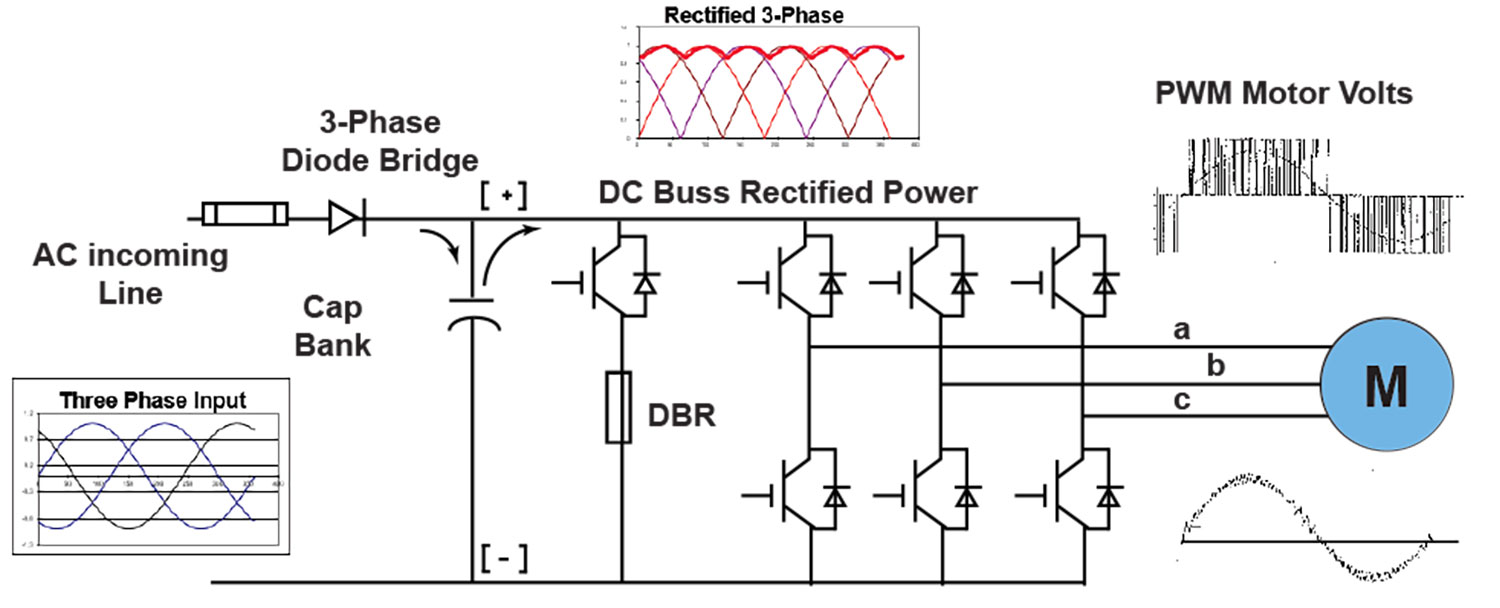
The motor’s objective is to create torque and, ultimately, the rotary motion of another piece of equipment. Torque depends on a flux wave in the air gap and the relative speed of the rotor to this flux wave. The strength of the flux wave depends on the voltage and frequency applied to the stator terminals, as shown in Equation 1:
Ø = V/f
A load applied to a motor reduces the rotor speed (increased slip). The speed will become constant when the motor torque matches the load torque but the rotor stalls if the load exceeds the maximum torque (breakdown torque).
A VFD controls both voltage and frequency to produce constant flux, thus maintaining maximum torque at various speeds. The VFD rectifies the alternate current in the inverter module and then converts it back to the alternate current through wave modulation.
In this process, harmonic waves and short-duration insulation eroding voltage spikes are also generated in magnitudes dependent on the VFD’s carrier frequency and its circuitry, along with any included filtering, if required. The output voltage of a VFD is critical information for the motor manufacturer. The motor manufacturer should consider the VFD’s effects in terms of size, cost and the best motor-VFD performance. Here are key points to consider when designing a custom-made motor to operate on a VFD.
Torque
The flux and current density create a current concentration at the upper portion of each rotor bar (skin effect). This effect is responsible for generating starting torque (locked rotor torque) and maintaining the starting current (locked rotor current) under a target value during the mains-powered motor’s acceleration.
When a VFD is involved, the skin effect is no longer pertinent to enable a motor to accelerate and maintain a low starting current. Still, it is necessary to limit the VFD-generated time-harmonic due to its capacity to create heat losses. However, the breakdown torque is critical and should match the application’s needs for fast speed response, loading and achieving the desired speed in the targeted constant power zone.
It is essential to size the rotor properly. Increasing the number of rotor bars or its length, thus also modifying the stator dimensions, are examples of design adjustments to increase torque. The VFD must supply enough current to generate the required torque in regular and overload operation, but a specially designed motor to match a VFD can limit current to avoid applying a larger and more expensive VFD. This action results in a lower system cost of acquisition.
Torque Pulsations
When the mains power a motor, slot magnetic leakage saturation, rotor static, dynamic eccentricities and the number of rotor and stator slots, among other things, can generate harmonics to the fundamental frequency. The results are losses and mechanical stresses, which the VFD-introduced harmonics increase in quantity. These harmonics create parasitic radial torque, resulting in extra vibration plus heat if not addressed when designing the motor.
Efficiency
Consumption of electricity by industrial electric motors is increasingly becoming a critical motor design criterion. Many countries have adopted regulations covering smaller AC induction motors (below 375 kW), as they represent, by far, the largest quantity of induction motors in operation and, thus, have the most impact on electricity consumption.
While there are no regulations for large machines up to several megawatts, efficiency is relevant because they are responsible for 23% of electricity consumption.¹
Efficiency is the ratio between power delivered at the shaft and the input power to the motor terminals. Both the International Electrotechnical Commission (IEC) 60034-2-1 and Institute of Electrical and Electronics Engineers (IEEE) 112 have helped the industries develop test procedures to determine motor efficiency by testing or calculating losses. Testing for efficiency includes determining the motor losses known as:
- stator I²R
- rotor I²R
- friction and windage
- core losses
- stray-load losses
The stray-load losses, which occur on the stator and rotor cores and other metal parts, the eddy current loss in the rotor bars, and stator windings are challenging to predict and measure. Accounting for VFD-generated harmonics compounds this challenge.
Cooling
Heat removal capacity is a determining factor in the machine size and compliance to its temperature rise class. The motor manufacturer must design an efficient internal airflow path and provide independent external air cooling for constant torque applications.
Vibration
Standard two-pole motors have a critical speed below their nominal rpm, which resonates amplifying vibrations to the point of damaging the equipment if the drive operates the motor at or near the critical speed. The motor manufacturer will need to know whether the operating speed range will intersect the critical speed to provide a solution that can be vibration dampening, modifying the critical motor speed, or programing the VFD to avoid the critical speed region.
Insulation
The voltage waveform supplied by VFDs consists of pulses with fast-rising peaks, behaving like surges in the connected motor winding. These differ from regular sine waves. The impedance mismatch between the power cables and the stator will augment the voltage by reflection. Over time, the stator insulation will deteriorate and fail if these fast-rising peaks are not addressed.
An actual waveform depicting the total harmonic distortion is valuable information but not always supplied, forcing the motor manufacturer to make assumptions. Over or underestimating the harmonics results in an additional cost to the user. In the absence of such data, a manufacturer may decide not to offer a motor due to the high level of risk.
Sourcing Motors & Drives
Sourcing a motor and variable frequency drive (VFD) from the same manufacturer can offer benefits. Medium-voltage motors with ratings above 375 kilowatts (kW), up to several megawatts, are built-to-order, custom-designed and expensive. Pairing a motor with a VFD system designed and produced by the same manufacturer can offer:
- maximum system longevity
- dependable, continuous operation
- reduced electricity consumption
If the motor and VFD are acquired from separate sources, an effective exchange of information between the equipment providers and the system integrator is necessary to match the specified system application outcomes.
The above decision factors do not cover all aspects when designing an electric motor or integrating a VFD but are provided to demonstrate the complexity of the custom motor design process, which may encourage the integrator or end user to purchase the equipment from the same manufacturer.
References
The Induction Machines Design Handbook – 2nd Edition Ion Boldea/Syed A. Nasar
IEC 60034-2-1 Rotating Electrical Machines – Standard methods for determining losses and efficiency from tests.
IEEE std 112 – Standard Test Procedures for Polyphase Induction Motors and Generators.
NEMA MG1 – 2016 National Electrical Manufacturers Association
U.S. Department of Energy – Premium Efficiency Motor Selection and Application Guide.