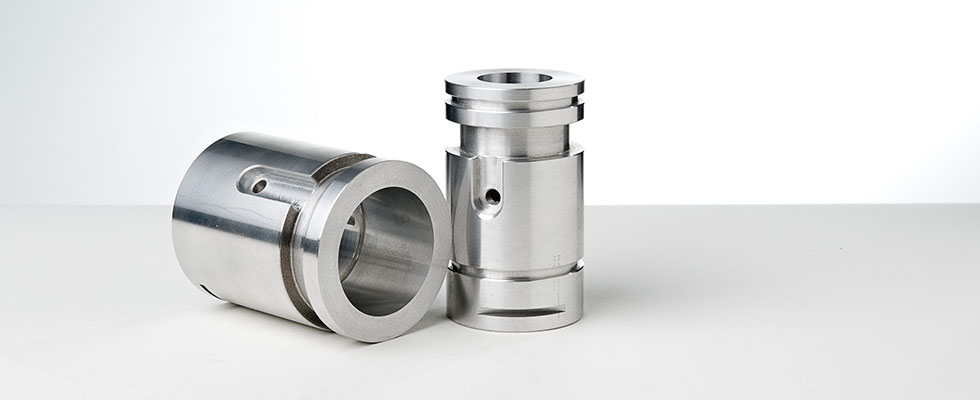
The last several years have introduced global challenges to many facets of life. One of the most impacted areas has been the manufacturing supply chain. Many OEMs have taken a globalized approach to sourcing materials and components for their products. When the COVID-19 pandemic lockdowns struck, many manufacturers did not have the supplies to produce products for end users.
This led to the return of localized sourcing for those same materials and components and the need for companies to bring outsourced components in-house. While some of the world has returned to normal, the global supply chain has yet to recover, and companies across the United States have found the best alleviation to the strains of a slowed supply chain is to source repairs and parts locally. Often, parts can be manufactured to the same specifications or better with a local supplier. It gives better proximity for communication, adjustments and deliveries.
Industrial OEMs & Repair Shops Suffer Supply Chain Challenges
Before the pandemic, distributors in the industrial market had reached a point at which products were available in a few days. This ability to obtain almost anything on a short timeline had given end users the ability to find lower-cost options, to the point where distributors were at record high inventory turns. In many cases, manufacturers were looking at direct-to-consumer models due to distributors having such a low cost of ownership of their products. When things move through distribution quickly, it increases the cash flow and reduces risk.
During the pandemic, it was almost impossible to find products that were needed. There were huge reductions in manufacturers being able to keep up with high and low-volume products, which pushed the focus to higher-volume production and more profitable items. Even with this, many manufacturers were focused on keeping their end users satisfied, which exponentially reduced the aftermarket inventory availability. While some markets are coming back, others are still reeling from pandemic and global supply chain issues.
The inability to get parts from aftermarket sources or OEMs puts tremendous strain on the operational side of organizations. The parts needed to assemble or repair equipment have gone from a lead time of days to months. This leaves projects either incomplete or a in a state of partial assembly. With parts causing delays, what work can get done, must be done, even if only partially. This keeps employees working on billable projects and prevents them from exhausting vacation or not getting paid due to lack of consistent work, further impacting companies’ overall profitability. The lack of parts can cause duress as fast as a lack of general work. Partially completed work also comes with its pain points, such as time to gather and put away tools for repeated setup/breakdowns that would not normally happen. To combat this, organizations have shied away from the globalization of manufactured parts and returned to a more localized approach. Some turn to their in-house teams to begin manufacturing the items they need to complete the project, while others turn to local companies to support their needs. Raw materials are more easily acquired than the finished product and timelines from local businesses should be faster than bringing a part in from a globalized source.
Aftermarket Repair Parts for Alleviating Supply Chain Delays
Companies that have historically focused on low volume or custom repair/replacement parts have seen an increase from existing users, but also an increase in demand from new users needing sources to support their needs. Distribution has gone from having an efficient supply chain process with plenty of sources and short delivery times to having to find new suppliers and options to fulfill end user needs. This has, in many cases, reshored opportunities for manufacturing that have typically been outsourced. Ironically, the price gap that once validated that decision is not as big as it once was. With global inflation on materials, goods, fuels, etc., and the inability to ship products quickly, local manufacturing has been able to compete in markets that once were dominated by offshore competitors.
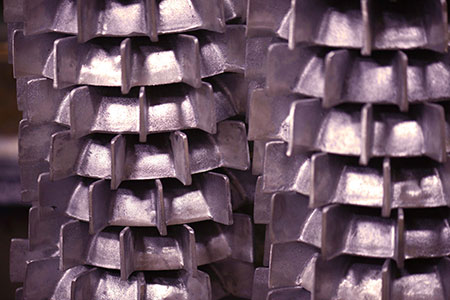
The ability to reverse engineer the components needed is invaluable. Often, the parts needed can be accurately measured and replicated locally. Computer-aided design (CAD) software enables precision measurements to be turned into a working print for local manufacturers or in-house employees to remanufacture the items needed.
Most aftermarket companies are skilled in recreating parts from samples or prints. Often, the complete part is not even needed. Aftermarket manufacturers and repair facilities that specialize in specific industries may already have the data to produce the parts needed. Facilities that specialize in repair and remanufacturing likely have a library of legacy components to help get what is needed, even if that includes a customization to a standard off-the-shelf part.
3D Imaging to Recreate Patterns
In the past, distributors looking for obsolete or hard-to-find replacement parts struggled to find something that would work for end users. If they did find something, the quality or fit was typically not great. With today’s technology, custom parts can have the fit and finish similar to, or in some cases even better than, the original OEM part. Technology can be thanked for this ability to replicate parts in such an accurate way. 3D imaging, from multi-axis arm scanning to laser image scanning, has allowed custom part remanufacturers to measure parts and transfer them to CAD software. This has allowed distributors to gain access to the custom, remanufactured, obsolete and hard-to-find parts that were previously difficult to obtain.
The arrival of 3D imaging and printing has changed manufacturing. Complex designs can be created within a digital space in CAD software and proofed for functionality before manufacturing. The software can also take 3D images and use them for computer numerical control (CNC) programming. This leaves the employee to fine-tune and adjust parameters while the bulk of the programming is complete. This saves manufacturing time and shortens end user delivery times. Once the operator has tuned the program, the CNC machine replicates the part and has it ready to go for foundry or finish production. 3D printing allows for prototyping at a lower price point. The printer can be configured to produce a basic rendition of the components needed for a fully detailed model.
Jobs Are Created & Maintained
Supply chain capabilities have advanced substantially over the past 10 years, but the pandemic has shown no matter how sophisticated and efficient they are, there are always risks to sourcing from offshore options. While there may be some cost advantages, the speed at which distributors can get products locally, as well as communicate with those suppliers quickly, can make a big difference. Increasing dependence on American-made products brings back skilled labor and the emphasis on skilled labor in schools.
As more products are sourced locally, a larger workforce is required. More skilled tradespeople are entering the market than has been seen in decades. Jobs are being added daily at companies that need to increase throughput. The skilled trade sector is booming with growth. This increase in capacity means the woes of a pandemic-era lead time are dwindling to previous levels.