Nitrogen is present in untreated wastewater effluent and can pose major environmental concern in high concentrations, especially when released into bays and watersheds. Nitrogen is an end-product of the bacterial metabolism of ammonia, which can act to deplete dissolved oxygen in receiving waters. Nitrogen also stimulates aquatic plant and algae growth, which causes hypoxia and, additionally, blocks sunlight from reaching submerged marine life, creating a condition known as eutrophication. Also, nitrogen can exhibit toxicity toward some animals and, in general, presents a significant public health hazard. Furthermore, nitrate compounds are another primary contaminant in drinking water that can cause a human health condition known as methemoglobinemia, which alters the oxygen-carrying capacity of hemoglobin. The levels of nitrogen created during the wastewater treatment process must be significantly reduced before the effluent is discharged into the environment. The primary challenge is to develop a practical method that economically reduces the levels of nitrogen in the effluent.
Denitrification Using Methanol
Through denitrification, water treatment facilities convert the excess nitrates into nitrogen gas, which is then vented into the atmosphere. This process helps prevent an algal bloom in watersheds thereby allowing oxygen and sunlight to reach marine life below the surface. Several commonly used methods, most of which use pretreatment basins, aeration tanks and blowers, can accomplish denitrification. For nearly 200 wastewater treatment plants in the U.S., however, the process also involves the addition of methanol into the effluent, which accelerates the activity of anaerobic bacteria that break down harmful nitrate. Methanol is a colorless, volatile, flammable and biodegradable liquid that is readily available in the market. Methanol denitrification related costs are estimated to be about one-eighth the cost of other commonly used methods. In most cases, a metering pump is used to add methanol to the effluent stream. The type of pump can vary but needs to meet certain application requirements, including chemical compatibility of wetted parts and electrical safety ratings for the area where the pump is being installed. Because methanol is an alcohol that is classified as an organic polar solvent, all wetted parts must have a high degree of chemical resistance. Since methanol is both volatile and flammable, the metering pump must meet approvals for use in hazardous locations, especially Class 1 & II services. Diaphragm pumps are often used for metering methanol for wastewater treatment applications. However, when metering in low flow treatment plants, such as small facilities associated with universities, hospitals and rural communities, pump designs that include valves can be difficult to prime and often become air-bound during operation. For these low-flow applications, a technology used for decades in a type of medical instrumentation has proven ideal for ultra-low-volume metering of methanol for denitrification.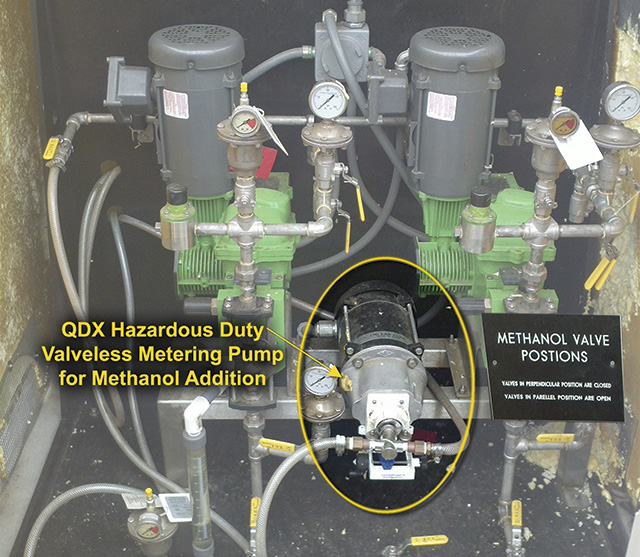
Valveless Piston Pumps
Valveless piston pumps rely on one moving part, a rotating and reciprocation ceramic piston, to accomplish both the pumping and valving functions. With only one moving part in the fluid path, internal check valves, present in diaphragm and other reciprocation pump designs, can be eliminated. The technology is precise and works particularly well in low-flow wastewater treatment operations. The use of sapphire-hard, dimensionally stable, ceramic internal components allows precision manufacturing with tight clearances. The ceramic components for both the piston and mated liner are wear-resistant and chemically inert. As a result, the volume of the pumping chamber remains the same for millions of metered injections. This, as well as the elimination of multiple check valves, provides a metering pump that can self-prime down to the micro-liter range and never lose prime. This is the result of eliminating check valves that don't seal well enough to prevent backflow. When metering methanol in the denitrification process, one valve-less piston pump is driven by a one-third fractional horsepower (HP) hazardous-duty motor rated for Class I, Group C,D; Class II, Group E,F,G. Image 1 shows an installation in a non-heated outdoor enclosure, at a community college wastewater treatment plant.How They Work
The metering pump uses a unique rotating and reciprocating ceramic piston, moving within a precision-mated ceramic liner to accurately pump fluid in one direction without allowing any backflow. The reciprocation action of the piston is similar to that of a standard piston pump. As the piston moves back, it draws fluid into the pump chamber. As it moves forward, it pushes fluid out of the pump. In addition to reciprocating, the piston simultaneously and continuously rotates in one direction. The piston is designed with a flat cut into the end closest to the inlet and outlet port (see Figure 1). As the piston rotates, the flat cut is alternately aligned with the inlet and outlet port, essentially functioning as a valve. At no time are the inlet and outlet ports interconnected, eliminating the need for check valves. One complete synchronous rotation and reciprocation is required for each suction and discharge cycle as shown in Figure 1.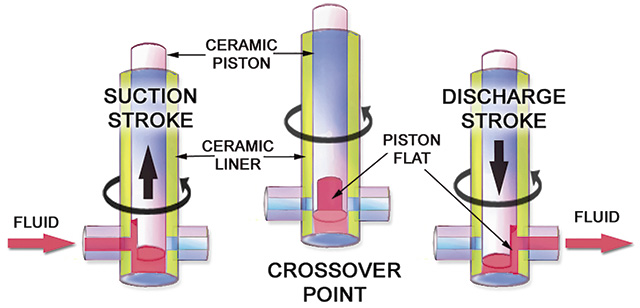
Easy Adjustment
The piston displacement (or volume pumped per stroke) is variable and controlled by the angle of the pump head to the drive. When the pump angle is zero, the pump head is in straight alignment with the drive, and the flow is zero. In this situation, no reciprocation occurs and only the piston is rotating. As the angle of the pump head increases above zero, in either direction with respect to the drive, the piston reciprocates, and fluid is moved through the pump (see Figure 3). The greater the angle, the greater the displacement (piston stroke) per cycle.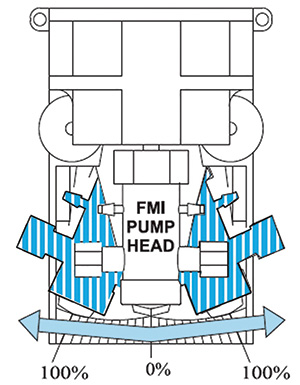
Accuracy & Precision
Monitoring both the accuracy and precision of the dispenses can help end users measure dispensing consistency. Accuracy is a comparison of the average value of the dispense volume compared to the desired or target value. Precision is the range or degree of variation from dispense to dispense. Comprehensive testing has proven that some valveless piston pumps can maintain a precision of 0.5 percent or better for millions of cycles without recalibration (see Figure 2).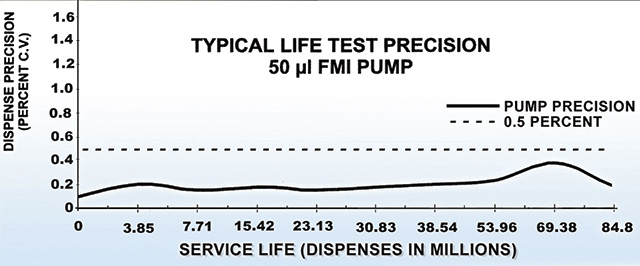