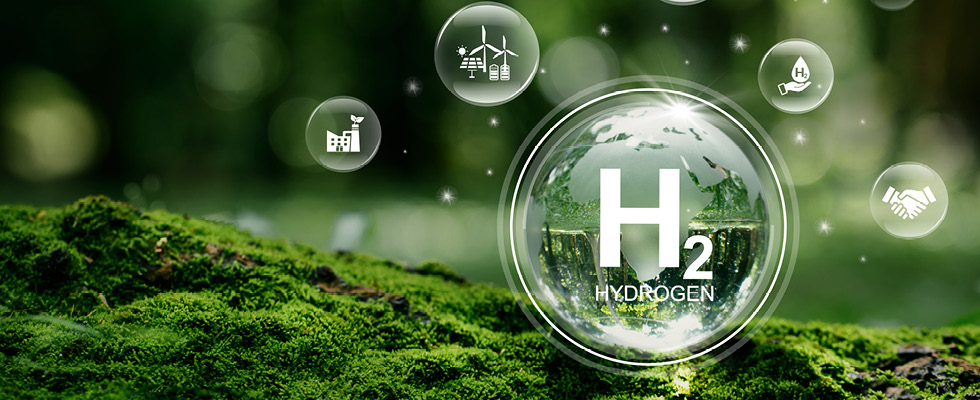
As the world pivots toward cleaner energy sources, hydrogen is gaining recognition as a pivotal player in the energy transition. The hydrogen economy promises to reduce greenhouse gas emissions and facilitate the storage and transport of renewable energy. However, the successful implementation of hydrogen technologies relies heavily on effective sealing solutions, particularly gaskets. This article delves into the trends shaping gaskets for hydrogen service and examines the implications of regulatory developments concerning per- and polyfluoroalkyl substances (PFAS) in the United States and Europe.
Understanding Hydrogen Service Requirements
Hydrogen, being the smallest and lightest molecule, presents unique challenges in sealing applications. Its properties—such as low molecular weight and high diffusivity—lead to increased permeation rates through traditional sealing materials. Consequently, industries utilizing hydrogen must adopt specialized gaskets designed to withstand these conditions while ensuring safety and efficiency.
As gaskets play a crucial role in various processes and equipment associated with hydrogen production, storage and distribution, some of the key applications of gaskets in hydrogen systems include the following:
1. Electrolyzers:
In hydrogen production via electrolysis, gaskets are essential for sealing components of electrolyzers, which separate water into hydrogen and oxygen using electricity. The integrity of these seals is vital to prevent gas leaks and ensure operational efficiency.
2. Hydrogen compressors:
Compressors increase hydrogen pressure for transportation and storage. Gaskets are used in compressor assemblies to maintain pressure integrity, prevent leaks and ensure reliable operation. High-performance sealing materials are required to handle the operational pressures and temperatures associated with hydrogen compression.
3. Storage tanks:
Hydrogen storage, whether in gaseous or liquid form, necessitates robust sealing solutions. Gaskets in storage tanks prevent leaks and maintain safety, particularly given the flammability of hydrogen. They must be resistant to the effects of cryogenic temperatures when storing liquid hydrogen.
4. Pipelines:
The transportation of hydrogen through pipelines involves numerous joints and connections, which require gaskets to prevent leaks. The sealing materials must endure varying pressures and environmental conditions, highlighting the need for durable and adaptable gaskets.
5. Fuel cells:
Fuel cells convert hydrogen into electricity, and effective sealing is essential for preventing leaks in the cell stack. Gaskets must provide a reliable barrier to ensure efficiency and safety in fuel cell applications.
Among the aspects to be considered when choosing the right gasket for your application are:
- Material compatibility: Keep in mind temperature, pressure ratings and chemical resistance since hydrogen can cause degradation and lead to premature failure.
- Seal design: Needed for appropriate gasket shape and thickness; based on the flange design.
- Regulatory compliance: Look for gaskets that meet industry standards. Opt for materials that are explicitly labelled as PFAS-free to mitigate environmental and health risks.
- Performance testing: Whenever possible, perform testing under real operational conditions to assess performance and durability.
- Monitoring and maintenance: This comes up after selecting and installing the gasket. A proactive approach can help to identify issues before they lead to failures.
Trends in Gasket Technologies for Hydrogen Service
The demand for hydrogen has prompted advancements in gasket technologies. Several trends are shaping the development of gaskets for hydrogen service:
- Traditional sealing materials, such as rubber, often struggle to meet the demands of hydrogen applications. Consequently, manufacturers are investing in the development of new materials that offer improved performance characteristics.
- Fluoroelastomers and polytetrafluoroethylene (PTFE) provide excellent chemical resistance and durability, making them suitable for high-performance hydrogen applications. These are increasingly being used in environments where hydrogen is present due to their ability to withstand high temperatures and pressures.
- Metallic gaskets are gaining popularity in high-pressure applications. They can provide excellent sealing capabilities and withstand extreme conditions. Materials such as Inconel and some stainless steels are often chosen for their strength and resistance to hydrogen embrittlement.
- Other materials, such as graphene and nanocomposites, are emerging in research for hydrogen sealing applications. These materials may offer superior mechanical properties and lower permeation rates, which are critical for maintaining gas integrity.
As industries become more environmentally conscious, there is a growing trend toward sustainable materials in gasket production. This trend is particularly significant considering PFAS regulations, which aim to minimize harmful substances in manufacturing processes. Manufacturers are also exploring innovative polymers that can replace traditional sealing options containing PFAS. The development of these sustainable alternatives is not only driven by regulatory compliance but also by the increasing consumer demand for environmentally friendly products.
The tightening of regulations concerning PFAS in both the U.S. and Europe is reshaping the materials used in gasket manufacturing. PFAS, often used for their chemical resistance, are now under scrutiny due to their persistence in the environment and potential health risks. In the U.S., the Environmental Protection Agency (EPA) is actively working to regulate PFAS, while Europe has introduced the Registration, Evaluation, Authorization and Restriction of Chemicals (REACH) regulation, which governs the use of harmful substances in products.
As a result, gasket manufacturers must prioritize compliance by sourcing materials that do not contain PFAS. This shift is prompting the industry to explore alternative materials that meet performance requirements without the environmental risks associated with PFAS. The move towards PFAS-free gaskets not only ensures compliance but also enhances safety and sustainability.
Challenges & Opportunities
While the trends in gasket technology for hydrogen service present numerous opportunities, they also come with challenges. The development of new materials must be matched with rigorous testing to ensure compatibility with hydrogen. Manufacturers need to conduct extensive research to understand how new gaskets perform under various conditions—such as pressure, temperature and exposure to hydrogen—over time.
As manufacturers seek out alternative materials to replace PFAS-containing products, securing a reliable supply chain becomes critical. The demand for sustainable materials may outpace supply, leading to potential shortages. Companies must invest in relationships with suppliers and ensure their materials meet the necessary performance and regulatory standards.
Furthermore, to navigate the complexities of transitioning to new materials and complying with regulations, collaboration across the hydrogen industry is essential. Gasket manufacturers, end users and regulatory bodies must work together to share knowledge, best practices and innovations. Industry standards can be developed to facilitate the safe and effective use of new materials in hydrogen applications.
In this respect, the future of gaskets in hydrogen service looks promising, with ongoing research and development paving the way for innovative solutions. As the hydrogen economy expands, the demand for advanced sealing technologies will continue to grow.
The trends toward environmentally friendly materials, improved sealing performance and regulatory compliance will be at the forefront of this evolution. As manufacturers adapt to the challenges posed by PFAS regulations and the unique requirements of hydrogen service, the industry can expect to see the emergence of more robust, reliable and sustainable gasket solutions.
The landscape of gaskets for hydrogen service is rapidly changing, influenced by technological advancements and regulatory developments concerning PFAS. As the hydrogen economy gains momentum, the need for high-performance sealing solutions becomes increasingly critical.
By embracing new materials and prioritizing sustainability, the industry can ensure the safe and efficient use of hydrogen as a clean energy source. The successful integration of innovative gaskets will not only enhance the performance of hydrogen systems but also contribute to a more sustainable future.
We invite your suggestions for article topics as well as questions on sealing issues so we can better respond to the needs of the industry. Please direct your suggestions and questions to sealingsensequestions@fluidsealing.com.