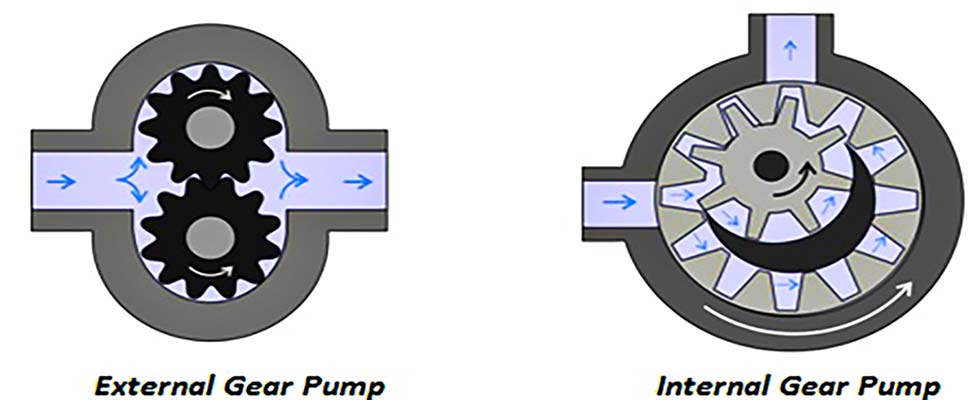
Gear pumps are the most common type of positive displacement pumps, which are often used in pumping relatively high viscous fluid such as hydrocarbons, motor oil, liquid fuels and adhesives. For any rotodynamic pump, as viscosity goes up, pump performance diminishes due to increase in friction. But in the case of gear pumps, the effect is the opposite. An increase in viscosity results in higher volumetric efficiency as viscous liquids fill the clearances of the pump.
External & Internal Gear Pumps
Both internal and external gear pumps have similar pumping principles, but there are some differences in design and construction. Fluid is trapped within the gear pump teeth and pushed to the high-pressure discharge side. The difference in pumping action is briefly explained in Image 1. Internal gear pumps typically have better suction capabilities than external gear designs and are suited to high viscosity fluids, although they have a useful operating range from 1 centipoise (cP) to over 1 million cP.
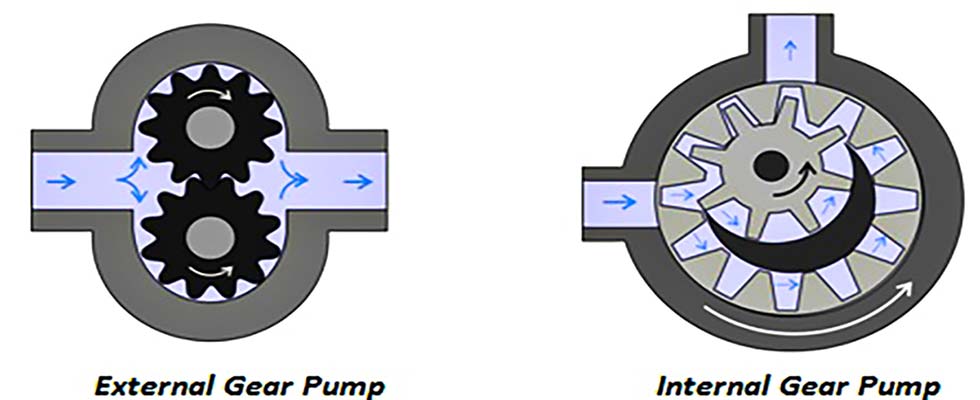
of Titan Manufacturing)
Clearances
As the fluid cannot seep back along the path it moved through, nor between the engaged gear teeth (they create a seal), it must exit through the outlet port. However, some gap/clearance is required between metal parts if they are rubbing against each other. Some fluid will seep through the side clearance of the gears to the casing, the peripheral clearance of the gear and bore in the casing and gear-to-gear clearance.
The degree of slip depends on these clearances, developed pressure and the viscosity of the liquid—the lower the viscosity, the greater the slippage.
This gap must be small, which is typically around 0.0005 inches, in order to maintain the pressure increase across the pump.
There are some essential variables for users to consider for gear pump sizing and selection.
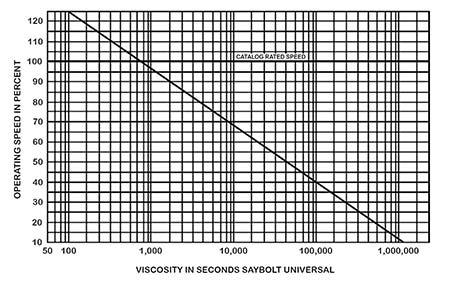
Pressure & Flow Rate
Flow rate is the amount of fluid being moved in unit time and pressure acts as energy to move that fluid against frictional resistance and gravity. Pressure and flow are two of the primary parameters that indicate the right selection of the pump and necessary modifications.
Unlike centrifugal pumps, in gear pumps or any other positive displacement pumps, flow rate is directly proportional to pump speed. Each revolution will deliver a fixed amount of fluid.
Flow rate will show the speed the pumps should be run. Actual flow, however, will be less than theoretical value, as some slippage will occur through the clearances. The volumetric efficiency of the gear pump remains around 80 to 90 percent. That means, 10 to 20 percent of fluid seeps back to the inlet port.
Differential pressure is another key factor for any pump selection procedure. As flow rate remains, the same irrespective of pressure, there is no such thing as shut off head in gear pumps. If the system demands more and more pressure from gear pumps, this will simply add more torque on gear pump components. For this reason, gear pumps are provided with an internal relief valve (and sometimes an external relief valve for a high pressure application) set at maximum desired pressure of the system. It is always recommended that users size the motor horsepower (hp) based on the pressure at which the relief valve is set.
Viscosity
As already noted, gear pumps often are chosen to pump high viscous fluid. It is important to understand what changes are needed to make inside a pump as we go higher in viscosity level.
- Clearances—Viscous fluid between moving parts opposes the relative motion between them. Generally, it is desired to have a small clearance to prevent fluid from seeping back. But as viscosity increases, shear stress (τ) given by Newton’s law of viscosity increases (Equation 1). For high viscosity value (µ), shear stress can be decreased by reducing shear rate or velocity gradient (∂u/∂y). One way to do it is by increasing the clearance. However, there is no direct relation between viscosities and clearance, and it ultimately depends on pump model and size. The end user may consult with the manufacturer for the best clearance for the particular application.
- Pump Speed—The second way to decrease velocity gradient in Equation 1 is by decreasing the pump speed. Higher viscosity liquids require a lower pump speed to allow the liquid to fill the space between the rotating gear teeth. Pump manufacturers have recommended maximum pump speed for various viscosities. Image 2 shows the percentage of rated speed compared to viscosity for internal gear pumps.
- Horsepower & Torque—Besides the power required by the pump to deliver certain flow and speed, there will be additional power required to compensate frictional loss within the pump due to fluid viscosity. For low speed gear pumps, additional power means increase in torque to the rotor and shaft. Sometimes a pump with a cast iron rotor may be prone to gear tooth failure in high viscous application where the pump manufacturer may recommend a pump with a high-strength steel rotor. The recommended viscosity limit with cast iron rotors depends on pump size and model.
Liquid Temperature
Liquid viscosity decreases with an increase in temperature. Liquids are often heated prior to pumping for higher allowable speeds, greater capacities and lower power requirements. Conversely, pumps are often required to handle low temperature liquids, particularly in refrigeration or air conditioning equipment. In either case, special consideration must be given to pump construction at extreme temperature conditions.
High temperature may require special gaskets, packing materials and varying amounts of added clearances applied to the internal parts of the pump to avoid scoring, galling and other mechanical failures.
Materials of Construction
In selecting the materials of construction, factors that must be considered—other than consideration of the liquid itself—are temperature, contamination and concentration of the liquid. The initial cost of materials, replacement costs and longevity of service should also be considered. Standard pump part materials like cast iron, bronze and low-carbon steel are typically less expensive initially. However, these materials can become more expensive if they cause premature failure, unexpected service and replacement. Often, 300 and 400 series stainless steel are popular for corrosion-abrasion conditions. For some low speed gear pumps, higher viscosity may require rotor material to be upgraded from cast iron to steel to resist the increase in torque due to viscosity.