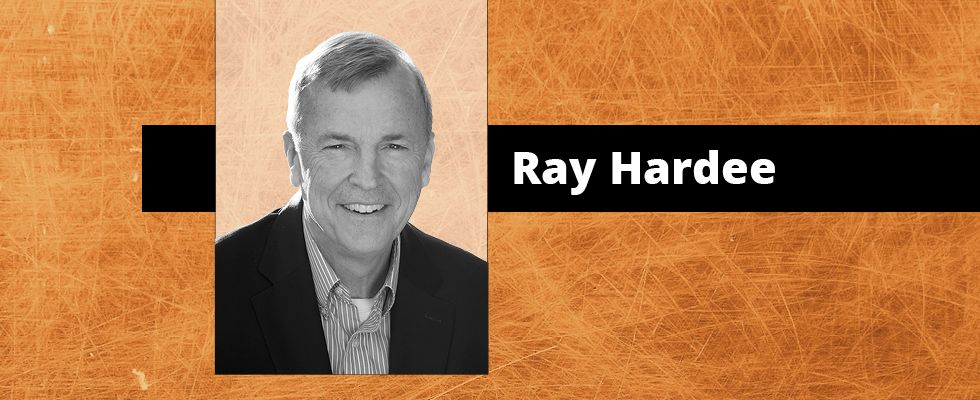
As I was writing this, I searched the internet for digital twin and found over 460 million “hits” about the subject. Topics like Industry 4.0 (over 470 million) and IIoT (over 12 million) are pervasive, too. These articles were full of exciting concepts such as big data, cloud computing, artificial intelligence (AI), machine learning, smart devices, edge technology and even the old standby, paradigm shift.
Each of these terms describe a process that uses new technology to improve and expand on existing processes. For example, in 1982, my first microcomputer, which weighed 21 pounds, had two 90-kilobyte floppy disks to store the program and data, a single eight-bit processor, 64 kilobytes of random-access memory, a keyboard, and 5-inch monitor. The piping program that we developed could calculate the balanced flow rates and pressures in a network of over 500 pipelines and send the results to a printer.
As I write today, this program still calculates the balanced flow rates and pressures within a piping system. But now data can be stored on the cloud, and the application can run on an array of computers with the horsepower to swiftly process data from systems of any size. The calculated results can be displayed on multiple monitors, provide insight to system operation, or input data directly into other mission critical applications.
So, instead of dwelling today on technology features and how they’ll provide a “paradigm shift” into the future, I’ll focus on how new technology enhances the established methods you’re already familiar with.
Limiting the discussion to fluid piping systems, we’ll start with the concept of digital twin and how it offers an accurate simulation of physical piping systems. Then we’ll look at the IIoT—the industrial internet of things—and see how the availability of low-cost instruments can give us better insights into how a system is really operating. Finally, we’ll discuss Industry 4.0 and smart devices, and examine their integrated approach to improving equipment efficiency and their ability to alert you to potential issues that can impact operations.
Digital Twin: Operational Intelligence Across a System’s Life Cycle
A digital twin is more than a software program, a computer-aided design (CAD) drawing or an equipment database. It is a computer simulation of a physical piping system that can be used throughout the life of the facility. Four key elements are:
- A mathematical model describing the system.
- Industry-specific data inserted into the model to describe how the system is built.
- Measured values from plant instrumentation to simulate the system’s operation and validate the calculated results.
- Methods to analyze those results to gain insights into the operation of the physical piping systems.
The mathematical model is the foundation of the digital twin. For piping systems, it is based on a system’s energy balance, which accounts for the change in energy through each item within the system. It takes the fluid energy supplied by the pump elements and balances it with the energy consumed by the process and control elements, and is expressed in Equation 1.
Equation 1
The next step involves entering the data needed to determine how each item uses the energy. The energy transferred is well understood for each item in the system, including the pumps, pipelines, process equipment and controls.
Since the digital twin is a life cycle document, the degree of detail will vary over the project’s life. As the system progresses from the conceptual design to a physical system, more details become available. These details are provided in equipment specifications, manufacturer-supplied test data and the installed plant instrumentation. Once the system is built and the as-built data is entered, the digital twin is ready to simulate how the system will operate.
Once the system is placed into service, it is operated in order to meet market conditions. By specifying the system’s as-operating data and its as-built model, the digital twin can simulate the operation of the total system. The as-operating data can either be manually entered or automatically imported from the facility’s supervisory control and data acquisition (SCADA) system.
Measured operating data from the physical system can validate the accuracy of the digital twin. For example, if the as-measured values of the installed plant instrumentation match the corresponding results of the digital twin, the model is valid and accurate.
The results of the digital twin simulation can provide greater insight into system operation. As I’ve discussed in previous articles, pump cavitation is harmful to both pumps and systems, yet there is no instrument that can directly measure the presence of cavitation.
That can only be done by calculating the net positive suction head available (NPSHa) at the pump suction, and by comparing the results with the pump’s net positive suction head required (NPSHr) from the pump curve. Because the digital twin calculates the NPSHa at the pump suction, and the manufacturer-supplied pump curve specifies the NPSHr for the operating pump, the digital twin automatically checks for the presence of cavitation and provides notification. This is an example of the insight that digital twin technology provides to system operation.
IIoT: New Sources of Raw Data
In the past, plant instrumentation was expensive to purchase, install and maintain. Most plant instrumentation was used to control the process and offer indications on system operation to the plant’s staff.
IIoT technology consists of low-cost instruments for determining pressure, temperature, vibration or flow rates. This, combined with wireless technology to connect the low-cost instrument with the installed SCADA system, makes it much more affordable to measure and record system data. Storing data on the cloud further reduces the cost of the information, but that begs the question, “what do you do with the data?”
Many IIoT articles talk about storing the operating data on the cloud, where machine-learning algorithms use artificial intelligence to provide greater insight for system operation.
Instead of compiling large amounts of data and letting machine learning “discover” the connections, the digital twin can simulate system operation and identify the differences between how the system should be operating and how the system is actually operating.
Using IIoT technology, more system operating parameters can be measured and used to further cross-validate the accuracy of the digital twin.
For example, if each pump used IIoT devices to obtain suction and discharge pressures and the power values from pump motors, these additional as-measured values would be able to provide more data points for this cross-validation.
Industry 4.0: Making Pumps Smarter
Industry 4.0 refers to the fourth phase of the Industrial Revolution and focuses on machine interconnectivity, automation, machine learning and real-time data.
When applied to a specific item of equipment, it is often referred to as a smart device or edge technology.
More pump manufacturers are installing smart pump packages that integrate low-cost sensors, variable speed drives and controllers to process the data locally. The added sensors measure pump suction and discharge pressures, pump vibration and temperatures of the pump seal, bearings and motor.
The addition of variable speed drives (VSDs) provides a measurement of pump power along with the ability to impact the process by controlling the pump head.
Instead of sending all the information to the cloud for further analysis, the smart device processes the measured data on the local controller and is able to give a warning when a pump is operating outside the control parameters. Since these calculations occur on a device outside the SCADA system, smart pumps can be considered edge technology.
So, how does the smart pump controller provide operational insight?
It is another example of a digital twin being used to simulate the performance of a physical pump.
The mathematical model is based on the energy balance in the pump; specifically, how electrical energy supplied to the pump drive is converted to fluid energy leaving the pump discharge nozzle. The data describing pump operation is found on the manufacturer’s pump curve. Some of the installed instruments give the digital twin the as-operating data it needs to simulate pump performance; others provide the as-measured values needed to validate the accuracy of the digital twin.
Insights from smart pumps can detect many things, such as dry running, operating below a minimum flow, pumping against a closed discharge valve and high temperature and pressure conditions, when the pump is not operating efficiently. They enable you to control the process by adjusting pump speed.
As always, smart devices can still send the operating data and the results to the cloud where machine learning algorithms using AI can provide additional insight about the operation of the piping system.
New Technologies Improve Sound Engineering Practices
The digital twin, IIoT and Industry 4.0 have been getting plenty of press in technical publications. Each of these technologies is based on well-established processes, and their greatest value is the speed and accuracy of doing tasks that were manually performed in the past. For example, I remember from my student days when my fluid dynamics class discussed how to calculate pressure drop in a pipeline.
The first step was understanding the mathematical model describing the pressure drop calculation. Then we had a homework assignment where we used the mathematical model, along with pipe and fluid data, to calculate the pressure drop for a given flow rate. Then we were off to the fluids lab to measure the flow rate through the pipe along with inlet and outlet pressures. We compared the as-measured values from the lab to the calculated results of our homework, and used the results to learn about the effects of flow rate on pressure drop. The entire experience took three classes, one four-hour lab, and hours of hand calculations for a single pipeline.
As you can see, we were using the foundational elements of the digital twin way back in 1969, before it was cool. Using today’s technology, the same process can occur on systems with hundreds of pipelines, equipped with SCADA data to determine if the results of the digital twin match the measured values.
The results provide insights for all areas of fluid piping systems.
In other words, it’s not just new technology that provides insight; you need a clear understanding of what’s occurring, and why, to meet your goals.
To read more Pump System Improvement columns, click here.