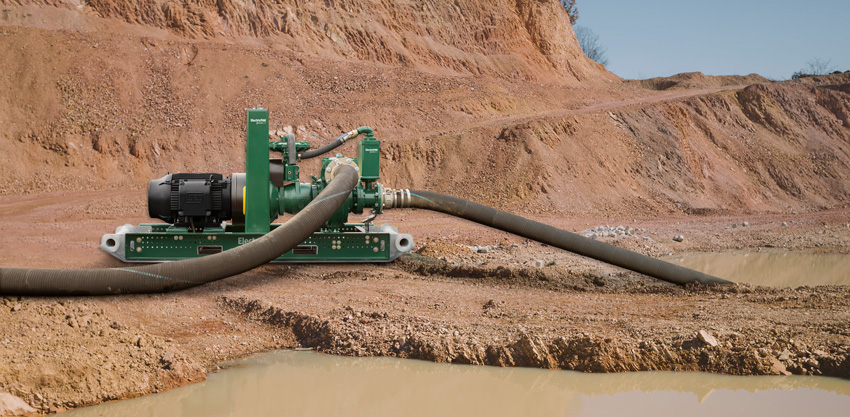
Pump packages that are used for dewatering and bypass purposes often take a beating, from operation to transportation to a jobsite in the first place. At a time when labor costs are on the rise and raw materials are scarce, durability and low maintenance operation have never been more important. Just as important is ensuring the pumps and motors operate at optimum efficiency. These factors have raised concerns over pump vibration and the resulting problems it can cause.
Mitigating vibration often comes down to ensuring a pump and motor assembly are properly aligned, and many times this process can be overlooked or not performed. Anyone who has completed an alignment on a pump and electric motor assembly knows the process can be tedious. It requires precision and an experienced service professional to get the units realigned properly. This process must be repeated any time the pump is moved to a new location or shows signs of vibration. Because the process is so labor intensive, it sometimes does not happen or is not done properly. This can lead to other long-term, vibration-related maintenance issues, including seal failures, unexpected power losses and—in worst-case scenario situations—a broken shaft. These issues can also cause pump users to completely rule out using an electric-driven pump since they assume the cost and efficiency savings will not offset alignment issues.
However, there is a solution: using a bracket that rigidly connects the pump and motor together. This bracket, also known as a motor stool, is engineered to precise tolerances to ensure that the coupling remains permanently aligned and protected. It eliminates any concerns with shifting during transport or operation, saving countless hours of service time. If this method of assembly sounds familiar, it is because it takes its inspiration from a typical diesel coupling with a bell housing that is bolted to an engine. However, in the case of an electric pump package, users benefit from the energy efficiency that electric motors offer without sacrificing performance, power or alignment.
Benefits of Electric Pump Packages With Rigid Motor Stool Design
Experience easier setup after transport
A pump and motor system is typically large, heavy and bulky, weighing in at several tons. For their initial placement, they may be shipped hundreds of miles, encountering bumps, stops and turns along the way. Once they arrive, they are usually unloaded by a forklift, jostled around and set on-site. From there, they might be moved as mobile dewatering needs change within an area. If the unit is used as a rental asset, it will be moved back to a storage facility only to be moved again to its next job.
One example of this is a temporary municipal application, like a sewer bypass. In addition to the initial transport to the site, additional issues may occur: the ground may not be level, a suction pipe may not be fully supported and the pumps frequently cavitate.
In each of these situations, and after any transport, the pump and motor must be realigned. This alignment requires exacting laser measurements that are not only time-consuming but also expensive. With a rigid motor stool design, the need for realignment can be eliminated.
A motor stool setup ensures alignment and smooth running, and a robust, modular design focused on portable rugged use is a good choice for users who need strong equipment operating quickly. Pumps can be fully operational in hours, not days after transport.
In fixed installations, the system designer may determine that grouting is not required due to the rigid alignment, opting instead to just secure the package to a rigid slab with anchors. This also saves time during the installation process.
Eliminate vibration issues caused from skipping alignment
Because alignment is time-consuming and costly, it may not be performed. In dewatering and bypass applications, time is always valuable. For example, municipal applications are often rental units, which means they are regularly transported in a fleet. Municipal installations in most cases have urgent pumping needs, and there is typically no time to spare to perform on-site alignment once the unit arrives. The extra step of realigning a pump package after transport can be eliminated if the pump remains rigidly aligned.
When an alignment is not performed or is done too quickly, the misalignment will lead to vibration issues. In time, this vibration can result in seal failures, oil leaks, shortened bearing life and more. In extreme situations, this vibration can cause the coupling to fail and the shaft to break.
Consistent vibration also leads to pumps that need to be rebuilt. Again, with a rigid motor stool design, vibration is not a concern because misalignments will never be an issue.
Extend pump life
Even permanently installed pump and motor packages that never move can suffer from misalignment over time. Despite their bulk, electric pump packages can be sensitive to movement. Nonzero nozzle loads are unavoidable, and misalignment and the resulting vibration concerns can occur as a result of nozzle loads. Misalignment can also happen when regular maintenance is performed on a pump or motor. A motor stool protects against misalignment that may occur during the life of a pump.
Mining applications provide good examples of these vibration and maintenance concerns in action. Mines are often hazardous environments, and pump packages are usually at risk of being hit by trucks and other pieces of equipment. A rigid motor stool can eliminate alignment concerns that result from everyday use of the unit or the environment it is operating in.
Mining pump packages are also frequently moved around the jobsite and have pipe and hose exerting loads on the pump and base. This makes a strong
pump/motor connection more important since the resulting vibration can cause misalignment.
Save time
Systems that feature a rigid bracket assembly are designed to be modular, which can help users get an electric pump package on-site for operation quickly and efficiently. The modular design is built using interchangeable parts, delivering upfront time savings for the system designer as well.
Custom-built units can take longer to engineer and often require specialized parts. A modular design makes the sizing and quoting process fast and the use of standard parts drives down lead time. These pump packages also offer streamlined maintenance since the modular design can be disassembled quickly, helping to reduce operating costs over the life of the system.
When thinking about these benefits, it is important to remember that often facilities and users may operate more than one pumping system. Worrying about alignment for a single unit is a big enough concern; consider those alignment needs across three, six or more units and the benefits of permanent alignment multiply.
Whether for mining, municipal bypass or another application entirely, alignment matters. Electric-driven pump packages that feature a rigid motor stool design can reduce time-consuming alignment work, saving owners and operators on initial setup costs as well as maintenance costs down the road.