The first bearing isolator of the current design was patented in 1977 and initially used on pumps and mixers in the food processing and chemical industries. Since the 1980s, they have been installed on most anything that rotates. During the last 10 to 15 years, most general-service, frame-mounted and horizontal American National Standards Institute (ANSI) pumps include a set of bearing isolators to protect the bearing housing from the introduction of liquids and debris (contamination ingress). Keeping the lube oil clean greatly improves the life of the bearing and, ultimately, the pump. Bearing isolators/protectors are a marvelous improvement over the previously used devices—lip seals. To a lesser degree, interim devices on higher-energy pumps involved stationary and occasionally rotating labyrinths of both axial and radial designs. Modern bearing isolators consist of a non-contacting unitized rotor and stator combination. Consequently, there should be no wear on the shaft and/or on the isolator itself. The earlier generation of bearing protection (lip seal designs) had a relatively short operational lifespan that was usually measured in months. The edge of the lip seal contacted the rotating shaft, creating permanent damage. Bearing isolators are not just designed to keep the contamination out and away from the oil and the bearings; they are also designed to keep the oil in the bearing housing of the pump. If the isolators (and the pumps) are properly installed, they will often operate more than 10 years with no bearing isolator issues. At some point, the elastomers reach the end of their useful life, which is mostly driven by environmental factors. Given the potential for a bearing isolator with a long lifespan, not all millwrights, operators and mechanics fully understand the limitations and boundaries of the bearing-protection device. Over the last 30 years, I have witnessed frequent errors and a general misunderstanding of the rules and principles for the devices. One of the most common field complaints I hear is that the lube oil is leaking out of the bearing housing. The following general checklist will help users find and troubleshoot potential reasons for oil leakage (oil egress) from the bearing isolator in the field. This checklist does not cover all designs and is based on a typical horizontal ANSI (B73.1) pump design because it is the most common type of pump used in general industry. This discussion is limited to pumps, but isolators/protectors are also commonly used on motors, mixers and other types of rotating equipment. If you have something to add to this checklist, I would appreciate your input.
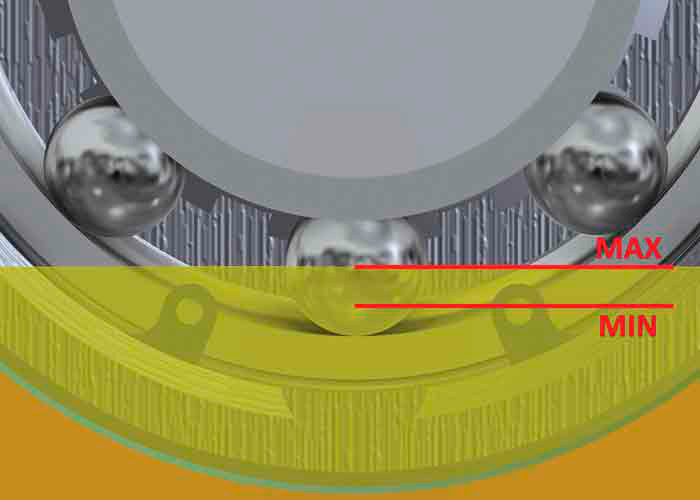
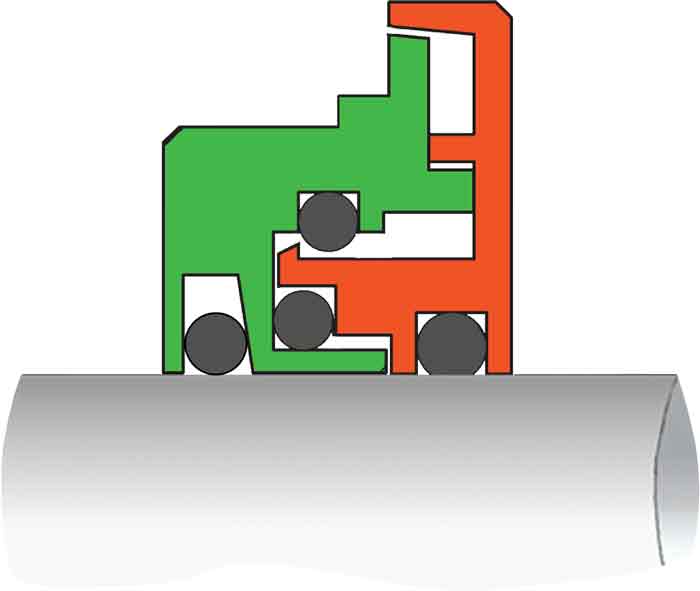