Viscous products such as processed cheese, peanut butter, meat, chocolate and whipped toppings can leave operators with cavitation issues when using traditional pumps. Low inlet pressures, high pumping pressures and process lines that may have relatively low levels of product in them all create issues that increase maintenance overhead and reduce pump reliability. Twin screw pump technology is designed to handle low inlet pressure applications, operate reliably at high differential pressures and increase run times. Although these units usually mean a higher initial investment, they can run at higher flows and speeds to reduce the size of pump needed. When a process has a low inlet pressure, rotors or lobes within a pump cut across its inlet. This can increase the inlet pressure required for the pump to run. Rather than blocking the inlet, however, the screws in a twin screw pump create an auger effect that actually helps the fluid into the pumping chamber. By using non-galling internal materials and precision engineering, the pumps can be constructed with exceptionally tight internal tolerances to create even greater suction and increased pumping efficiency. The smooth operation of this style of pump further reduces slip pulse in low inlet pressure, low viscosity and high pressure conditions.
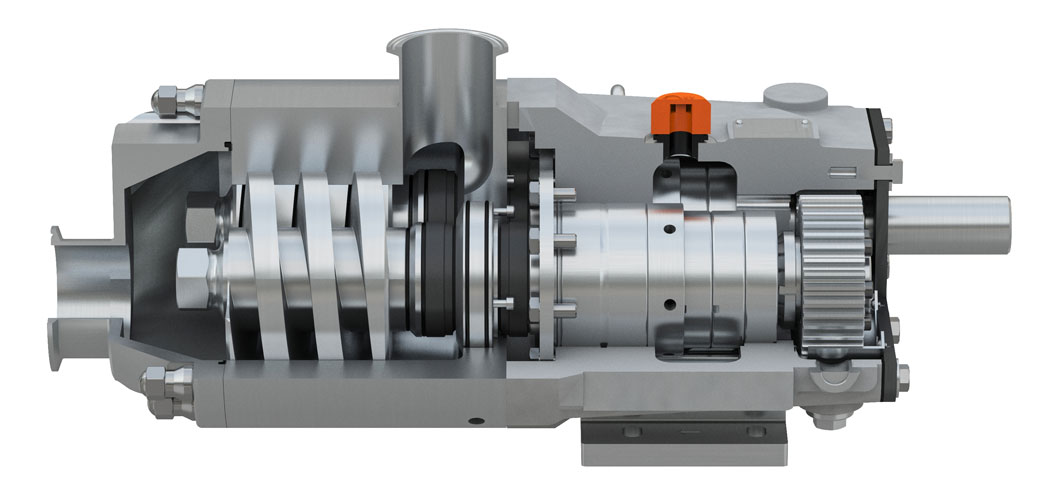