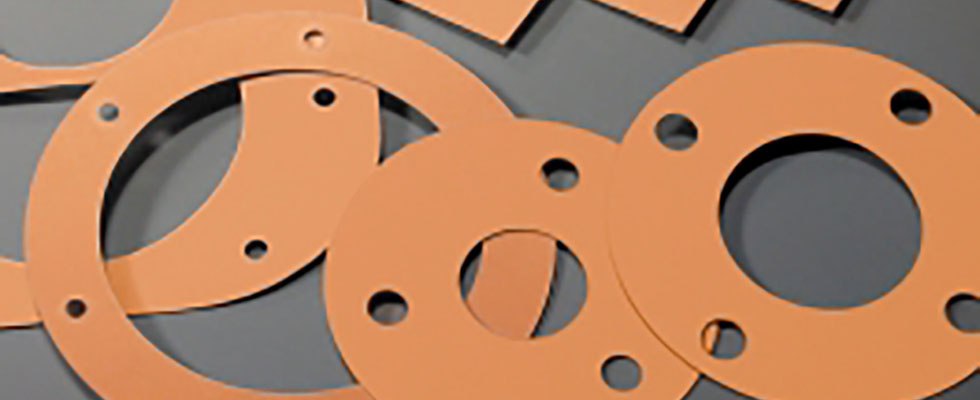
There has been a lot of recent attention paid globally to a general class of fluorinated chemicals called perfluoroalkyl substances (PFAS). PFAS are materials that have a carbon-fluorine based structure—a definition that covers thousands of different chemicals.
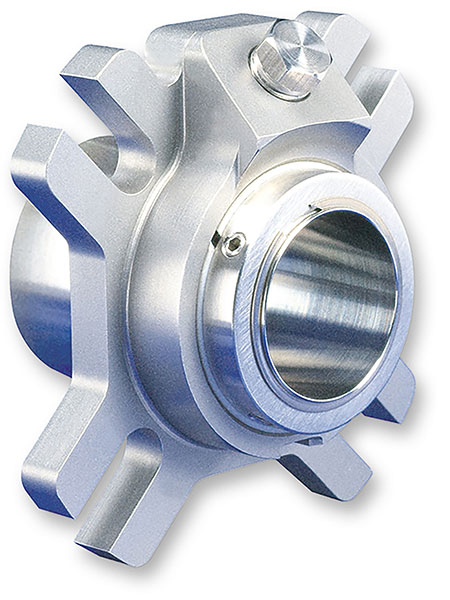
Two of these PFAS chemicals, perfluorooctanoic acid (PFOA) and perfluorooctanesulfonic (PFOS), have been identified by the United States Environmental Protection Agency (EPA) and other regulatory bodies as potentially harmful chemicals that have been found in drinking water supplies.
Other chemicals that fall under the broad definition of PFAS are often erroneously considered dangerous by association with those two chemicals. To the contrary, quite a number of these other PFAS are considered safe and non-hazardous, and they are irreplaceable in a wide range of industrial applications, such as power generation, oil and gas production, chemical production, mining and water systems, as well as uses in many other sectors, such as medicine, aerospace and semiconductors.
Some legislators and advocates have proposed banning all PFAS outright, which would unnecessarily create a myriad of new problems (what do you replace these materials with?) while trying to solve the issue currently focused on a small number of chemicals of concern this massive group of chemicals. This would be a regrettable example of throwing the baby out with the bathwater.
As the trade association representing a majority of fluid sealing device manufacturers in the Americas, the Fluid Sealing Association and its partners at the European Sealing Association work to educate all interested parties on the function and proper use of sealing devices worldwide.
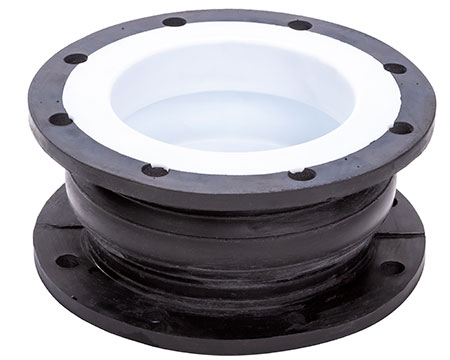
One recent area of the Fluid Sealing Association’s focus has been on PFAS as it relates to one of the world’s most effective, high-performance sealing materials: polytetrafluoroethylene (PTFE). Because it has a carbon-fluorine bond, this material is by definition also considered a PFAS material; however, it is a completely inert and safe material.
What Is PTFE & Why Is It Useful?
The turn of the last century saw many new developments of man-made compounds like fluoropolymers by applying recent discoveries in quantum mechanics, chemistry and physics. Scientists were trying to create new materials that could be stronger, inert, thermally and physically stable and nonreactive with other materials. These materials would allow longer life of everyday products without breaking down over time from corrosion and chemical attack.
Some of this innovation began with Linus Pauling, who won the Nobel Prize in Chemistry in 1954 and the Nobel Peace Prize in 1962. He created many firsts in science, including his work in 1932 with electronegativity that established a scale on the bond strengths of elements.
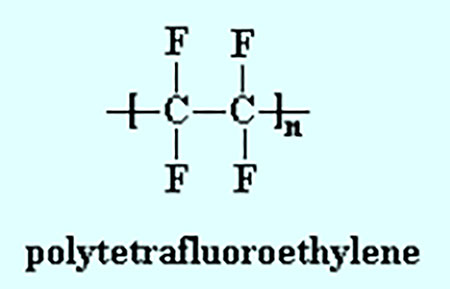
In that work, it was first noted that fluorine has one of the highest bond strengths compared to all elements, and scientists worked to create materials using this discovery that would withstand harsh environments.
PTFE (Image 3) is a fluoropolymer and molecular chain of many carbon and fluorine atoms. It was first used during World War II as a sealing device in equipment used to transport uranium hexafluoride. This super material was critical to the development of nuclear fusion and was described as having
“hearts of diamonds and skins of rhinoceros hides” by Dr. Joseph H. Simons, who developed the electrochemical fluorination process used to make PTFE while at Penn State University.
This incredible material proved to be resistant to attack from many chemicals, was thermally stable, had one of the lowest coefficients of friction of solid man-made materials and showed excellent resistance to natural enzymatic degradation. For these reasons, PTFE continues to be a supreme and irreplaceable material in numerous industries.
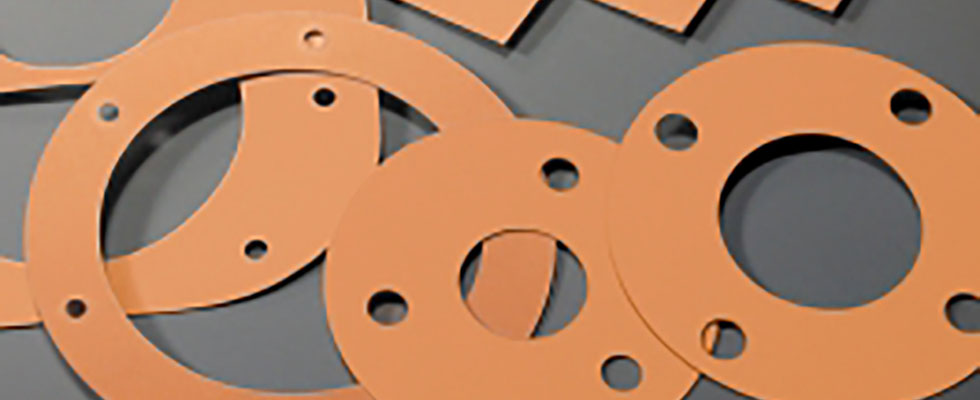
As a sealing material, PTFE has properties unlike any other. It is used in a wide variety of sealing devices, such as gaskets (Image 4) used to seal flanged piping systems, compression packing (Image 5) used to seal valves and various kinds of expansion joints used in piping systems. Mechanical seals used in pumps, agitators and mixers use PTFE gaskets as well as fluoroelastomer O-rings. PTFE is unaffected by almost all chemicals, which means it can be applied across a wide range of applications safely.
This chemical resistance decreases the risk of improper material selection in dangerous media, thus minimizing risk of exposure to plant personnel. PTFE can also handle a wide range of temperatures (typically up to 500 F or 260 C), and as a result, it is useful in numerous industrial applications. Because of its low coefficient of friction, PTFE helps to minimize power consumption in rotating equipment and yields efficiency and operability of control systems in industrial systems.
PTFE is also the best performing material in applications where low emissions of volatile organic compounds are required by law. PTFE sealing devices are used in applications in food preparation, pharmaceutical and potable water applications and it has been one of the only materials deemed safe and effective for many critical applications. In many cases, there are no alternative materials available with the same capabilities.
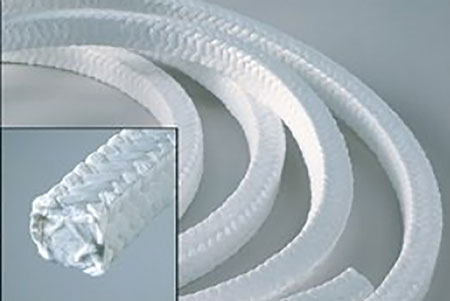
The indispensable uses of PTFE should not be caught up in the net of regulatory activity focused on PFOA and PFOS. PTFE is not PFOA or PFOS. Years ago, PFOA was used as an aid in the production of PTFE, but it is not an intentionally used or added material in PTFE manufactured in the U.S. today. In 2006, the EPA created a stewardship program to work with the eight major companies in the PFAS industry to reduce PFOA from facility emissions and product content by 95% no later than 2010 and to eliminate PFOA from emissions and product content no later than 2015.
All eight companies met that goal, developing and using newer technologies to replace it. Per the EPA “the manufacture and import of PFOA has also been phased out in the United States as part of the PFOA Stewardship program.”1
As mentioned above, there are thousands of chemicals that fall under the general definition of PFAS. The exact number is somewhat difficult to pin down as the definition for PFAS differs, depending on the language used by the user. The number varies between 4,700 to 10,000 or more chemicals. Treating thousands of PFAS chemicals the same when they have a wide array of uses and properties does not make sense. Lumping inert and safe materials like PTFE with chemicals of concern like PFOA is too general an approach. A more logical approach is to focus on classifications of chemicals.
PTFE and related fluoropolymers and fluoroelastomers should not be considered in the same classification as PFAS of concern, like PFOA. All PFAS are different and care needs to be taken not to use terms like PFAS, PFOA and PTFE interchangeably.
PTFE remains an indispensable and safe compound in all facets of modern society. The Fluid Sealing Association agrees with the use of a science-based approach to regulating potentially harmful chemicals, such as PFOA and PFOS. Legislators and regulators should avoid overbroad decisions about the large PFAS family of chemicals and focus on chemicals of concern based on science.
Our Association is in favor of a carve out for PTFE for industry use, similar to language for using PTFE in medical usage, to help ensure that important sectors—medical, aerospace, energy, telecommunications and infrastructure—that use PTFE products are not impacted unnecessarily. As just one example, the loss of PTFE in sealing systems would result in reduced worker safety, energy efficiencies and manufacturing output. Let us keep the baby and throw out the bathwater.
References
Fact Sheet: 2010/2015 PFOA Stewardship Program | US EPA