This technology self-lubricates, reduces friction and performs in wet or dry operating conditions.
09/02/2014
An article in the June 2009 issue of Pumps & Systems detailed a new technology to treat the surface of silicon carbides. The treatment is not a coating and not homogenous with depth. Since the publication of this article, independent parties have tested the treatment and returned the results from several applications. This article summarizes some of those tests.
Background
The technology involves treating a finished silicon carbide (SiC) component with a specific chemistry that etches the silicon from the surface of the SiC and leaves behind the carbon. This process occurs at the nanoscale. The silicon is removed, and the carbon—which was initially reacted with the silicon and sintered into the SiC substrate—remains in its original, covalently-bonded crystal lattice. During the reaction, the carbon further reorganizes into various nanospecies and creates a treatment zone as shown in Image 1.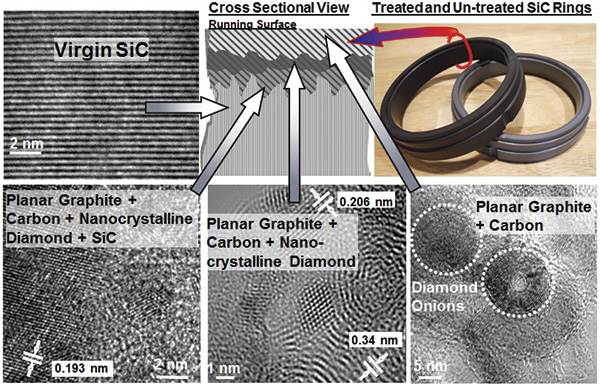
New Tests
All the recent tests, detailed in this section, had the hard/hard running combination of a treated SiC surface against another SiC-treated surface.Mechanical Seals
A seal pair was run in rigorous water test in conditions that typically damage sealing faces, as shown in Figure 1. The water test lasted for 350 hours. Next, the pump was drained, and the seal was run for another 75 minutes in dry nitrogen before a temperature spike stopped the test. This test proved extensive wet- and dry-running capabilities, even after running under rigorous wet conditions. No leakage occurred throughout the combined test.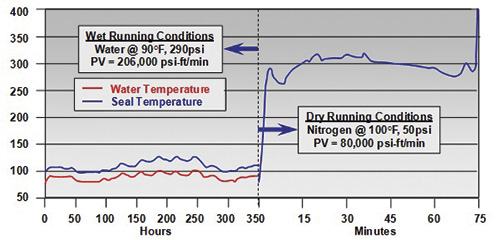
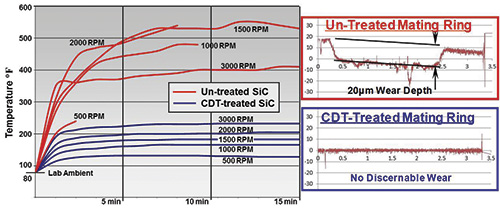
Bearings
The treatment also enhances the performance of bearings. One manufacturer demonstrated improved dry startup capability in a hydrodynamic bearing contained in a downhole pump. In operation, the pump runs dry for five to 10 seconds at startup before dirty water floods the bearing chamber. A test was performed in dirty water with 35 stop/starts—25 forward and 10 reverse. While this test typically destroys SiC hydro pads and thrust plates, the treated components were unharmed. The components were able to be reused in another pump and placed into service. Image 2 shows the results of a hydrodynamic bearing test with treated components. The test was conducted in water with a load that increased incrementally until twice the normal load-bearing capability was reached. As the image shows, the components experienced no discernible wear. Profilometry measurements also showed no discernible wear. The assembly may have been able to support even higher loads.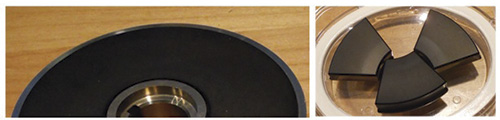