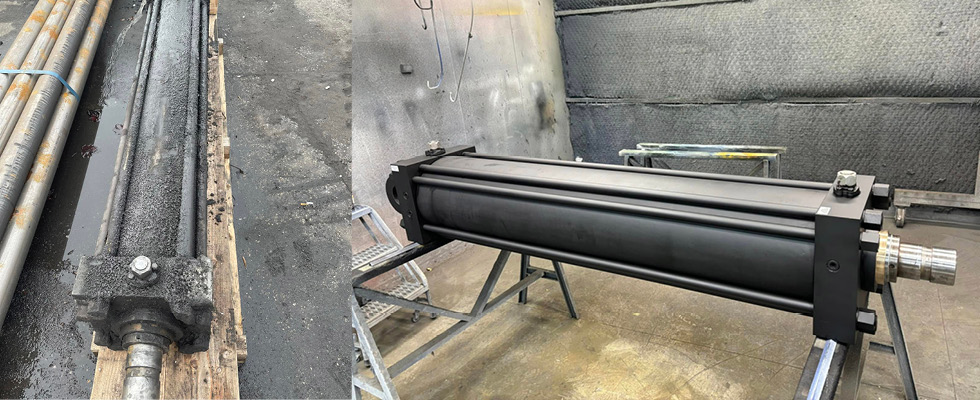
For maintenance and manufacturing professionals, one of the greatest challenges is navigating the unpredictable cost and downtime of equipment failure. This challenge is compounded by industrial machinery that may be in operation for decades, often without the advanced features of modern systems. However, aftermarket solutions for condition monitoring are providing a viable cost-effective path forward by improving equipment reliability and operational efficiency. These tools empower teams to anticipate failures, minimize disruptions and extend the life span of existing assets.
What Is Condition Monitoring?
Condition monitoring involves the use of sensors, data analysis and other technologies to track the health of equipment and identify signs of wear and tear before failure occurs. Aftermarket condition monitoring solutions allow older equipment to be retrofitted with these capabilities, making predictive maintenance a more accessible option for businesses seeking to optimize their operations.
By continuously monitoring key parameters—such as vibration, temperature, pressure or voltage—these systems give operators real-time insights into machinery conditions. Acting on these insights can mean the difference between seamless operations and costly downtime. This approach strikes an ideal balance between performance optimization and long-term cost management.
Types of Aftermarket Condition Monitoring
Aftermarket condition monitoring solutions come in multiple forms, each tailored to specific operational needs. Deciding what type of monitoring to implement depends on factors such as equipment configuration, performance demands and the nature of surrounding processes. Below are examples of commonly deployed monitoring technologies.
Vibration monitoring
Vibration monitoring is a highly effective diagnostic method for identifying mechanical issues in rotating equipment like pumps, motors and compressors. Sensors detect abnormal vibration patterns that often stem from issues such as bearing wear, shaft misalignment or rotor imbalance.
Temperature monitoring
Temperature monitoring is essential for preventing overheating issues. Aftermarket solutions enhance this process by seamlessly integrating temperature sensors into engines, bearings and other heat-sensitive components. These sensors continuously track temperature levels and detect abnormal readings that may signal underlying problems, such as lubrication deficiencies, excessive friction, electrical malfunctions or impending component failures.
Pressure monitoring
Pressure monitoring provides insights for systems that rely on hydraulic, pneumatic or fluid-based components. Excessive or insufficient pressure can signal leaks, blockages or pump malfunctions.
Voltage monitoring
Electrical systems remain a backbone in manufacturing environments. Voltage monitoring allows operators to observe the health of motors, drives and associated circuits. It captures data on voltage irregularities, identifying wiring issues, insulation weaknesses or power supply instabilities.
The Benefits of Aftermarket Condition Monitoring
Predictable service and repair
Unplanned downtime is a major challenge for manufacturers, leading to operational inefficiencies and financial losses. Aftermarket condition monitoring shifts the maintenance strategy from reactive to predictive, equipping teams with real-time alerts and critical insights into equipment health. Issues can be identified early, allowing scheduled maintenance programs to align with actual equipment needs.
This targeted approach helps to ensure repairs and servicing occur only when necessary, reducing the risks of over-maintenance while addressing potential failures before they happen.
Likewise, planning maintenance activities ahead of time reduces the frequent reliance on costly emergency parts procurement and expedited labor. Resources are utilized more effectively, with maintenance teams focusing their efforts on priority tasks and making optimal use of personnel, tools and spare parts. The result is a streamlined operation with reduced repair expenses and increased uptime.
Extended equipment life span
Machinery wear and degradation are inevitable over time, but integrating retrofitted condition monitoring technology can mitigate these effects. Retrofitting older equipment with advanced sensors and monitoring systems is a cost-effective way to modernize existing assets, enhancing their performance and reliability without the need for expensive replacements.
By equipping legacy machinery with real-time monitoring capabilities, teams gain the ability to track issues like misalignments, overheating and excessive vibration. Retrofitted machines also experience reduced strain on critical components. This leads to less wear and tear, smoother performance and longer intervals between repairs.
Improved safety
The industrial sector inherently involves risks, and equipment failures can have significant safety implications. Incidents like overheating motors, mechanical breakdowns or pressurized fluid leaks can lead to workplace hazards, property damage or even serious injury.
Condition monitoring plays an invaluable role in preventing such scenarios, as it enables early identification of potential safety concerns. For example, a temperature abnormality detected in a critical motor allows teams to prevent overheating that could otherwise lead to fire hazards or equipment seizure. Similarly, monitoring systems that identify leaks or fluctuations in pressurized systems help avoid dangerous mechanical failures. These advances protect personnel from harm and minimize the risk of property damage that could disrupt operations.
Aftermarket Service & Repair Enhanced by Condition Monitoring
While condition monitoring reduces the likelihood of equipment failures, no solution can entirely eliminate the potential for unplanned breakdowns. When such events occur, the combination of condition monitoring with aftermarket service and repair provides a powerful advantage.
Real-time data from condition monitoring systems provides repair teams with detailed diagnostics. Instead of relying on symptoms or guesswork, technicians can access precise insights into the root cause of failures.
The partnership between aftermarket services and condition monitoring does not stop at faster repairs—it also elevates the reliability of the solutions provided. Repair facilities with access to monitoring data can implement tailored fixes that address not only the symptom but the underlying cause. This proactive approach extends the life span of equipment and prevents recurring issues, leading to higher levels of operational stability.
The Shift Toward Proactive Maintenance
The adoption of aftermarket condition monitoring represents a pivotal move toward proactive maintenance strategies. Retrofitting legacy machines with sensors and monitoring systems modernizes decades-old equipment, enabling them to meet contemporary efficiency and reliability standards.
Still, for many industrial and manufacturing businesses, this shift is not without challenges. Barriers such as upfront costs, the complexity of integrating new technology and the need for workforce adaptation can deter decision-makers.
Costs are often the first hurdle. Retrofitting legacy equipment requires initial investment in hardware, software and implementation. It can be tempting to delay upgrades to avoid these expenses. Yet, the long-term benefits far outweigh the initial financial outlay.
Integration challenges are another common concern, particularly when dealing with older machinery lacking digital connectivity. Customization is often required to ensure sensors and monitoring systems work seamlessly with existing equipment. While this process can be resource intensive, it transforms legacy assets into modernized tools of efficiency and reliability. Retrofitted machines close the performance gap with newer systems, delivering real-time insights that empower operators to make proactive, data-driven decisions.
Additionally, shifting from reactive to predictive maintenance involves developing new skill sets for employees, particularly in interpreting data and applying it effectively. The ability to identify and address potential issues before they escalate fundamentally shifts how teams work, turning maintenance from a reactive necessity into a strategic advantage to plan for downtime and equipment upgrades.