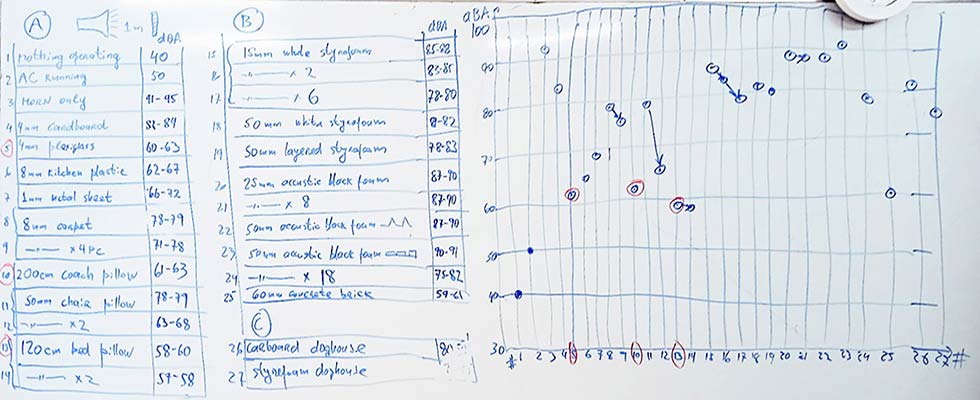
Every piece of rotating machinery vibrates, and the noise it emits is a result of vibrations propagating through the air, attachments, baseplates, frames, pipes, etc. But how bad is really bad?
For the sound/noise, no such standards relating sound to reliability exist, and the max levels are usually set by the Occupational Safety and Health Administration (OSHA), or a similar standard, to protect human hearing. For example, an 85 decibels A (dBA) level of sound pressure is typically what OSHA considers safe, and the pump manufacturers are guided by these rules.
When an experienced mechanic old-timer touches a pump and says it is “running rough,” they are usually right, as years of field experience often beat the most sophisticated vibration analyzer. Or, when they hear a pump and call it “noisy,” they are also right and some issue is likely in the making.
However, even a small level of vibrations could potentially cause a serious problem even though, technically speaking, the level could be well within what is allowable. This may not be a concern for most cases with a typical motor-to-pump attachment, piped and set on a baseplate, receiving cooling water from a tank and pushing it on to cool a process. But, when a pump is installed inside a frame with multiple filters, gauges, monitors, etc., things may look very different. Tiny tubing connecting pressure or temperature gauges to pipes may have multiple natural frequencies of vibrations, and even a small exiting force can, over time, cause fatigue and failure, leaking fluid (possibly a dangerous chemical) to the environment with potentially dangerous consequences.
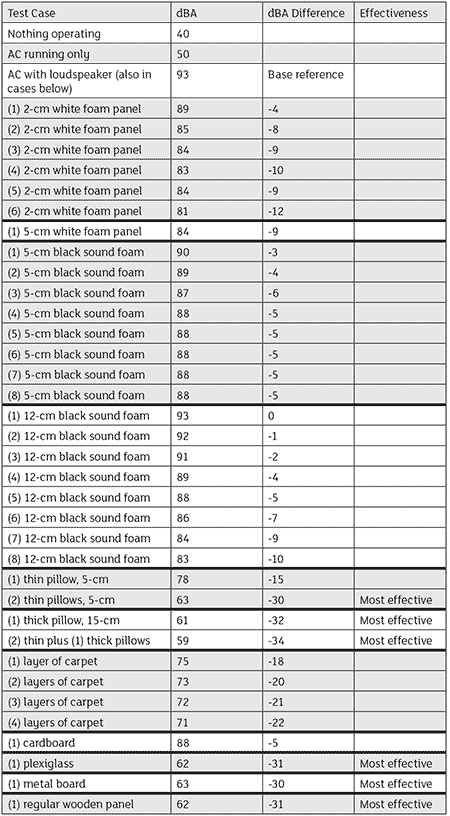
To isolate such systems, and to prevent failures, various methods are used such as dampeners, soft pads under the equipment mounting feet, etc. And if noise is an issue, sound enclosures (dog houses) are built around the pump (and/or motor) and flexible piping connections, if possible and allowed, are used.
Some types of pumps are predisposed to run noisier than others. For example, a gear pump would typically be noisier than a centrifugal pump for the same operating parameters. Regardless of how thick a fluid film of the pumpage is, it still cannot fully prevent contact between meshing gear teeth and, thus, makes noise. And this noise, even if not harmful to a human ear, is an indication that somewhere inside the pump, vibrations are also being emitted and may find some part of the system to “tune in” into this frequency and fail (fatigue) over time.
From a noise isolation standpoint, several materials are available and used in the industry. These range from industrial heavy-duty materials (often not recommended for residential use, i.e., chemical compositions not compatible with proximity to humans) to simpler and safer material for residential applications. These can reduce the noise by 10 dBA easily, which is considered a minimum level of noticeable reduction of noise.
Others can extend this reduction by 20 or even 30 dBA. If you can find a material to reduce noise by 40 dBA, you have probably reached the level of unobtainable.
The key to the characteristics of the noise reduction material is two factors: density and fluffiness. A heavy winter blanket, for example, wrapped around your bedroom window can probably reduce outside street noise by 10 to 15 dBA and turn your sleepless nights into a refreshing eight hours of sleep.
Our Pumping Machinery Research Center has conducted a simple, but interesting, study of several readily available materials to see how well they can reduce the sound pressure and make operation quieter. These results can be seen here.
Those of you who may have questions about how to turn these materials into “dog houses” for the pumps, to make them less noisy, let us know. And for those who try to turn their bedroom into a quieter place, let us know how well it worked for you, by how many dBA you were able to reduce the background street noise, and how your design looked (a simple blanket cover or an additional window frame, etc.).