After many years of study, analysis and discussion, the U.S. Department of Energy (DOE) has released new rulemaking that defines a pump system efficiency test procedure, 10 CFR Parts 429 and 431 – Energy Conservation Program: Test Procedure for Pumps. Energy conservation has been a focus for both the private and public sectors for years, but this is the first time the DOE has developed rules to determine the efficiency of pump systems. Pumps represent more than 50 percent of all potential energy savings of motor-driven loads. Furthermore, energy costs associated with pumping applications represent approximately 40 percent of the total cost of ownership for the life of that pump. Because pumps are a major consumer of electric energy, the DOE pump system guidelines have been the topic of discussion for several years. This is the first time that the government has taken steps to address energy usage in the previously unregulated pump industry. This rule does not include information on any action that the DOE will take against inefficient systems; however, it lays the groundwork for future rules detailing efficiency level requirements and subsequent penalties for noncompliance. Many pump users remember the process that the DOE and the Environmental Protection Agency (EPA) underwent to develop minimum efficiency standards for electric motors nearly a decade ago and the resultant laws governing minimum allowable motor energy use as detailed in 10 CFR Part 31 of the 2010 Energy Conservation Standard for small electric motors. The process started with the Energy Policy Act of 1992, which required that certain types of motors sold in the U.S. after October 1997 meet or exceed minimum efficiency standards. Efficiency guidelines continued to expand with the Energy Independence and Security Act, setting the minimum efficiency for motors above 1 horsepower (hp) (signed in December 2007), followed by the DOE Small Motor Rule that set minimum efficiency requirements for certain electric motors between 0.25 and 3 hp in 2015.
Measuring Pump System Efficiency
Pump system efficiency typically has been measured only when a system is operating at 100 percent capacity (speed, flow and head pressure). This full load and speed point of operation, while important, did not represent where most installed pump systems ran for long periods of time. Even if throttle valves or other mechanical bypass means were used to vary system flow and pressure, the overall system rarely ran at 100 percent capacity. This new efficiency test procedure requires that measurements be taken at different key load points, gauging the system's efficiency at varying loads to provide a more holistic understanding of the pump system's overall energy use.Addressing Pump System Efficiency
This rulemaking will be applied to new pump systems and will not mandate any updates to installed pumps. The regulations underscore the importance of energy efficiency for all pumping systems across all industries—both to reduce environmental impact and to improve the bottom line.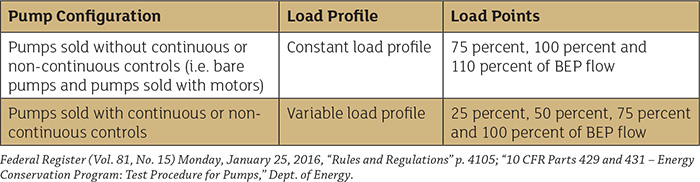
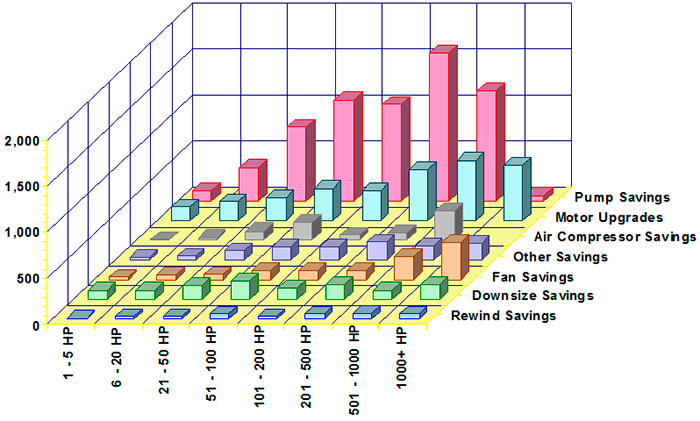
Contributing to the Guidelines
As with the majority of federal guidelines, this rule was developed through years of study and with the input of independent industry groups. The Air-Conditioning, Heating and Refrigeration Institute (AHRI) is one group prominently referenced in the legislation. This rule comes on the heels of that organization's recently published VFD standard, AHRI Standard 1210 (IP) and 1211 (SI) Performance Rating of Variable Frequency Drives, which addresses system efficiency by focusing on the drives. By adding a VFD, it is possible to reduce a pumping system's electrical consumption by at least 30 percent. However, it was difficult to understand which drives provide greater process efficiency. The AHRI standard represented the first independent, nationally recognized performance standard in the industry for VFDs, allowing users and consulting engineers to better specify VFDs based on published performance data verified by credible third-party testing. To achieve the Standard 1210/1211 Certification, manufacturers must complete a detailed process, including independent testing of three VFD measurements:- Combination drive/motor efficiency at defined speed and load points
- Total harmonic current distortion at drive input terminals
- The rate of voltage change over time (Dv/Dt) of drive output waveform measured at motor input terminals with 6-, 15- and 30-meter cable lengths
Additional VFD Benefits
With a variable frequency drive, pumping systems can also benefit from:- Smart pump control
- Remote access and monitoring
- Predictive maintenance