Sealing systems can play a vital role in equipment performance and are considered critical components in the validation process of a design. Engineers should closely examine the sealing systems used in their equipment, because they do everything from preventing seal leakage and extending hydraulic cylinder life to lowering dynamic friction and controlling hydraulic motor position. Component designers must contend with extreme wear conditions and harsh chemicals. In addition, they must meet tight tolerances and factor in significant vibration and high pressures. Many variables can affect sealing capabilities, and their impact can vary greatly depending on the sealing application. Manufacturers and users are often challenged to balance resources properly when addressing what could be substantial sealing issues. Issues with the sealing system can affect performance significantly and may lead to decisions in the validation process that produce erroneous or misleading results or consume excessive resources. So, what are the right methods to properly address the validation of sealing systems?
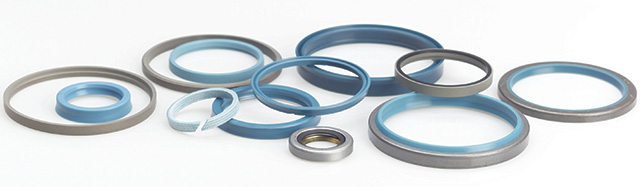
Seal System Verification
Verification and validation of a system design process are independent procedures that are used to ensure that a system meets the intended specifications, requirements and objectives. They provide assurances that reliability and performance will be maintained over the life of the process. Equipment manufacturers want to minimize the cost of validation without jeopardizing any requirements. The validation process delivers a comprehensive understanding of the risks or liability associated with the process and gives insight into many of the influences on the system's performance. Systems validation requires considerable planning. Any mistakes in planning can lead to falsely validating systems. The product could then have to be redeveloped, or it could be launched with poorly understood behavior. For instance, seal leakage can affect cylinder or actuator life, which can be a vital part of operations, controlling valves in every area, and managing the flows of water, gas or chemicals. Another example is sealing system friction, which can affect position control. Since sealing system performance and process performance are directly linked, the validation of sealing system performance plays a crucial role in process validation procedures.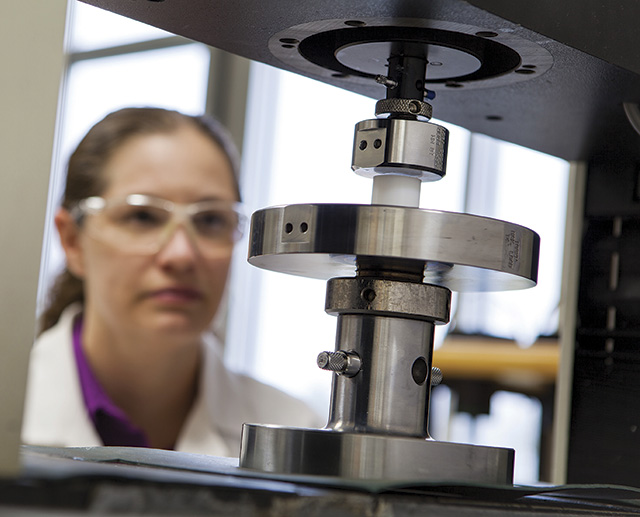