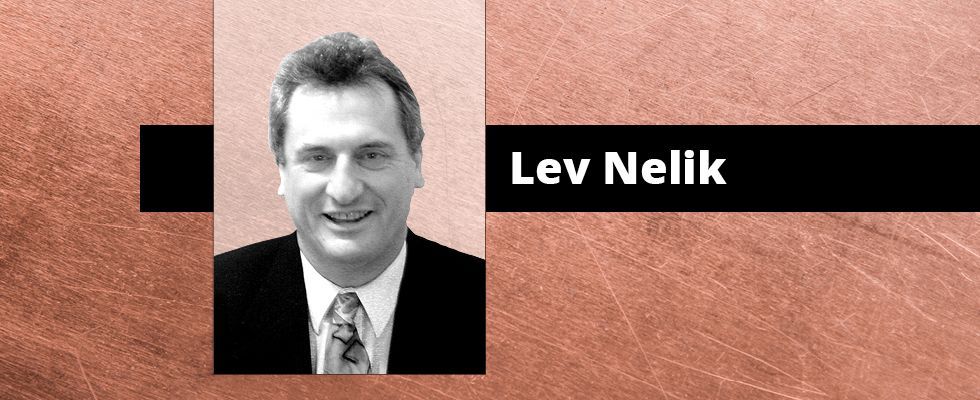
Small pumps do not mean small problems. If not installed or maintained properly, a simple clean water pressure boosting pumping system could cause many problems to apartment complex residents. A recent troubleshooting case of one such system illustrates multiple aspects of pumps hydraulics, bearings, and system panel controls and instrumentations all interacting together, and all needing to be understood properly in order to apply a solution.
A six-story building was supplied with drinking water by a local municipality. The water supply pressure was, depending on the time of day or night, between 5 to 6 bars (70 to 90 pounds per square inch gauge [psig]), which was enough to reach the tallest point (the elevation from the ground to the roof plus friction). Two-unit standby pumps—in case the main water supply was briefly interrupted—almost never had to kick in to maintain pressure for such rare emergencies.
However, over the years, as the city grew and more buildings were built, the supply pressure dropped due to increased number of water users, and the standby pumps started to come online more frequently. That, by itself, was not a big problem (other than some added cost of electricity to operate the pumps). But as pumps started to wear out, motor bearings started to rattle and vibrations propagated via piping throughout the building, waking up residents and creating a big issue that had to be addressed.
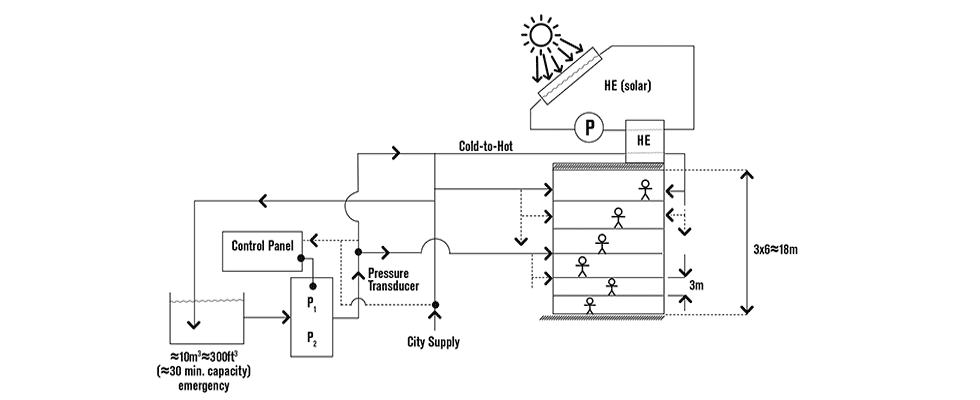
The first step was to understand exactly what was happening. Image 2 is a simplified sketch of a pump hydraulic performance curve versus a system curve. The nameplate of each pump (five-stage model DPVF 18-50) shows a design point of 5 liters/second at 5.4 bar (54 meters), operated by a 7.5-horsepower (hp) motor at 2,880 revolutions per minute (rpm). The height of the building (18 meters) plus friction losses (which we calculated) appears to be sufficient for the pump to operate and move water to the roof properly. Some of the water branches directly to the apartments as a cold source, and some is pumped to the roof where it is heated by a solar panel and a heat exchanger, and then proceeds to the apartments (Image 1).
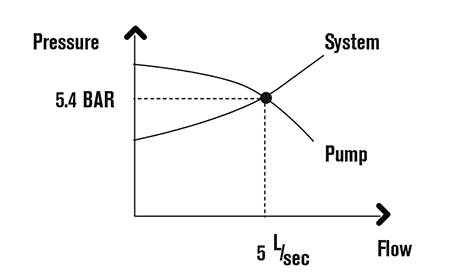
The next step was to ascertain the reason for the noise. Using a vibration analyzer, we determined the noise emanated from the motor bearings of one of the pumps and needed to be replaced. The other question was why the pumps came online much more frequently as compared to the earlier years. To do that, we had to test the system to determine pressure fluctuations over time (Image 3).
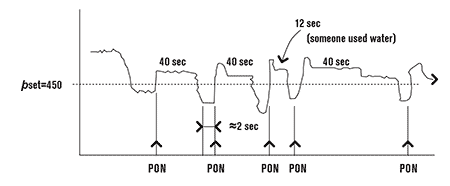
With the set point at 450 kilopascal (kPa)—4.5 bar—as set via the control panel parameter, and the system normally operating at 5 to 6 bar in the past, the pressure rarely (other than rare emergencies of supply water loss) used to drop below the set point. In our test, however, we found that pressure would drop below the set point frequently, causing the pumps to “race,” or come online and offline. During the day, the pressure always remained above at least 5.2 bar, and at night it varied between 4.6 down to 4.2 bar, thus triggering the start of a pump.
The peculiar fact of why the daytime pressure was generally higher than the nighttime could be explained by assuming the municipality estimated a lower water use at night and, thus, reducing overall system supply pressure. Unfortunately for the area the building was in, this resulted in pressure not being sufficient. The reason for the pumps continual “raising” at night was because the operating pressures and set pressure happened to be “just wrong”—system pressure dropping from, say, 4.6 bar to 4.4 bar (triggering a pump start), but then soon restoring itself back to 4.6 bar, shutting the pump off.
Such continual fluctuation of the pressure around the set point of 4.5 bar was what caused the “raising,” and then the continual noise on and off, which residents would hear at night.
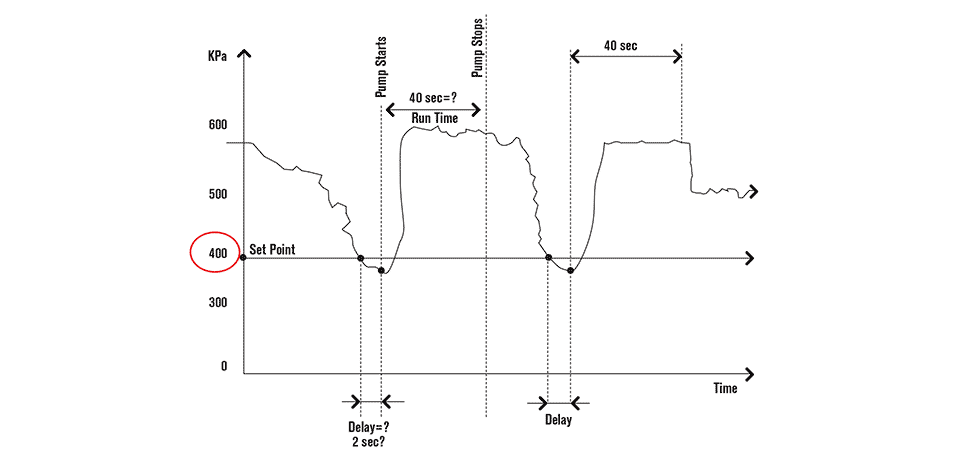
Our solution was straightforward and simple: drop the set point pressure to, say, 4 bar (Image 4). Calculations showed that as long as a total pressure remained about approximately 3.5 bar, it would be sufficient to supply water to the top of the building—including static head and friction in pipes.
Some further fine tuning was also done, to occasionally make the pumps start, by lowering a set point to 3.8 bar (Image 5). This was done so that the water in an emergency supply tank would not always stay settled but would get periodically renewed by a started pump.
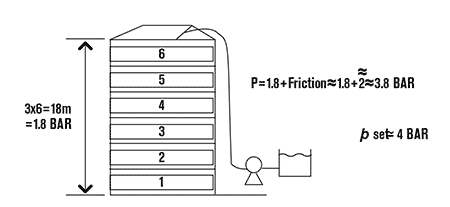
Having done that, even with a bad bearing, the pumps were no longer a problem since they would rarely start up, and if they did, their operation would be only for a short time. Eventually, however, a bad bearing would be replaced to make sure the pump would not fail catastrophically.
Thorough Analysis a Must
A thorough analysis supplemented by a field testing of the entire pumping system—including pumps, valves, gauges, control, supply tanks, etc.,—is a must for proper understanding of an issue. Once understood, a solution is usually clear and straightforward. Even though this case was for a small residential water supply pump, a similar process and troubleshooting techniques should be applied for any system—regardless whether the pumps are 1 hp or 1,000 hp.
As a final quiz and a question to our readers: What other things should you analyze to try to solve the problem in this case?
References
1. VPRS Pumps Repair Specifications Standard, P&S: www.pump-magazine.com/pump_magazine/specifications/specifications.htm
2. Nelik, L., “Calculating vs. Estimating Pipe Velocity,” P&S, January 2019
3. Nelik, L., “Bearings Life Extension and Reliability Features of Modern ANSI Pumps,” Proceedings of the 2nd international conference on equipment reliability; Houston, Texas; Nov. 15-18, 1993
The following authors also contributed to this article:
- Dani Kazakov, DK Avodot, Israel
- Leonid Avrukh, Beer Sheva, Israel
- Scott Carlson, MTH Pumps,
- Chicago, Illinois
- Arjan Hoogerbrug, DP (Duijvelaar) Pumps, Holland
To read more Pumping Prescriptions columns, click here.