Read Part 1 here. Most pump bearings fail long before their design life span. The American Petroleum Institute (API) typically requires a minimum bearing life (L10) of 25,000 hours, and ANSI B73.1 specification for horizontal ANSI pumps specifies a minimum L10 bearing life of 17,000 hours at maximum load and rated speed. Prudent end users frequently request bearings with more than 40,000 hoursL10, but most bearings do not reach that many hours of operation before failure. More than half of pump bearings fail as a result of contamination, excess heat or both. Preventing this introduction of contaminates is easier and less expensive than removing them. Some studies suggest removing contaminates can be eight to 10 times more expensive than prevention.
Oil Contamination
This premature failure rate is typically the result of contamination of the oil not a fault of the bearing or pump manufacturer. Dirt, wear particles and other foreign debris as well as improper bearing installation procedures can contribute to contamination that leads to reduced bearing life. Other forms of contamination include heat and air in the form of air entrainment and aeration. Increased levels of heat and air lead to increased oxidation rates. One of the most common sources of contamination, however, is water, which is often introduced because of improper storage and handling. During pump operation, water can leak into the bearing housing from external sources such as area wash down, spray from failed mechanical seals (or packing) or leaks from equipment near or above the pump. Another common method of water introduction is condensation through machine aspiration (moisture laden air is drawn in due to pressure differentials). For example, a pump running steady state at a given temperature above ambient for five days is shut down on Friday at 4 p.m. As the pump cools, the ambient air is drawn into the bearing housing where it cools and the moisture condenses, releasing the entrained water into the housing where it mixes with the oil. According to sources at the SKF Bearing Company, 250 parts per million (PPM) water in the lube oil will reduce bearing life by a factor of four, and another source states that 0.002 percent water in the oil will reduce the bearing life by 48 percent. According to other sources, the reduction of oil contamination levels from the ISO 21/18 to the ISO 14/11 will increase bearing life by a factor of 7.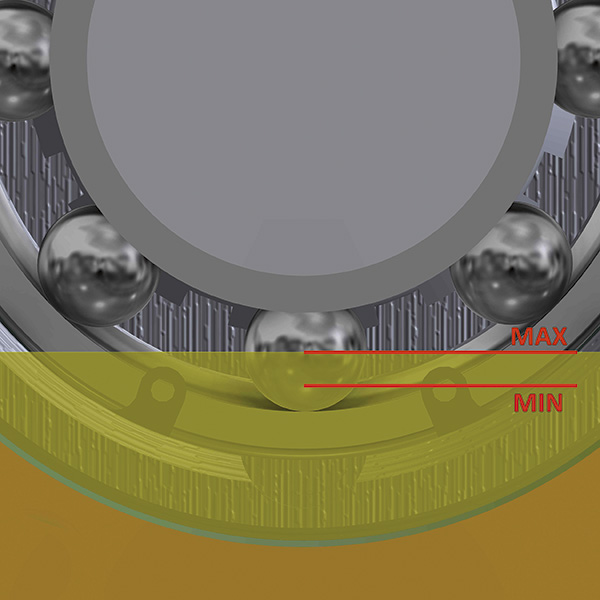
Bearing Lubrication Methods
Selection of a bearing design for a specific service will, to a large degree, determine how it is lubricated. Depending on the pump speed, type of service, horsepower (HP) range and size, different types of bearings are available. A properly selected oil-lubricated ball or roller bearing will work for most applications less than 200 HP, 400 F (fluid temperature) and 3,600 revolutions per minute (rpm). For some smaller and lower temperature applications (less than 320 F), grease-lubricated bearings may also work well. Larger pumps at higher speeds and system temperatures will require line, sleeve or plain journal bearings for radial support (hydrodynamic journal bearings) and tilted shoe (pad) designs for thrust bearings. Methods and designs that are acceptable for ANSI specification pumps may not be acceptable for API, process, marine and power generation applications where HP can often exceed 70,000 brake horsepower (BHP) with speeds in excess of 6,000 rpm. Because most end users at the high end of the HP and speed spectrum are aware of oil types, best practice lubrication techniques and bearing selection, this article will examine the middle and lower range. Oil splash lubrication may be the most common method of bearing lubrication for horizontal pumps from 5 to 250 BHP. The oil is contained in a sump in the housing with the bearings. The machine is designed so the oil level for proper operation is at the middle of the bottom ball in the bearings.Oil Levels
Oil levels higher than the middle of the lowest ball bearing will have negative consequences and increase oil temperature and air entrainment. Both of these factors accelerate the oil's oxidation rate and reduce oil and bearing life. For splash lubrication, the oil level should touch the very bottom of the bottom ball in the bearing. If the oil drops below the ball or the outer race, the bearings could be damaged. If the level is too low, the bearing could experience temperature runaway, which is when the bearing gets hot quickly and is permanently damaged. Variations on splash lubrication design include flingers, discs, oil rings and several other methods/types of lubrication. One note of caution is that rings must be close to perfectly concentric, and the pump shaft must be level for the rings to work correctly. I have rarely seen the ring remain round, especially after the first maintenance overhaul. If not initially leveled, the pump may not remain level either. Problems may also arise if the design ratio of ring to shaft diameters is not correct. Critical speed can also be an issue. While the rotor may be above the first critical speed, the oil ring speed is typically at 50 percent of the shaft speed and may be rotating close to critical frequency. Other types of lubrication include grease (with ball bearing variations of shielded/unshielded and sealed), oil mist, oil purge and forced oil feed (oil is pumped to the bearings for the larger HP pumps and some marine applications). Most motor bearings are grease-lubricated, so it is important to know if they are open, shielded, sealed or a combination of these options. If they are shielded on one side, the best practice is to place the shielded side toward the grease fitting. I have seen many end users who order pumps with greased bearings still add oil to the housing simply because the installation, operation and maintenance manual (IOM) did not specifically say not to. Running the pump with greased bearings and splash oil lube at the same time is an incorrect solution.Oil Changes
The first oil change should be conducted at a shorter interval than subsequent changes to eliminate the contamination that occurs from startup and run-in operations. Most ANSI and some API pump manufacturers will state that the first change should come at 200 operating hours and subsequent changes at 2,000 hours or 3 months, whichever comes first. The intervals depend on operating temperatures and how contamination ingress is managed. Some operations will require more frequent oil changes, and others can operate for several years. Oil sample analysis and experience will aid in decisions regarding oil change intervals. Consider how often oil is changed in a car. If a car was driven at 60 miles per hour for 24 hours a day and 7 days a week for one year (8,760 hours in a year), it would drive 525,600 miles. You would never drive a car that many miles without changing the oil.Automatic Oilers
Several automatic oiler types and brands are on the market. The question to ask is whether the oiler is vented to atmosphere or to the housing. Old designs vented to atmosphere, but that is how moisture gets to the bearing housing and oil. The new best practices are to vent the oiler to the housing and keep the housing sealed. The old method was to also vent the housing, but that was a source of contamination. The vents should be eliminated or, at the very least, used with a desiccant breather or an equalizer expansion chamber.Lip Seals Versus Bearing Isolators
For more than a hundred years, lip seals have served the industry well. While they are simple and inexpensive, end users should consider replacing them with the more modern and efficient bearing isolators. Lip seals, regardless of the manufacturer, will, at best, only last about 3,000 hours in service. After approximately four months of operation, they will fail and potentially allow water or other contaminants to enter the bearing housing. The advent of the bearing isolator is what has allowed many pump manufacturers to extend their warranties from one to five years. The modern bearing isolator will, on average, last eight to 10 years and, if properly managed, even longer. During that time, the isolator will not wear/score a groove on the shaft and, for the most part, will prevent the introduction of contamination to the bearing housing at both operating and static conditions. Bearing isolators can be of the labyrinth or contacting face design, and there are numerous designs and manufacturers.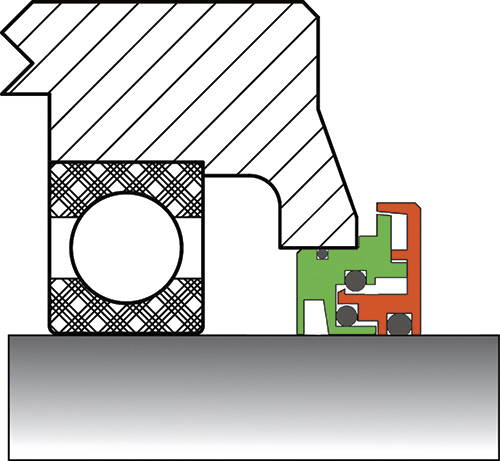