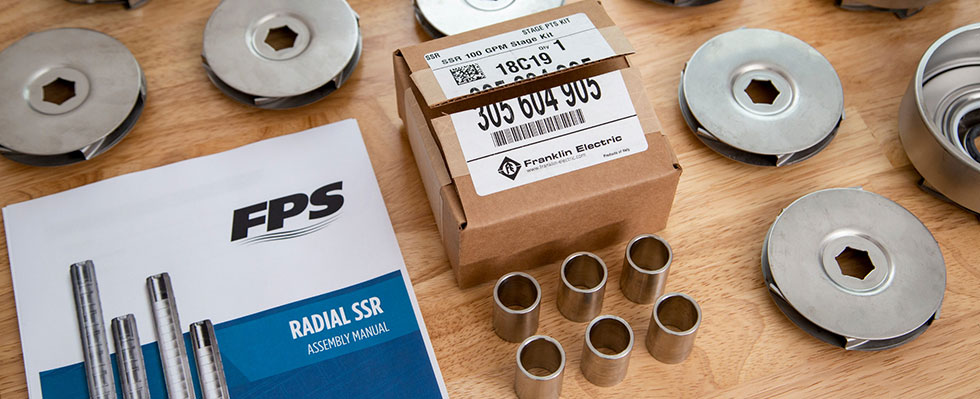
Nothing strikes fear in the hearts of a pump system owner quite like the thought of an unexpected shutdown and for good reason. Downtime is lost revenue. If a system is not up and running, it is not producing, the team is idle and it is losing time and progress. Pump failures can cause a snowball of issues for an operation, and determining the root cause of the problem becomes mission-critical.
There is never an opportune time for a part to fail, but there are steps to make the repair process easier and faster. Consider these tips to help plan ahead. With a little work now, end users can recover from system emergencies and unexpected shutdowns faster—and possibly avoid failures in the future.
Tip: Know the name and contact info for your local pump distributor and service center.
When a problem arises, who is going to solve it? Does the team have the knowledge, tools and resources available to perform a repair, or will outside expert help be needed? Knowing whom to call ahead of time can help bring in a service team faster. In addition to a primary contact, it is recommended to also have a backup in case workload requires it. It is also a good idea to have the contact information for a local build center in case the pump needs off-site work. If unsure of how to find this type of resource, reach out to a pump manufacturer. Larger manufacturers have distribution and partner networks that they can refer users to. Some also offer repair services and in-stock spare parts.
Tip: Know your pumping system’s model andserial numbers.
Knowing whom to call is only a small part of the battle. Knowing what to call about is even more important. When the pumping system’s critical information is readily available, five phone calls can be turned into one, with service coming faster. In addition, having this documentation at hand will mean not having to search for it in an emergency, like when a sump pump is clogged and overflowing.
Be sure to document:
- manufacturer name
- system size and type
- model number
- serial number
- horsepower
- amperage
- intake and discharge pipe sizes
Record all this data in a centralized area so it can be easily found and referred to. Include the technical support hotline information for the manufacturer as well; this can help not only with on-site troubleshooting, but also help locate a service center if needed. Also, include any information on part numbers that have been ordered in the past. Consider documenting part numbers for system-critical components, like the impeller. Some manufacturers will package this information in a parts breakdown, detailing the component part numbers of a standard pump package. Reach out to the manufacturer to see if they have an equivalent option available.
Tip: Try to always choose and source OEM-approvedreplacement parts.
The equipment’s performance is only as strong as the weakest link. OEM replacement parts are designed, manufactured and produced right alongside the same parts that went into the original equipment. This means the tolerances are tighter for production and the quality control is more stringent. If the local supply store cannot source an OEM part, contact the pump manufacturer. They will connect with a distribution partner nearby or ship it directly. The best pump manufacturers will also have dedicated technical support hotlines with trained team members that can help troubleshoot issues over the phone.
Tip: Diagnose the cause of the failure to make sure it does not happen again.
Pump systems are designed to be workhorses, but all pumps are intended for different applications.
Some things to consider when diagnosing unexpected system failures are: Is the pump sized and scaled correctly for the job it is running? Is it running at higher operating parameters than expected? Is there a pump designed for a residential application trying to tackle commercial duty requirements?
All these factors will affect the overall performance and longevity of the pump system.
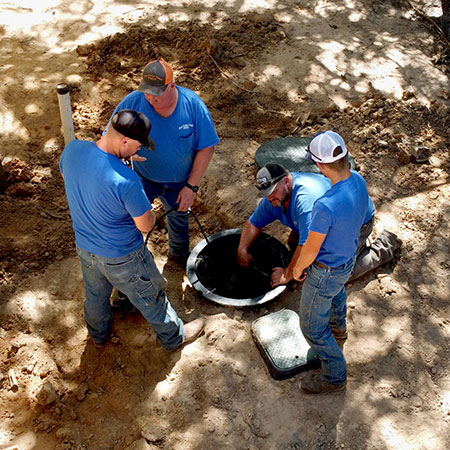
Also know that some failures can occur for uncommon reasons even a pump manufacturer or seasoned repair professional cannot predict. Consider the case of the muskrat that decided to build a home near an intake pipe. The pump pulled in the critter’s lodge.
The pipe clogged as a result, stumping the maintenance crew that tried troubleshooting mechanical parts and found nothing within the pump that needed replacing. Once they investigated further, they found the culprit. The pipe was cleared of the vegetation, and the crew fitted a protective screen to the intake valve to prevent this from reoccurring.
Tip: Consider your maintenance schedule.
Just like changing the oil in a car and replacing brake pads on a regular basis, pumping systems require some routine service as well. Product manuals outline ideal maintenance schedules based on the run hours of the system. Equipment manufacturers also recommend routine maintenance if your equipment is exposed to extreme temperature swings or is placed in storage for extended periods of time. These guidelines can include suggestions for which additional parts need to be replaced when performing routine maintenance jobs, such as O-rings and gasket kits. Know the pump’s recommended maintenance schedule, and plan for a service outage when it is convenient, rather than being forced to maintain the system when it is needed most. During scheduled maintenance, inspect the equipment thoroughly to look for any other potential issues. This can help offset the stress of an emergency shutdown.
In fact, the best plan for handling an emergency is to avoid it in the first place. With a little advance planning and preparation, users can not only reduce critical shutdowns, but also recover from them faster.