Pump users will know that the transition to U.S. Environmental Protection Agency (EPA) Final Tier 4 (FT4) is approaching, with regulations due to be fully implemented for all newly purchased off-road diesel engines by the end of 2018. But what does this mean for pump users? And how can we make the transition to FT4 a smooth one? FT4 is the most recent stage in a long journey laid out by the U.S. EPA Clean Air Act. The Act established emission reduction standards for off-road diesel-driven equipment including construction equipment, generators and diesel-driven pumps. The standards demand a reduction in the six common criteria pollutants—particulate matter (PM), ozone, sulfur dioxide, nitrogen oxides (NOx), carbon monoxide and lead. The most significant effect of the Clean Air Act on off-road diesel engines has been the reduction of NOx and PM.
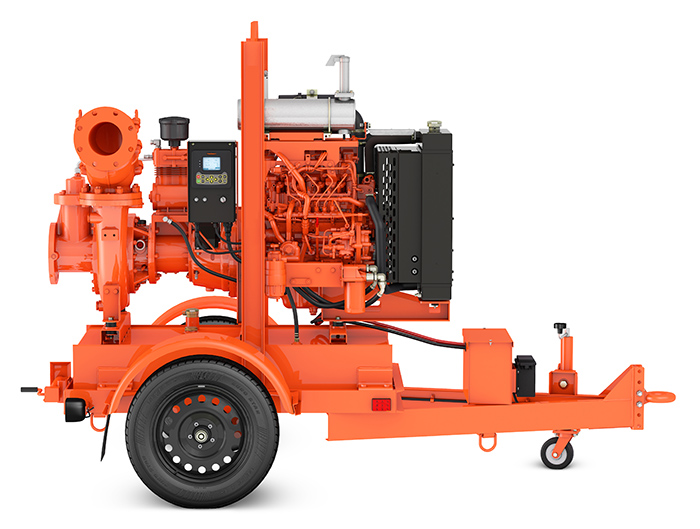
In-Cylinder & After-Treatment Technology
General emission reduction technologies fall into two categories: in-cylinder technology and after-treatment methods. The method and configuration used is determined by a number of elements including horsepower and equipment type. In-cylinder technology targets the combustion event when diesel fuel, injected into the engine’s cylinders, meets oxygen and is compressed. With enough compression, the diesel-oxygen mixture combusts, creating force that continues to move through the system. The primary goal of in-cylinder technology is to create a maximum efficiency combustion event, meaning that as much fuel is to be burned at a desired temperature with the least amount of resulting soot. The less PM made, the less soot is carried out in the engine’s exhaust. After-treatment methods treat the immediate diesel exhaust as it exits the combustion area using filters, metals and fluid additives to trap PM and chemically neutralize pollutants that develop during the combustion process. Field and application testing have shown that for most pumping jobs, engine models that use in-cylinder methods to meet emissions requirements have fewer maintenance problems and less downtime. In-cylinder methods also tend to be less expensive, which results in a less costly diesel-driven pump.Fuel for FT4 Engines
Ultra-low sulfur diesel (ULSD) fuel is the only fuel used in FT4 engines. ULSD is highly refined and formulated to contain less than 15 parts per million (ppm) of sulfur. Interestingly, this low sulfur recipe is the main reason why it is imperative that fuel storage containers are clean and free of condensation. Water in diesel fuel is the perfect incubating medium for fungus and assorted bacteria that form a slime that floats on top of the fuel. The slime reacts with metal to produce corrosive hydrogen sulfide that corrodes metals in fuel tanks, fuel injectors, connectors, etc. Follow these tips to keep your FT4 pump engine running smoothly:- Mount portable fill tanks at an angle with a drain at the low end to eliminate water.
- Ensure that portable tanks and nozzles are protected against dust, water and debris.
- Store bulk fuel inside and out of sunlight to avoid temperature extremes that cause condensation.
- Consider treating large stores of ULSD with an EPA-approved biocide to treat microbe waste.
Diesel Exhaust Fluid
Another must for FT4 engines that use selective catalyst reduction (SCR) systems is diesel exhaust fluid (DEF), a precise mix of 67.5 percent de-ionized water and 32.5 percent highly pure synthetic urea. DEF purity is vital. Even small concentrations of trace elements can contaminate an entire tank of DEF. If the required chemical interactions do not occur, the SCR system will malfunction and cause the engine to shut down. Although DEF is nontoxic and not hazardous, it is corrosive. As corrosion leads to particles in the solution, the International Organization for Standardization (ISO) recommends that DEF should not come in contact with copper, copper alloys, zinc, lead, chromium, nickel, aluminium, aluminium alloys, metal-coated plastics, or solder containing lead, silver, zinc or copper. Follow these tips when working with FT4 engines using DEF:- Never attempt to make your own DEF recipe.
- Do not use containers used for other materials, even if they have been cleaned. Detergents and contaminants residue in tap water will foul DEF.
- Use a coupler designed to limit air exposure during fills.
- Air can cause DEF to form crystals, so keep small containers tightly closed.
- Keep DEF storage areas at a constant temperature. Fluctuations affect DEF stability.
- Use corrosion resistant containers and accessories.
- Do not use tap water to top-off or stretch DEF. Contaminants can alter the DEF properties.