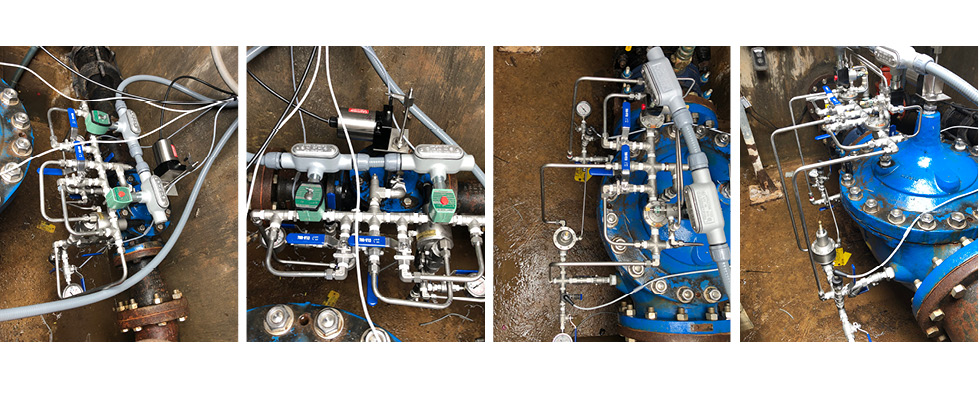
Roanoke, Texas, is a small city with charm and all the amenities of a big city. Located just north of Fort Worth, it has a population of just under 10,000 people. The city gets its water from the City of Fort Worth and has always controlled pressures in the system by using manually adjustable control valves.
A few years ago, three of the city’s control valve vaults were upgraded to full stainless steel pilot systems on the control valves. This is a great option for any pilot operated valve, as stainless systems cut down on maintenance and last longer than brass and copper systems. At that time, it was also suggested they may want to consider automating these valves.
It was proposed they could upgrade the manual valves to enable full electronic control, essentially converting the valves into intelligent valves while still utilizing the new stainless hydraulic system as an emergency backup system. This would enable remote monitoring and adjustments of each valve via the supervisory control and data acquisition system (SCADA) the city already utilized.
The city agreed this was a great idea and added it to their budget. The project was recently completed, with three 10-inch by 3-inch valve stations being converted to electronic valves utilizing two pilot solenoid valves to position the valves, an inlet and outlet pressure transmitter and a valve position transmitter, feeding into an electronic valve controller for each valve. These controllers in turn communicate with the city’s SCADA system.
This enables each of the valves to output the pressures (inlet and outlet) and the valve position. From these inputs, along with the valve curves located in the valve controllers, the flow rate through each valve can be calculated and that signal is sent back through SCADA. This allows the city to make adjustments to each valve to stabilize pressures or increase flows where required, which helps balance their network in real time.
The foreman is happy with the installation and is pleased with the fact that he can now track from his phone what every valve is doing along with the relevant data. He says he can balance the systems’ pressures and flows much better than before. He also states this was a great addition to the water system.
Converting an older, manually operated control valve is a relatively simple task, and the benefits to the network can be huge. Having the ability to get real-time information on what is happening in the network helps operations to manage their system more intelligently and allows the control valve to share all the information it uses to control the system with those who can really use the data.