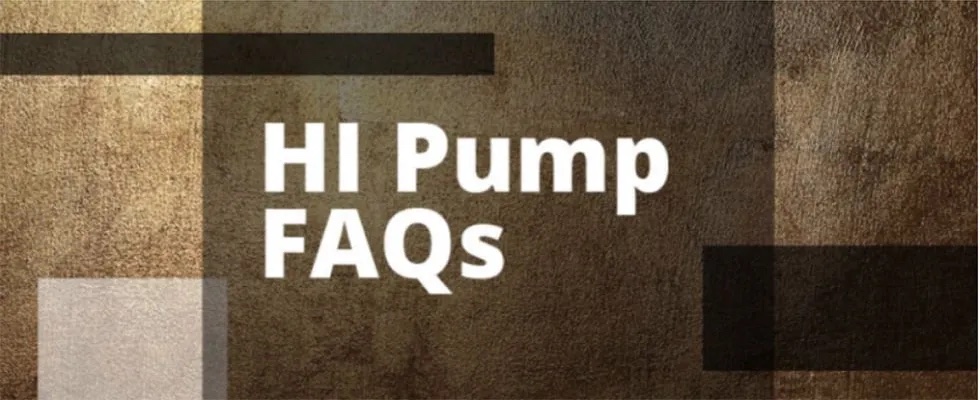
A variable frequency drive (VFD) adjusts the voltage and frequency applied to the motor to adjust its rotational speed and the pump speed. This allows for greater control of the pump performance to meet the system requirements, but a few factors must be kept in mind to ensure reliable operation.
First, one must keep the motor in mind. Peak voltages supplied to the motor terminals will be higher when using a VFD, which will stress the motor insulation system. Therefore, a motor designed for “inverter duty” should be used, and other mitigating accessories can be considered. Refer to NEMA MG-1 Part 31 for a starting point on recommendations for inverter duty motors.
Second, careful attention to the installation of the VFD is required. Minimizing the length of electrical cable, utilizing the proper type of cable (Image 1) and following the recommended grounding is necessary. The environment the VFD is installed in also needs to be considered. Cleanliness, ambient temperature and altitude will all need to be taken into account for proper selection and reliable operation.
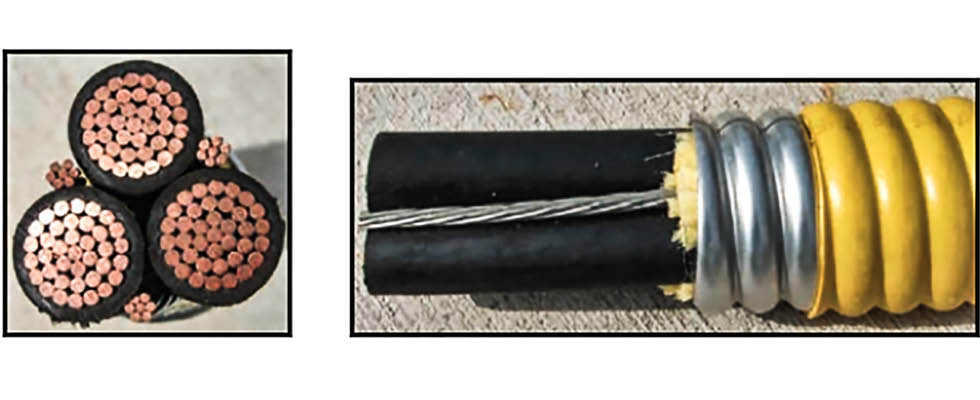
Third, attention to the operating parameters is needed. It is vital to understand the load the VFD is supplying and how the required torque changes as a function of speed. This will affect the VFD selection, settings, starting methods and minimum operating speed. Another operating consideration is the dynamics of the pump structure and rotating assembly. The structure and rotating assembly have natural frequencies, which become more likely to coincide for forced vibrating frequencies when the pump is operated at a range of speeds. Refer to ANSI/HI 9.6.8 for details on evaluating the dynamics of pumping machinery.
For more information on VFDs, refer to HI Guidebook, Variable Frequency Drives: Guidelines for Application, Installation, and Troubleshooting at pumps.org.