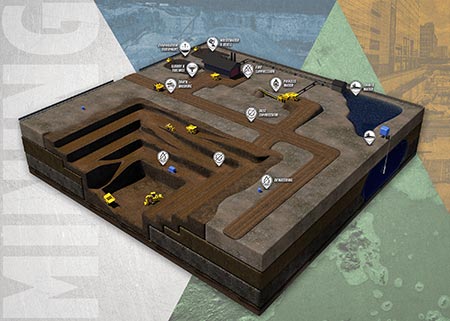
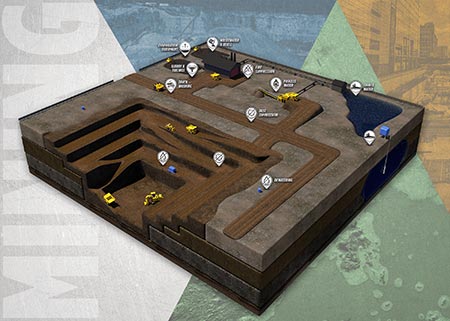
In the mining industry, pump efficiency and reliability are essential for profitable operations. With so many application needs—including general dewatering, slurry and tailings removal, source and process water, truck washing and dust suppression—how can pump performance be maximized? While most of the mining industry relies on diesel-driven pumping, portable electric-driven pumps are emerging as another popular choice—one that offers application versatility, as well as performance and return on investment (ROI) benefits.
Here are a few considerations to keep in mind when assessing pumps for mining:
The Benefits of Electric-Driven
Versatility
Electric pump packages are hardly one-size-fits all, and that versatility can be essential for the ever-changing needs of mining sites. For example, portable electric-driven pump packages are typically paired with variable frequency drives (VFDs) so that users can achieve multiple applications with one pump by simply adjusting the speed.
For mining applications with varying duty points, electric-driven packages can meet the specific efficiency and performance requirements of each application. This flexibility maximizes return on investment for electric-driven packages. On a mine site, this is particularly useful in applications such as dewatering, due to flooding or other emergency problems where a single unit can be used to respond immediately.
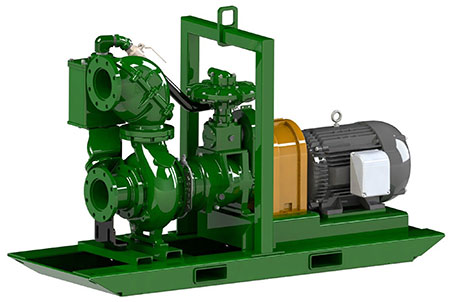
Clean running
With environmental regulations becoming more stringent, pumps need to be safer, cleaner and more efficient than ever. Electric-driven packages can be an environmentally friendly option for mining applications. Spontaneous combustion from non-exhaust emissions and leaks in diesel engines can be a safety and environmental concern in mine sites. Electric motors eliminate emissions and mitigate hazardous waste cleanup from leaks and other Environmental Protection Agency (EPA) regulations. These environmental benefits also lead to financial ones, since cleaner running equipment minimizes the cost of dealing with emission issues.
End-to-end performance
Another benefit of using an electric-driven pump package with a VFD is that it can cover a larger pump operating range on the performance curve. In an electric-driven package, when the VFD connects to a power source, it converts the input frequency to the desired output frequency, changing the rotational speed of the motor. This allows the pump to reach the entire pump end’s performance curve range. In contrast, with Tier 4 diesel engine pump packages, the operating range is restricted to a specific area within the performance curve and has limitations on variable loading. This range restriction is mostly due to the new exhaust systems used on diesel engines. These must be kept extremely hot so they burn off particulate to meet emission regulations. When a diesel engine operates at slower speeds, it is usually also underloaded. This can cause regeneration issues in the engine or a buildup of particulate in the exhaust system—and that will eventually lead to a failure and repairs. Previous engine tiers were not as sensitive to slower speeds as the latest Final Tier 4 engines.
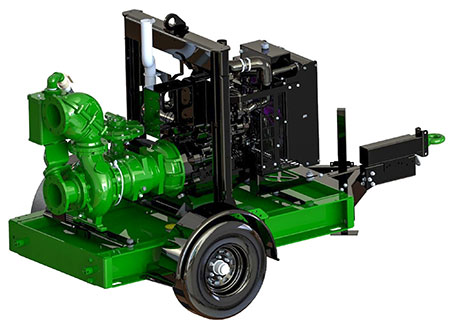
The Benefits of Diesel-Driven
While electric-driven packages have cost benefits and some performance advantages in certain types of applications, there are still circumstances when diesel-driven packages are the better choice. For example, consider the operating environment. To use an electric-driven pump package, the mine site will need to have access to on-site power. Ideally this power should run across the entire mine so the pump can be used in multiple applications (fixed or portable).
If site power is unavailable, a generator is needed, and this can add to the pump package’s initial cost. In this case, a diesel-driven pump package may be a lower upfront investment.
Diesel-driven packages are often a good choice for temporary applications. They can be commissioned to dewater a pit due to increased infiltration for a week, and then sent to bypass process water at a cooling tower. Installing permanent power to each of these temporary jobs within one or multiple mine sites would not make sense financially.
Realizing Cost Savings & ROI
As with any capital expenditure, it is important to not only consider the initial cost of the equipment, but also the lifetime cost of maintenance, service and operation.
Over the last decade, the cost to manufacture electric-driven pump packages and VFDs has gone down while the price of diesel engines has increased. In addition to this initial investment, the operating and maintenance costs on electric-driven pump packages are typically less than diesel-driven ones.
For example, the kilowatt energy cost to run electric-driven pump packages is typically lower than the cost of burning diesel fuel. Electric-driven pump packages also eliminate the need and cost for fuel delivery. The after-treatment system of Final Tier 4 diesel engines also means other operating and maintenance expenses. These include diesel exhaust fluid, which must be filled whenever the unit is in use, and maintenance costs for servicing after-treatment components including diesel particulate filters, diesel oxidation catalysts and selective catalytic reduction (SCR) systems.
Preventative maintenance costs are also generally higher for diesel-driven packages as they require engine oil, filters, fluids, and coolants to be checked and changed on a regular basis.
Making the Choice
From an overall selection perspective, both diesel- and electric-driven packages will stand up to the arduous duty of mining applications. The two package types are equally built to last and accelerate performance in tough, rugged environments.
The decision ultimately depends on the characteristics of the mine site, particularly the availability of electric power. Then factor in cost: from initial purchase to maintenance to operation. In both cases, users can be confident that either a diesel- or electric-driven package will provide safe, protected operation while meeting the needs of demanding mining applications.