Using chopper pumps and waste from food production, Cannington generates energy to run operations.
11/15/2013
As potato and arable crop farmers who diversified into cold storage, bioenergy and recycling, Mike and Tim Roe’s journey into anaerobic digestion shows what can be achieved by operating the ideal pumps and systems that are matched to the application.
Cannington Enterprises
The father and son—based in Bridgwater, Somerset, U.K.—first ventured into cold storage in 1997, growing their business from around 200 pallets of cheese and fruit juice to more than 3,500 pallets stored per week. This success brought about the need to move to a much larger site in 2003. Currently, the company has in excess of 10,000 tonnes of fruit juice and food ingredients stored at -14 C to ambient temperatures. Not surprisingly, these quantities led to much higher energy bills, and they have been rising steadily every year. “Addressing an annual electricity bill in the region of a quarter of a million pounds became a big priority,” said Tim Roe, managing director at Cannington Enterprises, the parent company of Cannington Cold Stores, Cannington Bio Energy and Cannington Recycling Services.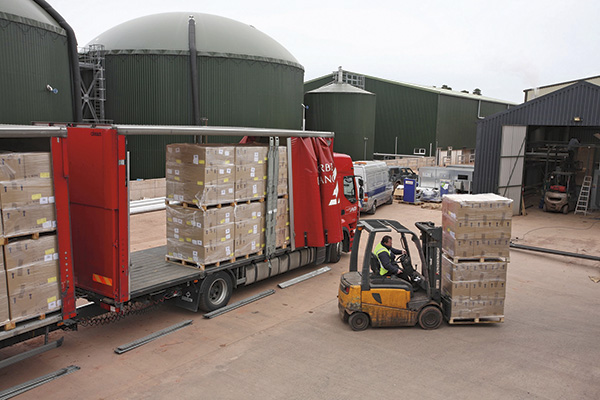
Accelerated Batch Times
Cannington’s AD process was working more than adequately, but in 2011, Tim and Mike Roe decided to change from exclusively corn waste to food waste, which decomposes twice as quickly, to produce the all-important gas much faster. They installed two additional combined heat and power (CHP) engines to boost the AD output to 1.3 megawatts (MW). Currently, the food waste that arrives at Cannington is shredded and de-packaged before liquids are added en route to the reception tank where the mixer first handles the material (17 percent to 20 percent dry matter content).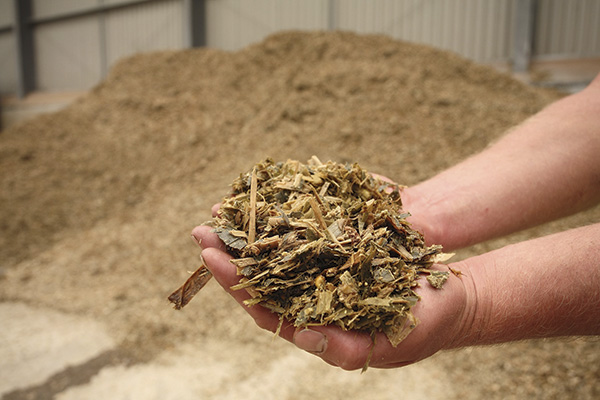
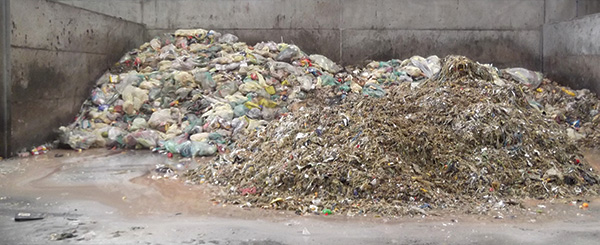
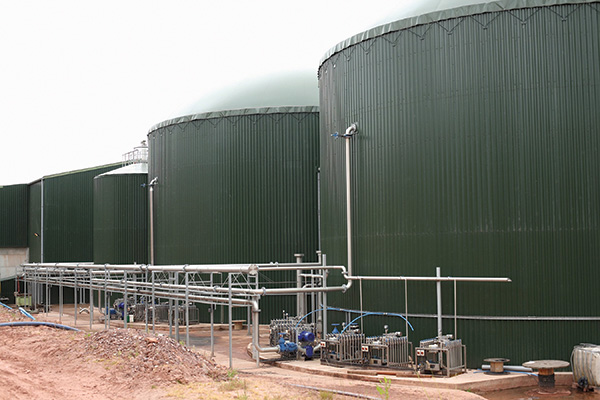