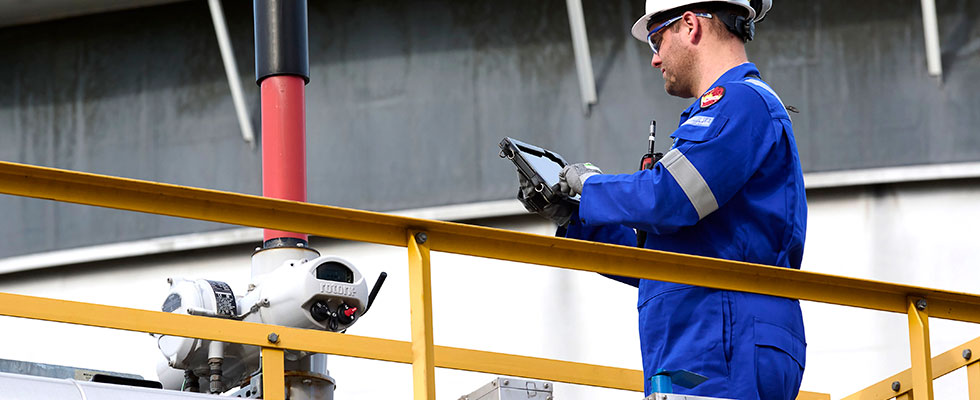
Flow control actuators automate the process of opening and closing valves. They are used in a variety of applications in the industries of oil and gas, water and power, chemical processes and industrial markets. Even on long-running sites, innovative flow control equipment continues to give operators access to cutting-edge technologies.
Actuators are vital assets to flow control operations, and if not kept in the best condition, any failures can have dramatic repercussions for the site. Keeping a site maintained should be a priority for any operation, but devising a comprehensive plan can be a complex and difficult task.
If an asset fails, then not only is downtime dramatically increased, but the safety of the site is also at risk. To avoid these possibilities, it is vital a holistic maintenance plan is implemented that is both flexible and comprehensive.
The Value of a Multitiered Plan
An effective and comprehensive site service program is critical for managing possible issues flow control products may encounter. The program needs to be affordable, accessible and pliable enough to accommodate a variety of enterprises. A multitiered reliability service has the advantage of offering increasingly better coverage and assistance by being split into three sections: basic, standard and premium. These programs’ customizable nature boosts the availability and dependability of assets, while also lowering potential downtime. Having the option for additional upgrades to suit the demands of the user is also an advantage. Adaptability is the best way to maintain consistent enhancement to a site’s functionality.
In such a maintenance program, the importance of taking an asset’s whole life cycle into account cannot be overemphasized. The risks posed by unsupported equipment might be substantial; however, by using specialized service and maintenance programs, operators may manage potential obsolescence in addition to the critical task of ensuring a site operates at optimum efficiency.
The failure of assets as a result of poor maintenance can lead to reduced performance, drops in quality and productivity and loss of investment, as well as severe environmental consequences. It is the responsibility of a site operator to ensure their operation is running as effectively as possible to avoid failing or underperforming equipment. If this equipment fails completely, the results can be disastrous.
Using Intelligent Asset Management to Keep Things Flowing
A crucial element of asset operations is intelligent asset management, which enables a company’s coordinated activity to correlate information and use that data to better understand and predict what maintenance is needed.
Intelligent electric actuators have several benefits, but what is key to a maintenance plan is that it can capture historical performance data for input into an asset management system.
Intelligent asset management, when integrated with a functional service plan, can help reduce operating costs, making budgets simpler to manage and allowing assets to work for longer, thus minimizing environmental impacts associated with premature asset disposal.
A program that uses intelligent asset management, which is a component of the industrial internet of things (IIoT), enables operators to access the data logs stored in intelligent actuators and take appropriate action to increase performance and uptime and avert the aforementioned type of damage. The IIoT consists of electronics that link to other equipment and share data with it. This includes machinery for intelligent flow control. To track, gather, share and analyze data, operational technology and information technology are combined.
Systems that are cloud-based can be invaluable to an intelligent asset program, as they make the process of sharing and storing data easier and are more intuitive, as the information can be accessed by a web platform.
Ultimately, the proliferation of data and data analysis IIoT provides enables plants to have greater efficiency and dependability in their operations. Proactive analysis of data that allows for informed maintenance decisions can mean significant savings in downtime and cost.
Data loggers built into intelligent electric actuators can save information, including the number of alerts, alarm frequency and torque profiles for individual valves. An actuator’s health may be determined by looking at its torque average, deviation, peak levels and opening/closing torque.
A possible issue may be indicated by sudden changes. A comprehensive asset management system that examines this data helps operators run equipment or a site as efficiently as possible, increasing productivity and lowering operational risk.
For any maintenance plan to be truly effective, the needs of the user must be considered. Customized spare programs,
site inspections and maintenance alternatives should all be a part of maintenance programs. In such a program, the importance of taking an asset’s whole life cycle into account cannot be overemphasized. The risks posed by out-of-date equipment might be substantial; however, by using specialized service and maintenance programs, operators may manage potential obsolescence in addition to the critical task of ensuring a site operates at optimum efficiency with little to no unplanned downtime.
When the asset’s whole life cycle is considered, a system is future-proofed. It decreases the risk of failure, removes the need to modify existing connections or control systems, and increases the ability to continue running. More users than ever have access to cutting-edge flow control solutions, and by taking advantage of the right plan, they can increase the profits, uptime and safety of their sites, while simultaneously reducing costs and their environmental impact.