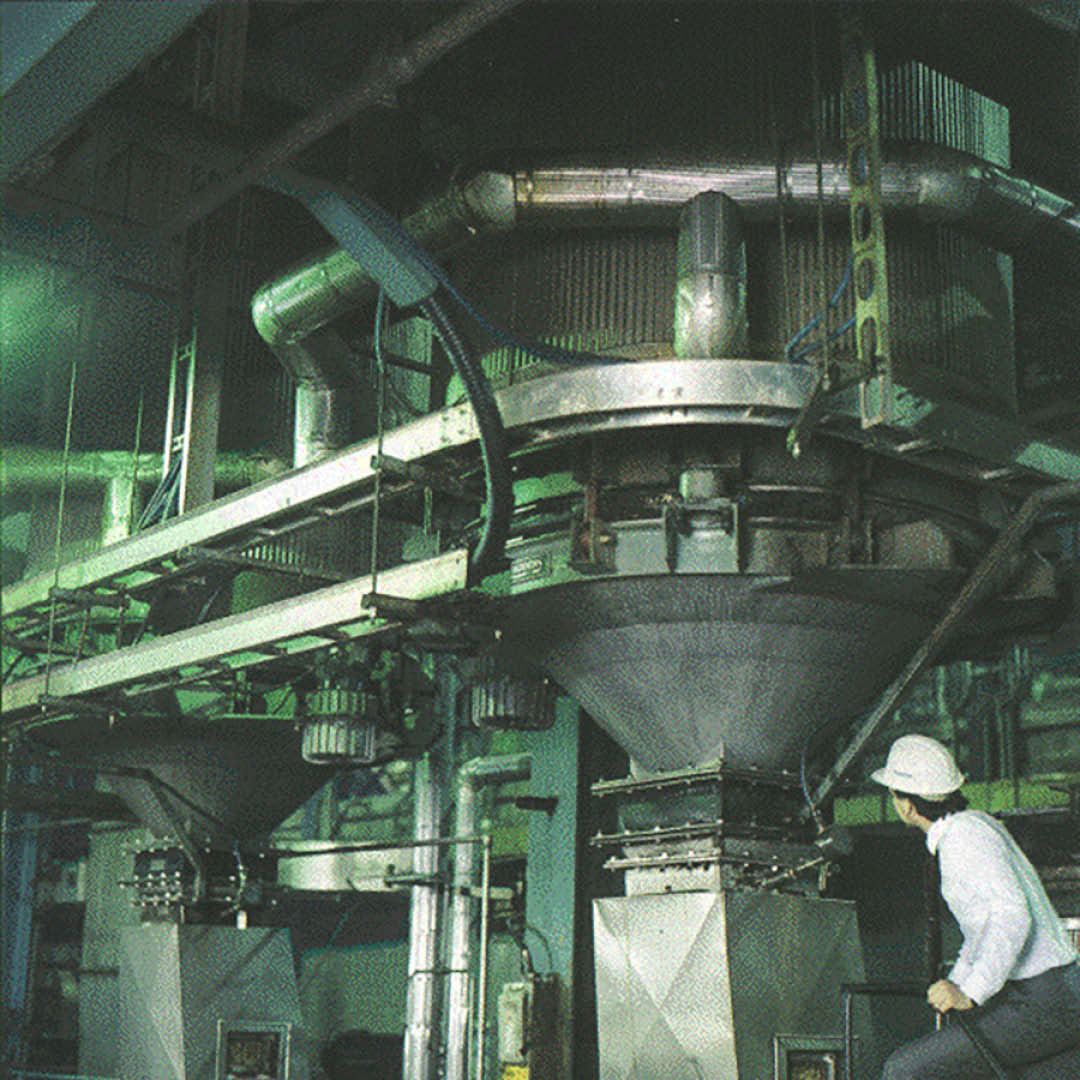
The pulp and paper industry provides products—such as paper stationery, cups, tissues and paper-based packaging, including cardboard—that are integral to modern life. The process of manufacturing paper products requires the movement of wood particles, chemicals and water through networks of piping to be processed. Rubber expansion joints mitigate pipe stress resulting from thermal fluctuations and vibrations from pumps or other specialty machines found in this industry.
Piping systems facilitate the constant movement of wood, pulp, chemicals and a constant circulation of water throughout the plant. Various chemicals are introduced to the process stream to break down the wood to make pulp. Spent chemicals are recycled for future use to help reduce waste and create a more sustainable process. A critical component—elastomeric expansion joints—ensure the piping and equipment run effectively.
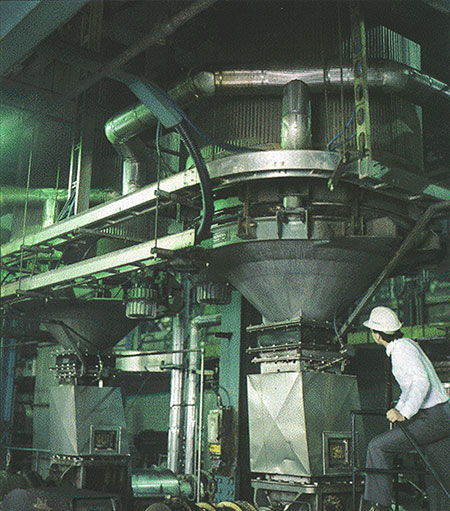
Pulping
Wood logs are first debarked and then chipped into small pieces so they can later be converted to pulp. Blowers and conveyors send the wood chips from the storage silo to the mill, this is the first stage of the process where expansion joints can be used. Raw wood chips are abrasive and require an expansion joint with a filled arch to facilitate flow without chips accumulating in the arch. In addition to a filled arch, the tube elastomer should be rated to withstand heavy abrasion. Ethylene propylene diene monomer (EPDM), hydrogenated nitrile rubber (HNBR) or natural/gum rubber are best suited to handle these abrasive applications. Flow liners, also known as top hat liners, can also be used in this area when the velocity of the wood chips is high enough to damage the rubber liner. A flow liner is a metal insert that controls the flow of high velocity abrasives and protects the rubber tube without impeding the movement and vibration absorbing qualities of the expansion joint.

The pulping process will break down the raw wood chips into separate lignin fibers and leave cellulose, which is the key component to making paper. Chemical pulping is the most common process for today’s products, employing a digester to cook wood chips in white liquor using high pressure steam. Once the digester has completed its cycle, the black liquor waste product is pumped to an evaporator. The other digester byproduct is wood pulp, which must be purified, washed and bleached before it can be made into paper.
Digesters often have expansion joints located on the white liquor supply as well as attached to the wood chip feeder bin. White liquor is a mild chemical that can safely be handled with an EPDM rubber liner. The bins feeding wood chips into the digester are gravity fed and require low-pressure expansion joints that can be manufactured in round or rectangular shapes, depending on the specific equipment setup. With little movement, an arch may not be required as the feeders are mostly compensating for vibration.
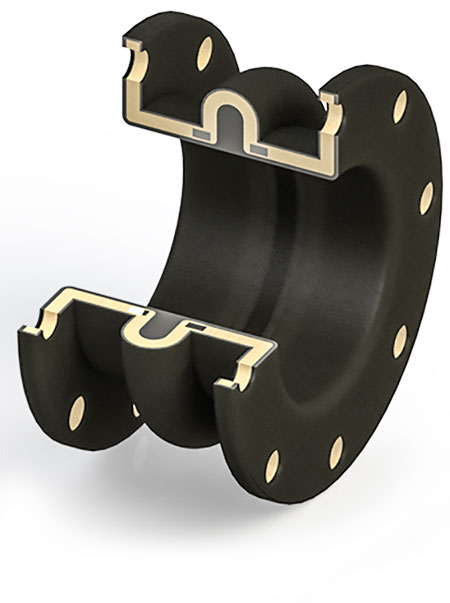
Chemical Recovery
The two byproducts of the chemical process taking place in the digester are wood pulp and black liquor. To reduce waste, black liquor is sent to an evaporator to burn off excess water, then transported to a recovery boiler. The recovery boiler further burns the highly concentrated black liquor and is left with a residue known as green liquor.
Once green liquor is made, it is then combined with lime and recycled back into white liquor. With the white liquor reproduced from the byproducts of this process, it can be reused at the start to break down raw wood chips. The cycle is repeated continuously, known as the Kraft process.
Expansion joints are fitted in the intricate piping systems that pump chemicals between the digester, evaporator and recovery boiler together in a safe and efficient manner. This is a critical area to ensure the expansion joint liner material is correctly specified to avoid unexpected failure. The white, black and green liquor can be handled safely with the liner materials summarized in the below table. Because some of these chemicals are cooked at high temperatures, liner materials may need to be specified to handle the chemical at the elevated temperature.
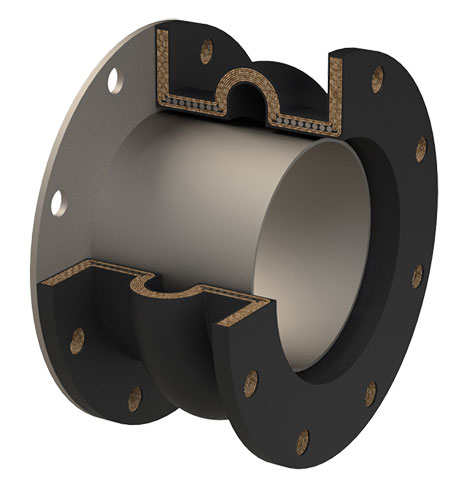
Bleaching
The wood pulp slurry that exits the digester is forwarded to a washer unit that cleanses the pulp from any remaining black liquor residue. A screener unit will further remove any impurities such as bark, stones or any other foreign objects.
Pulp slurry, at any point in the cleansing stages, has a high concentration of solids and is another example where an abrasive resistant liner is critical for the expansion joint. Natural/gum rubber, EPDM or HNBR are acceptable liner materials. In addition, a filled arch and/or flow liner configuration are ideal additions to avoid buildup of pulp material in the arch.
For products that require bright white appearance, bleaching agents are added to the pulp mixture. This is another area where it is critical that the proper liner compound be specified. Most bleaching agents can easily deteriorate some elastomers upon contact. In the bleaching lines, fluoroelastomer (FKM) or polytetrafluoroethylene (PTFE) lined expansion joints are the optimal materials to be specified.
Paper Machine
Paper machines then convert the purified pulp into the finished product. The machine itself is complex and incorporates a great deal of piping and pumps to circulate water through each stage. The process starts at the head box, where pulp slurry is pumped in from the blend chest to be prepared for drying and finishing.
The blended stock flows through the wet end of the paper machine and vacuum systems remove water from the slurry. The water vacuumed out of the stock gets transferred to a seal pit. With mainly water extracted from the slurry, general purpose liner materials are sufficient, but it is important to specify an expansion joint with full vacuum rating. With water now evacuated from the pulp slurry, the dry end of the paper machine starts to form the dried pulp into its final form. Presses operate on the dry end to start forming sheets, which are then fed through a series of rollers. This area also has piping fitted with expansion joints handling various penetrating liquids, surface coating materials and dyes for colored products. Depending on the final product, additives will give the paper the desired surface characteristics and physical properties. Pumps are also used to handle overflow of these solutions to be recycled.
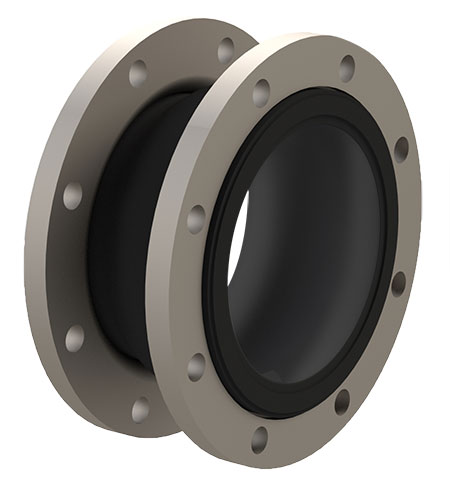
General Applications
In general, a paper mill has fluid sealing needs beyond those highlighted as part of the pulp and paper making process. There are generally water treatment plants, powerhouses and water supply pumps that support the facility. Applications in these areas are widely considered as general use as the media is typically water at ambient temperatures.
Some examples of general use are, but not limited to, spherical expansion joints, which come in standard sizing and materials. Spherical expansion joints typically come furnished with floating metal flanges that are ideal for quick installation and inventory reduction when compared to integrated rubber flanges with retaining rings.
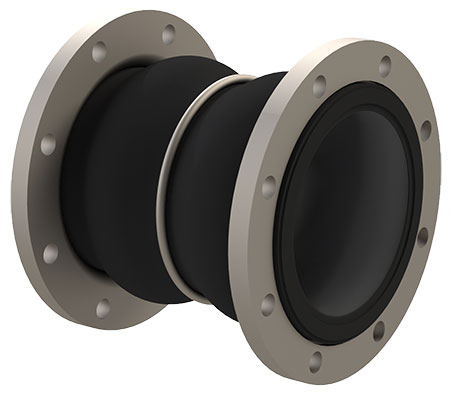
The pulp and paper industry uses complex equipment to manufacture important products. Elastomeric expansion joints are a means of ensuring equipment in a paper mill runs efficiently and reduces wear that can be caused from thermal pipe stresses and vibration. The expansion joints that are specified in these applications should take into consideration media, temperature, movement, pressure and vacuum requirements to ensure a safe and leak-free operation.
We invite your suggestions for article topics as well as questions on sealing issues so we can better respond to the needs of the industry. Please direct your suggestions and questions to sealingsensequestions@fluidsealing.com.