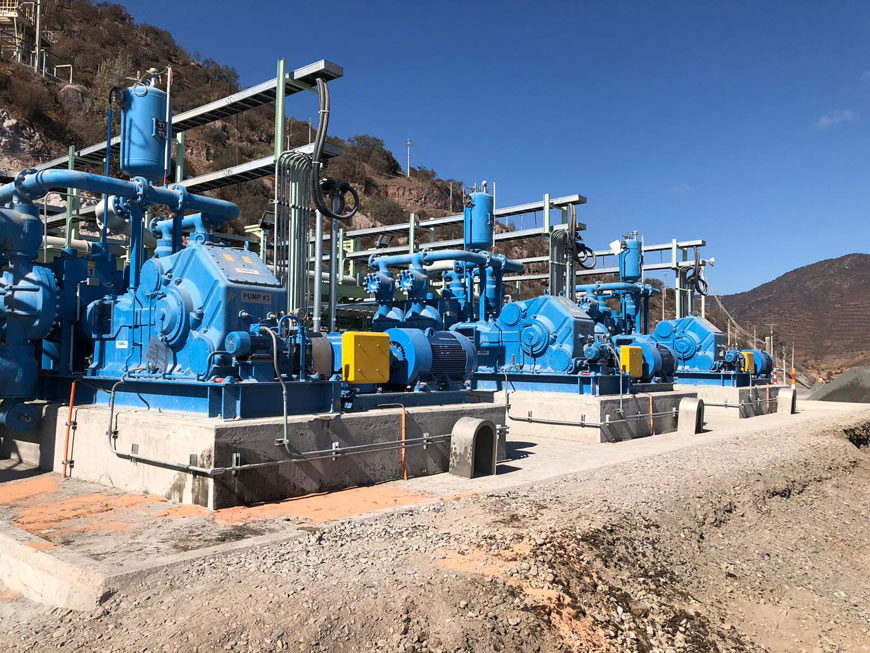
The short definition of dewatering in mining terms is simply removing groundwater for an underground mine or mining pit—anywhere that is below ground level and susceptible to collecting water. The tough part of the equation is how to do it when the liquid is heavy with migrating solids, high pH levels, gases and other contaminants that are contrary to conducive pumping at great depths or distances and sometimes with high temperatures under pressure.
A miner’s worst enemy has always been water where it is not wanted or needed. A mine’s operational plan or design could change in an instant if groundwater intrusion suddenly becomes an issue.
Therein lies the need for a hybrid solution for the typical occasions in a mine when the fluid being pumped is not clean: a piston-actuated diaphragm pump. Whether the separation of this liquid removed is done mechanically through a press or chemically, it still needs to get to ground level to be evacuated and either disposed of or remediated. The workspace needs to be kept dry to access the product to be mined while keeping in mind that pH levels, product temperature, solids content, solids size and overall thickness slurry also involve the system design and pipe layout and sizing.
Removing heavy, hot and reactive slurries from deep in the ground at below-ground levels under pressure requires a pump that is built to last and constructed of compatible materials. If chemical compatibility is considered when sizing the pump, the most optimal outcome ensues.
There is a trend toward the removal of air and gas engine-powered devices in confined areas. The increasing need for environmental responsibility in both the process and equipment will prevail as time goes by for reasons of efficiency and regulation.
When the ability to drop a hose and use a gas-engine driven, end-suction centrifugal pump is not possible, users need an electrically driven, piston-actuated diaphragm pump as a permanent solution. These types of pumps do not have the same portability as kinetic pumps but gain the permanence of scalability, dependability and greater volumetric efficiency—on average, they have 90% overall volumetric efficiency.
Achieving Efficiency Within Budget
Piston-actuated diaphragm pumps used in mine dewatering have the ability to work at high pressures and efficiencies at a constant rate. They are easy to maintain and repair and operate at a slow stroke speed that is conducive to low vibration and parts wear.
Piston-actuated diaphragm pumps do not need a tight tolerance or clearance in the pumping chamber to operate and can pass thick slurries, sometimes as thick as up to 70% solids. Since they move a given amount of fluid or slurry for each pulse of the diaphragm, they can pump repeatable and reliable volumes almost every time. The fluid amount does not fluctuate much during pockets of migrating solids or gassing.
Most piston-actuated diaphragm pumps are run on a variable frequency drive (VFD) and have an adjustable operational range. They have passive pumping ability in which the fluid column passes by the face of the diaphragm and usually does not slam up against it. These types of pumps also require fewer booster pumps or no booster pumps in many mine dewatering operations when properly sized and used.
In today’s climate, finding the correct pumping system to match the application, and last, is critical to achieving a mine’s budget. A piston-actuated diaphragm pump can provide longer, predictable wear with forgiving maintenance algorithms. The most major wear components such as gearboxes and drive pistons usually last the entire life of the pump, therefore consumable, more common wear items become manageable.
Piston-actuated diaphragm pumps can also be forgiving to a mine’s capital expenditure—a well-built piston-actuated pump can last 30 years or so and until it requires replacement. The cost of the pump is known and can be budgeted for as a long-term capital expenditure.