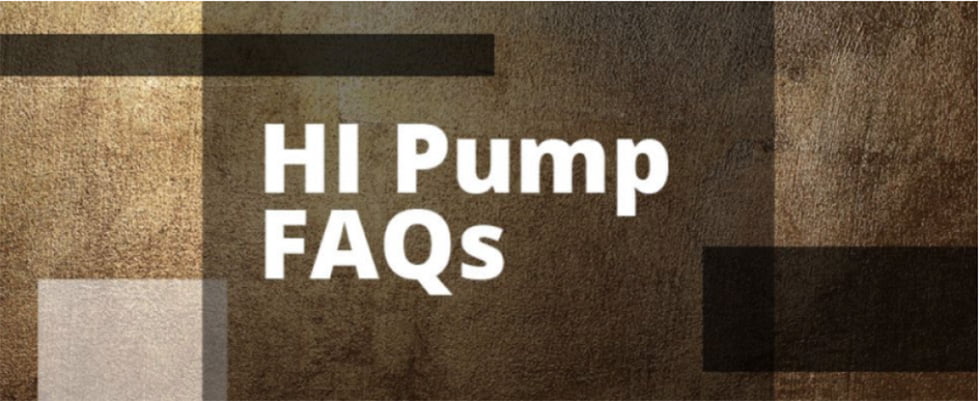
What Impeller Balance Grade Should be Used to Limit Pump Vibration?
High levels of residual unbalance in rotating parts can generate high unbalance forces resulting in excessive bearing and shaft loading and inducing high levels of vibration.
Pump impellers are typically balanced in accordance with International Organization for Standardization (ISO) 1940 balance quality grade G6.3 or better. (ISO 1940 for values relating to other balance grades). It is important to note that the G6.3 is a generality. Some equipment may run at higher speeds and require a better balance grade to meet vibration standards, and other equipment may be lower speed and built robustly for a heavy-duty service.
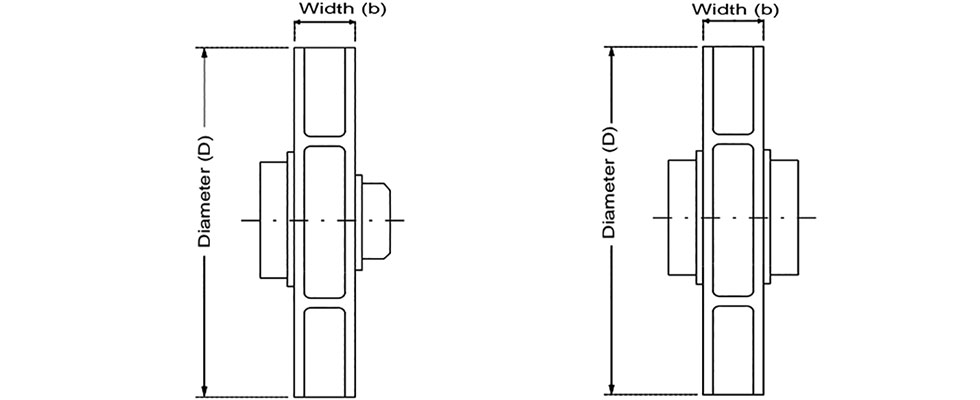
of Hydraulic Institute)
For example, slurry pump impellers will have wear during operation that will change the balance; therefore, slurry pumps are designed to operate with a large amount of unbalance in the impeller. For the balance of slurry pump type impellers, refer to the latest edition of American National Standards Institute/Hydraulic Institute (ANSI/HI) 12.1-12.6.
Another important factor to consider is single-plane versus two-plane balance. Depending on component geometry, it may be satisfactory to perform a single-plane spin balance. Components are typically single-plane balanced if the ratio of diameter to width (D/b) is 6.0 or greater (Image 1). Two-plane (or dynamic) balancing is typically performed otherwise.
Unbalance is only one of the causes of rotating equipment vibration but is arguably the most prevalent. Therefore, it makes sense to pay attention to balance of the rotating elements to limit the vibration; however, a pump with the most precise balance can still exhibit excessive vibration due to operating away from the design point, misalignment, resonance or poor installation.
For more information on impeller balance and pump vibration, refer to “ANSI/HI 9.6.4 Rotodynamic Pumps for Vibration Measurement and Allowable Values” at www.pumps.org.