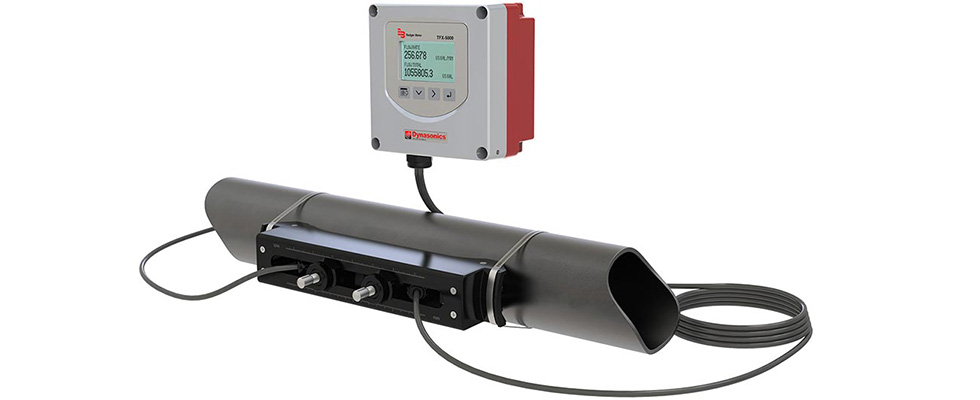
Building owners are seeking to deploy advanced flow and energy measurement solutions to obtain high performance. The reliability and efficiency of pumps and other components of hydronic heating, ventilation and air conditioning (HVAC) systems can impact the bottom line.
Challenges for Facility Operators
Commercial and industrial businesses spend much of their building costs on processing hot and cold water and distributing it around their facility. There is an increased focus on determining the correct amount of this resource required.
Hydronic balancing is the process of optimizing the distribution of water in a building’s heating or cooling system by equalizing the system pressure, so it provides the intended indoor climate. Recently, building hydronic systems have employed variable speed equipment and pumps to vary the system’s flow. This technique matches the water flow (gallons per minute) to the demands of the building without wasting energy and reducing the wear on equipment.
Need for Flow Measurement
Flow metering, in particular, is key to the reliable operation of HVAC systems that provide climate control in large complexes. Installing this technology at multiple points in cooling tower and HVAC systems is a best industry practice to minimize water consumption, energy expenses and repairs to pumps and other equipment.
For facility owners/operators, the effective use of flow measurement can assist with system capacity analysis, individual building cost allocation, energy efficiency initiatives, hydronic system optimization and equipment troubleshooting. Typical flow applications in building design, construction and operation include glycol and hot/chilled water, domestic water/domestic hot water, makeup water/blow down, steam/steam condensate, boiler feed water, cooling towers, chiller systems, energy audits and cost allocation.
In some cases, building operators find it necessary to install flow meters upstream from pumps to provide flow data alerting them to situations leading to potential problems caused by low-flow conditions. Otherwise, the result can be expensive pump repairs or even system shutdowns.
Choice of Metering Solutions
End users involved with commercial and industrial buildings can choose from a broad range of flow and energy measurement products for their facility’s hydronic HVAC systems. Common choices range from electromagnetic flow meters to vortex, differential pressure, positive displacement, turbine, disc and ultrasonic meters. The typical flow meter selection criteria include accuracy requirements, installation environment, output requirements, interconnectivity needs, maintenance and serviceability requirements and budget limitations.
Ultrasonic transit time flow meters have become a popular choice for HVAC-related applications. With this technology, ultrasonic waves transmit upstream and downstream through the pipe wall and the liquid flowing in the pipe. By measuring the difference in the travel time and knowing the pipe size, the meter determines the velocity and flow rate.
Transit time ultrasonic flow meters use two transducers, which function as both ultrasonic transmitters and receivers. They operate by alternately transmitting and receiving a frequency-modulated burst of sound energy between the two transducers. Since ultrasound energy in a moving liquid is carried faster when it travels in the direction of fluid flow (downstream) than it does when it travels against fluid flow (upstream), a differential in the times of flight will occur. The ultrasound’s time of flight is measured in both directions, and the difference in time of flight is used to determine the velocity of the fluid.
When an existing in-line or insertion flow meter fails and is difficult to replace, or additional metering is needed, the best choice can be a noninvasive solution like an ultrasonic clamp-on flow meter. Designed to attach to the outside of pipes, this type of meter does not contact the internal liquid, allowing for installation without shutting down the operation. Hot tap, in-field drilling and welding are not required when installing the device.
Ultrasonic clamp-on flow meters provide reduced installation costs, flexibility across pipe sizes, elimination of pressure head loss and no moving parts to maintain. This meter design allows for routine maintenance activities without having to cut into piping.
Recent Technology Innovations
Ultrasonic transit time flow meters have gained wider industry acceptance for measuring volumetric flow rates in clean liquids as well as liquids with small amounts of suspended solids or aeration. Also, the availability of these devices has increased. The current generation of ultrasonic flow meters is offered with configurations and features to meet particular application requirements. They include diagnostics that take the guesswork out of isolating process or application problems. Users are alerted to out-of-specification flow conditions and can access a history with the most recent alarm, error and event codes.
Using an ultrasonic transit time flow meter, building operators can measure energy costs for both hydronic chilled and hot water applications. Where dedicated thermal measurement is required, as in the case of a distributed chilled water system, the devices can be used with dual clamp-on resistance temperature detectors (RTDs) for British thermal unit (Btu) energy measurement.
A key feature of energy monitoring is the data logger. A second requirement is data retrieval. A number of the new meters offer secure digital (SD) card data storage and do not require software or download cables. With built-in data logging and a real-time clock, the most advanced ultrasonic flow meters record flow rate, total and diagnostic information with a time/date stamp—providing the baseline and load profile information needed to optimize pump efficiency. Meters designed to use a micro-SD card can store a large volume of backup data for troubleshooting or reporting purposes.
Typical Industry Applications
Building operators are faced with mapping all the submetering points for energy or water usage, as well as measuring flow at both the design rate and minimum rate required for seasonal operation. This can be accomplished by using noninvasive ultrasonic flow technologies without disruption to the hydronic system.
Ultrasonic clamp-on flow meters can control the pumped condenser water, condenser water blowdown and evaporation. Their power and communications features can be added or replaced when system requirements change. The meters can be installed outdoors within a cooling tower system so that the owner receives precise measurements for sequence and cycle control while using the flow data to help identify limits of operation.
In addition, the latest ultrasonic transit time flow meters can integrate metering components with flow and temperature sensors to measure energy costs in diverse heating and/or cooling applications. Users can pair the meters with cloud-based advanced metering analytics (AMA) software to provide flow data for consumption analysis, leak detection and other purposes. These devices were developed for data-centric operations to interface with building automation systems for real-time flow balancing using Modbus RTU, BACnet MS/TP and BACnet/IP.