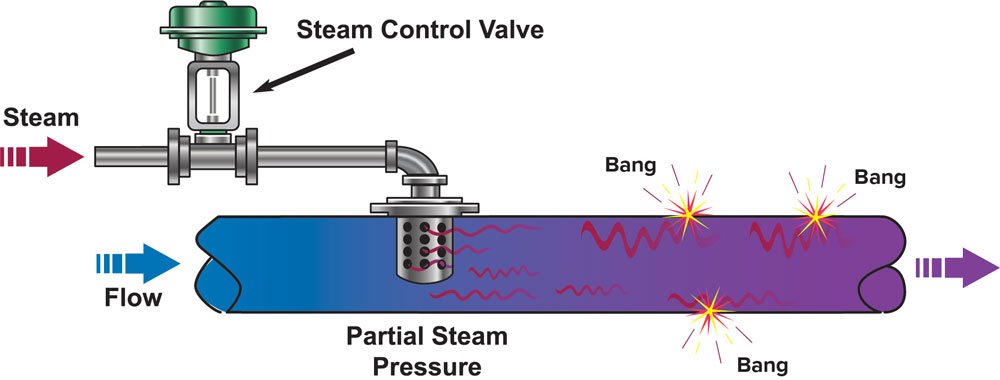
Experiencing intense equipment shaking or the sound of banging and rattling pipes can be steam hammer. Loud noises are commonplace in production facilities but steam hammer does not need to be.
Steam hammer in fluid handling and heating systems occurs in various patterns, all fundamentally related to the rapid condensation of steam from its vapor phase back into the liquid phase. The effects of steam hammer within a system are usually seen as rattling or banging noises with pressure spikes and vibration. These conditions can have adverse effects on process piping, tanks and other fluid system components, including pressure gauges, flow meters and valves. Therefore, this phenomenon can be a concern for personnel safety and equipment maintenance.
Understanding Steam Hammer
The phenomenon of steam hammer generally occurs when there is direct contact of steam vapor with a liquid at its subcooled state. This is typically seen in applications where steam is directly sparged into a tank or injected into a process pipe.
When a form of direct contact steam injection, such as direct sparging or valve controlled steam modulation, is used to heat a given process fluid within a pipe, steam vapor interacts with the process fluid and condensation occurs at the phase interface. This initially results in a two-phase or bi-phase flow. As the two-phase flow moves through the pipe, a stratified layer is formed between the vapor and liquid boundaries. As steam condensation progresses, the stratified flow boundary creates a wave flow pattern. Finally, with the condensation of steam adding to the liquid level inside the pipe, the wave formation reaches a point where it is high enough to isolate the steam vapor section from the liquid section. This results in the formation of steam bubbles within the isolated steam section.
Following the formation of a steam bubble (a single steam bubble considered for explanation), rapid condensation occurs within the bubble. Steam takes up about 1,600 times the volume of its equivalent mass of water. This results in the formation of a low-pressure zone due to a differential in density. The liquid from both upstream and downstream locations is accelerated toward the collapsing bubble to fill this low-pressure cavity within the pipe. The inertia forces generated through this process induce high acceleration forces in the water, resulting in excessive pressure spikes. These pressure spikes cause banging noises and damage process line components and fluid handling equipment upstream and downstream of the steam injection point.
As these bubbles grow in size and collapse, a low-pressure region is created, resulting in accelerated water movement. This mechanism taking place at the inner surface of the tank results in failures over time. Steam hammer within tanks can lead to cracks, leaks and deformation of the tank walls. Steam hammering raises safety concerns if the tank or pipes fail and increases the likelihood of increased maintenance costs.
In addition to maintenance and safety issues, the sparging process’s variability causes problems related to temperature control. When steam is directly injected into a tank containing a liquid, there is a nonuniform distribution of energy within the bulk volume. Due to the absence of turbulence or the required mixing velocity, steam vapor starts forming bubbles resulting from uneven condensation. The uncontrolled nature of the condensing inside of the tank results in temperature variation, typically causing overheating. This variation can harm processes involving temperature-sensitive materials or methods that require temperature control.
Eliminating Steam Hammer
Steam hammer can be caused by externally modulated heating technologies such as heat exchangers or other forms of direct steam injection (DSI), such as spargers. Spargers are standard heating systems in tank heating that rely on the facility’s steam supply or boiler. A standard sparging nozzle consists of several holes that allow steam to enter the process fluid and heat it to the desired temperature. This action may lead to steam hammer or unit vibration as the steam from the sparger mixes with the process fluid in the tank or piping.
Over time, if steam hammer is unchecked, it is dangerous and can be an expensive maintenance problem. The effects of steam hammer can be reduced and possibly eliminated by achieving rapid and uniform steam condensation into the liquid being heated. The required turbulence to condense steam and uniform dissipation of energy can be achieved using internally modulated DSI heaters that use the principle of choked flow.
Unlike sparging, internally modulated heaters use a single nozzle that focuses the incoming steam and accelerates it to a high velocity (usually sonic velocity) before it comes into contact with the process fluid. This high velocity helps atomize the steam bubbles and shear the incoming process fluid, which allows for a more complete, efficient heat transfer—almost eliminating steam hammering in the unit.
Eliminating the problems associated with sparging will directly reduce the cost of heating and maintaining temperature in the tank. Internally modulated heaters use all available energy in the steam and transfer this energy rapidly and stably. This efficiency reduces the energy and time required to heat the tank and eliminates hammering problems.
Internally Modulated Sonic Velocity Steam Injection
DSI heaters designed to internally modulate the mass flow rate of steam at the injection point use the principle of choked flow. A nozzle or a diffuser is generally used to modulate the steam flow and inject it at sonic velocity.
.jpg)
Choked flow can be defined as a fluid dynamic condition. A compressible fluid at a given pressure and temperature passes through a restriction (nozzle or a vena contracta) into a lower pressure region by increasing velocity. The increase in velocity occurs with the mass flow being unchanged, following conservation of mass. Therefore, the generation of choked flow can be identified as the operating point at which the ratio of the downstream pressure to the upstream pressure falls below the critical pressure ratio limit. Also, while the choked flow condition is achieved, a change in the downstream pressure will not affect the flow velocity as long as the pressure ratio is within the recommended critical pressure ratio limit.
As for DSI, a sonic velocity for steam injection can be achieved across a flow restriction such as a nozzle or an orifice when the absolute pressure ratio between the process pressure (liquid) and the steam pressure is below 0.575—i.e., downstream absolute pressure is 57.5% of the upstream absolute pressure.
Using sonic velocity for steam injection uniformly disperses the steam into the process liquid, thereby achieving a consistent temperature profile. In addition, natural turbulence is introduced within the controlled volume. Due to the sonic velocity, the steam jet also requires mixing velocity to condense the steam vapor into the liquid instantaneously. This rapid condensation of the steam helps eliminate problems such as two-phase flow and the formation of bubbles. Internally modulated DSI heaters thus achieve complete condensation of steam and uniform dissipation of the energy before the liquid exits the discharge of the heater.
An internal modulation heater can be installed inline or around a tank to prevent the possibility of having live uncondensed steam within the given system. As mentioned earlier, the use of a single nozzle in these heaters focuses the incoming steam and accelerates it to a high velocity before contacting the process fluid. This high velocity helps to atomize the steam bubbles and shear the incoming process fluid, which allows for a more complete, efficient heat transfer. The result is no steam hammer, precise/uniform heating and reduced maintenance.