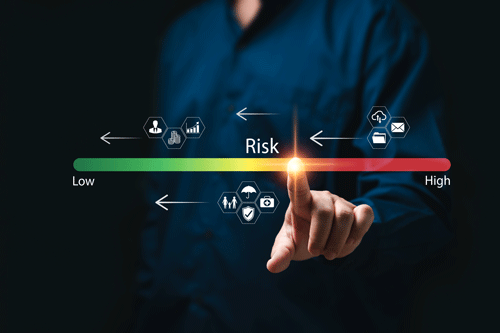
When examining bearing failure modes, external factors are often the cause of failure rather than a manufacturing defect. While a manufacturing defect is possible, it is more common to deal with environmental, human and application damages. Each brings a different series of failure opportunities that must be understood and addressed to ensure the equipment runs reliably and efficiently. Foreign contamination, improper installation and maintenance, potential electrical discharge and temperature all play a major role in reducing the operating life of a bearing. These factors, and others, can be mitigated with a mix of proper handling, installation techniques and technological advances.
Environmental factors carry significant responsibility in determining the performance and longevity of bearings. The operating environment directly impacts the sealing and lubrication of the bearing. Improper material selection will lead to premature wear, failure and reduced efficiency. Understanding how environmental factors can be mitigated is crucial for ensuring the maximum bearing function and service life is achieved.
In environments with high levels of dust, dirt or other abrasive particles, the risk of bearing failure is high. Without proper sealing, contamination can enter the bearing unmolested and cause catastrophic damage to the bearing races and rolling elements. Foreign particles entering the bearing create abrasive wear that leads to reduced performance, elevated operating temperatures and eventual failure. As the particles enter the lubrication of the bearing, they act as a lapping compound that creates uneven wear on symmetrical surfaces.
Proper external sealing can mitigate the effects of environmental contamination. Lip seals and bearing isolators offer various levels of protection based on the needs of the environment and how critical the asset is. Lip seals offer protection at the expense of friction, and bearing isolators do so at the expense of price.
Lip seals are often pressed into the bearing housing externally and use a single or double spring-loaded inner “lip” to ride against the rotating shaft. If the seal is too tight, a wear groove will occur on the shaft and allow contamination to pass through. If the seal’s inside diameter is too large, contamination can pass through the void between the seal and shaft. Proper machined shaft and housing tolerances are critical to the life span and efficacy of the seal. This basic level of protection is great for low level contaminant environments.
Bearing isolators are the next level in sealing protection for bearings. They use a similar concept to bearings in that they have a stationary and a rotating component to create a seal. The stationary component is pressed into the external housing while the rotatory component seals to the shaft using an O-ring. The isolator uses a series of internal tongue and grooves with O-rings to create a labyrinth sealing effect that can eject foreign particles before they reach the bearing, allowing used grease to drain.
Both methods of sealing require proper material selection. Elevated temperatures may require a fluoropolymer elastomer and synthetic rubber compound to ensure the seals do not melt. Chemical factors may require bearing isolators of glass-filled polytetrafluoroethylene (PTFE) in lieu of bronze due to corrosion considerations. The nature of the contamination present along with the location of the installation should determine the base material when selecting a sealing method.
Human factors affect a piece of equipment from the beginning of manufacturing. Most people can only determine how the equipment is treated once it arrives at the intended facility. At that point, installation and maintenance practices can help ensure a piece of equipment runs optimally.
When a piece of rotating equipment is installed, it must be aligned with the driven equipment to ensure the bearings run within manufacturer application-based tolerances. Various factors including rotations per minute (rpm) and running temperature must be accounted for to ensure in-operation alignment is correct. Equipment rpm determines the amount of run clearance that is available. Operating temperature will determine the thermal rise of each component in the driven system. With an understanding of those factors, a technician can then use a laser system to ensure proper operational alignment tolerance is selected and achieved.
Care must also be taken when linking equipment together after alignment. In a direct drive application, the driving and driving equipment operate in-line. The coupling halves should be able to be positioned without force and locked into position using set screws or similar mechanical methods. Forcing a coupling into position can result in false brinelling and axial thrusting. False brinelling is the presence of impact craters in the rolling element raceways. These craters act as a hammering device on the rolling elements and will continue to deform the raceways and rolling elements until they cause premature, often catastrophic, failure.
Axial thrusting causes the rolling element to operate outside its intended space. This often leads to a wider surface of contact than designed. The wider surface contact leads to an increase in operating temperature, and that in turn leads the material to lose structural integrity and fail prematurely. The alignment should be performed with the equipment involved and should be in a free state with the couplings positioned and secured after the fact, if possible. If the application is belt driven, a roller bearing should be specified on the drive end of the equipment. A pulley alignment should be performed to ensure proper belt tracking. The belt(s) should then be preloaded based on the application and bearing size to ensure proper function of the roller bearing, which is designed to act under a radial load.
Bearing life is also affected by what the application equipment is doing and how it is powered. The job of the equipment should be examined to ensure the proper bearing and lubrication is selected. Some applications, such as a vibratory motor, require bearings with more clearance and high-pressure grease to withstand the effects of brinelling that come from vibration. Higher speed applications will require bearings machined to tighter tolerances.
It is also critical to know if the power is being delivered through a drive due to circulating currents created by the conversion of energy in the drive. Proper mitigation techniques must be used to eliminate or reduce the effects of circulating currents. This is crucial to the longevity of the equipment.
To combat circulating currents, a low-impedance path to ground must be present. This transferral from the rotating shaft to ground can be accomplished using a carbon-based shaft grounding brush or shaft grounding ring using conductive microfibers. Both methods should be paired with an insulated or hybrid insulated bearing. This gives the damaging currents the best path to ground without damaging the bearings. Other forms of bearing current protection are available that address the potential issues at the variable frequency drive and incoming power source.