies on a number of factors. The product surface, distance between the product surface and the sensor, and product reflectivity all play a part. An agitated, turbulent product surface is more likely to reflect the radar signal in other directions away from the radar antenna. Partial signal loss can occur over longer distances, and this must be accounted for in tall tanks and silos. And finally, not all products reflect radio microwaves equally.
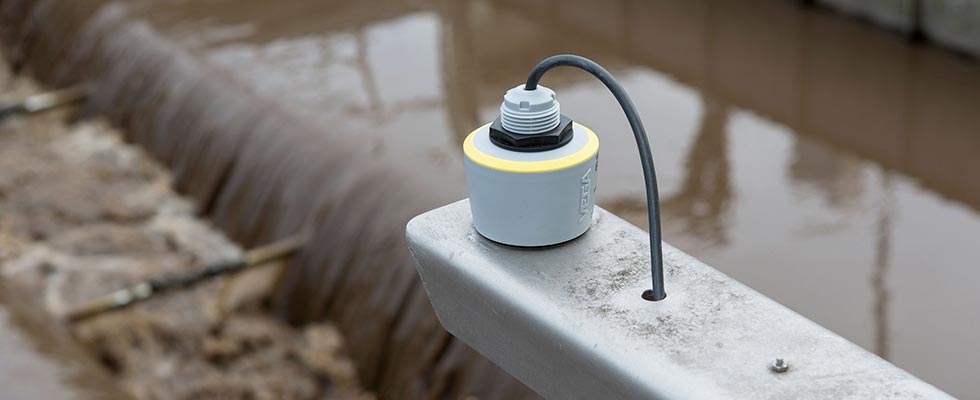
A product’s chemical composition is typically the biggest predictor of signal strength. Conductive products reflect almost all microwave energy while nonconductive products reflect just a portion of the same energy. This reflective property is referred to as a product’s dielectric constant. Highly reflective products like water have a high dielectric constant while poorly reflective products like oil have a low dielectric constant.
The range of signals a radar sensor can detect is called its dynamic range. Sensors with a large dynamic range are sensitive enough to register weak signals as well as strong ones. Radar sensitivity varies from manufacturer to manufacturer and even from sensor to sensor in a manufacturer’s instrument line. A user may think a highly sensitive radar would be more susceptible to “noise” created by unwanted microwave energy reflecting back to the antenna. This unwanted noise could originate from buildup or condensation on the antenna, from internal structures within the vessel, or from microwave energy bouncing off the side of the vessel itself. This noise can distort a level measurement, but it can be overcome with intelligent software capable of filtering out any interference.
FMCW vs. Pulse Radar Technology
When comparing different radar sensors, users may discover two different types of radar level sensors: frequency-modulated continuous-wave (FMCW) and pulse. These are two different methods of how the radars operate. Both principles of operation output the same level measurement using the time of flight principle, but the type of signal is slightly different.
FMCW radar sensors transmit a continuous linearly modulated signal. The receiver and sensor electronics monitor for this changing intensity of the return signal and determine a distance to output a level measurement. Pulse radars transmit singular pulses of a set intensity while the receiver and sensor electronics monitor for these individual signals to return.
In the early days of radar level measurements, these two technologies differed greatly in their applications and performance, and each option had its strengths and weaknesses. Since then, both methods have improved, their shortcomings have diminished, and the technologies have become more similar in power consumption, reliability and cost.
As a result, these features are not typically deciding factors when choosing a modern radar level sensor. Instead, other improvements and features like transmission frequency, dynamic range and manufacturer support do a better job of differentiating radar sensors from one another.
Common Applications for Through-Air Radar
Radar level transmitters are used for noncontact level measurement of liquids and bulk solids, even under high pressure and extreme temperatures. They can be used in simple or aggressive liquids, and they are suitable for applications with stringent hygiene requirements. Radar level sensors measure light and heavy bulk solids with unquestionable reliability—even in the presence of dust and noise—without being affected by buildup or condensation.
Advantages of Radar Level Sensors
Through-air radar level sensors’ most noticeable advantage is their noncontact measurement, and they have no moving parts. This means users do not have to worry about the level sensor getting damaged by corrosive or harsh products, and there is no ongoing maintenance.
Radar sensors are unaffected by fluctuating product properties or by changing process conditions like temperature, pressure or high-dust environments. This is because radar sensors use radio microwaves to make a measurement, and few process variables can disturb the flight of a radio wave, making this type of sensor a reliable option for level measurement.
Another benefit of using a through-air radar sensor is that initial setup and adjustment can be done while the vessel is in use. Installing a level device without stopping the process saves time and avoids the cost of a shutdown.
Limitations
Through-air radar is capable and offers many benefits to users, but that does not mean it is the solution for every level measurement application. For starters, users must have a connection at the top of the tank to install a radar level sensor. The connection does not have to be large, but it must be present.
In applications with rampant, heavy foam, radar is not always the right solution either. The radio microwaves can be absorbed right into the foam. However, not all foam is created equally, so it is always a best practice for users to discuss their level measurement application with their instrument provider before choosing a technology.
Process measurement instrumentation veterans may say radar has a reputation for being too expensive for some industries to make such a big investment, but that is not true anymore. As the technology has grown, improved and become more diversified, users can now find cost-effective radar sensors specifically designed for industries accustomed to lower-cost instrumentation.
When searching for a noncontact level measurement, radar technology should be at the top of everyone’s list. Radar sensors are more focused than ever before, making them a reliable option, even in vessels with obstructions or applications that require isolation valves.
Some instrumentation manufacturers are pairing the exceptional focus of 80 GHz technology with incredible sensitivity and intelligent software, so users can measure products with poor reflective properties and eliminate return signals from unwanted noise.
Additionally, current high-frequency radars have smaller antenna sizes, enabling radar to go places that were previously thought to be impossible. Retrofitting and mounting are now less expensive and simpler.
Users who have steered away from radar in the past should give it a second look, and users currently relying on an older radar may want to consider an upgrade to a high-frequency unit. Radar technology has come a long way since its inception, and today’s sensors are providing more accurate, reliable level measurements.